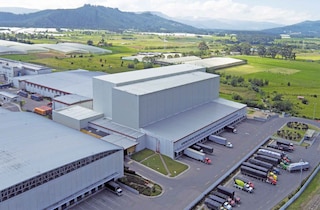
Warehousing logistics: definition, objectives and areas of work
Within a company’s supply chain, warehousing logistics encompasses activities related to the correct storage, protection and conservation of goods in an installation for the period of time required. It also involves the management, transport, location, handling and conditioning of this merchandise from receipt to dispatch.
The warehouse is the key element that enables you to regulate the flow of goods between supply and demand. It is here that the management of the materials that a business moves, stores and handles is concentrated to respond to commercial and production needs. Installations, thus, are the cornerstone of warehouse logistics.
Warehousing logistics objectives
The ultimate goal of warehouse logistics is to minimise operating costs while maintaining quality service. It aims to achieve the best combination of the following actions:
- Maximise the use of storage space.
- Ensure optimal organisation of the workforce.
- Leverage handling equipment.
- Guarantee access to goods when they are requested.
- Maintain the security measures necessary to preserve the integrity of the goods.
Logistics managers work in each area of warehouse logistics to meet these objectives.
Warehousing logistics: areas of work
At the heart of warehousing logistics is the installation. The main activities carried out there are the receipt, storage, preparation and dispatch of goods. For all these operations to be performed effectively, each aspect needs to be optimised. Let’s take a look at the key points to take into account:
1. Warehouse layout design
Square one for designing an installation and, thus, achieving optimal warehouse logistics management, is to prepare its layout. The strategy for doing so will vary depending on whether you’re creating a new facility or reconfiguring an already up and running warehouse.
This design will be conditioned by several major factors, including:
- Volume and characteristics of the products to be stored.
- In-warehouse stock turnover and material flows.
- Storage space available and site limitations.
- Makeup, organisation and qualifications of the work team.
- Corporate management system followed and whether or not you use a warehouse management system.
- In addition, when renovating the current layout, you need to consider the storage systems and handling equipment already available.
The layout design must always start with an exhaustive analysis of your company’s needs. As a baseline for warehousing logistics, this is approached with a long-term view, anticipating possibilities for growth that the installation might have.

2. Materials management: handling equipment and storage systems
Materials management refers to the set of operations involved in preparing, locating, moving and storing products. It is, therefore, an essential element in warehouse logistics management. Goods handling results from the interaction between operators, machines, racks and working methods involved in moving, storing and controlling materials.
- Storage systems
There’s a huge variety of industrial racks for warehouses available for both pallets and boxes. You should choose your storage system based on the following criteria:
- Type of product and its unit load.
- Target storage capacity.
- Desired agility of operations.
- Costs and available financing.
Before making your choice, it’s advisable to discuss the possibilities offered by each option with the supplier. In our Technical Warehouse Manual, you’ll find an example of how to calculate and compare the capacity of each rack.
- Handling equipment
The amount and type of handling equipment determine the installation’s throughput and the operators needed for it to function efficiently. These machines can also affect the layout distribution due to, for example, the height they reach or the width of the aisles in which they operate.
Handling equipment is divided into:
- Manually controlled devices: these include traditional forklifts, order pickers and pallet lorries, among others.
- Automated systems: these refer to automatic machines run by control software in direct communication with warehouse management software. Examples of these systems include stacker cranes, conveyors, electrified monorails and transfer cars, among others.
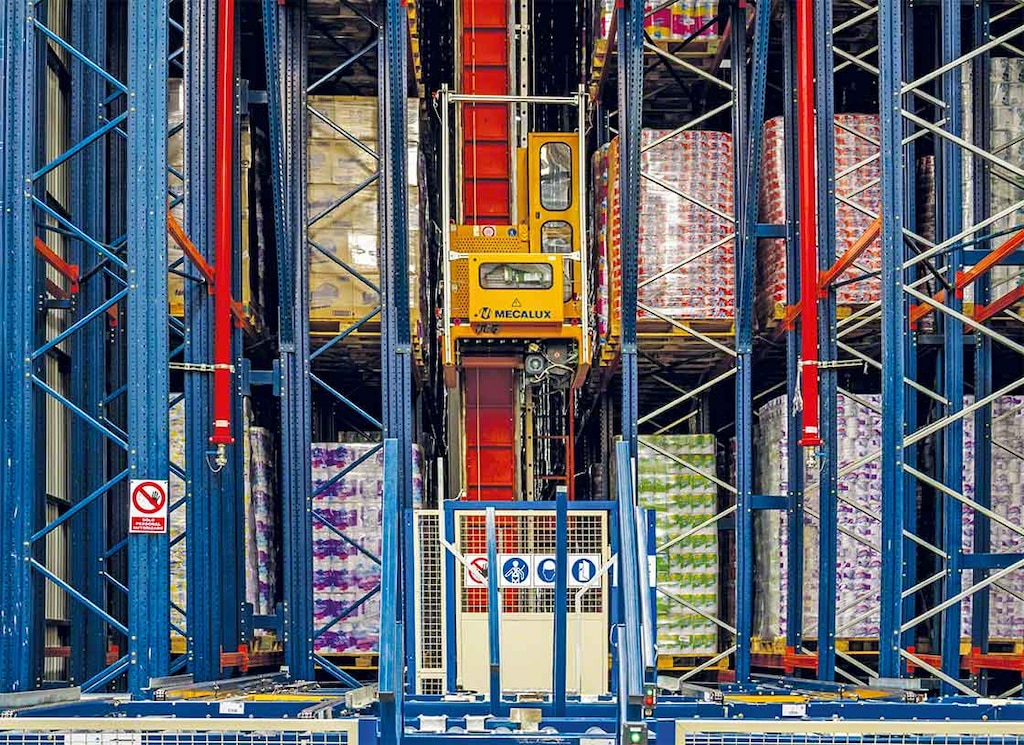
3. Picking and order preparation
Picking processes have a considerable impact on certain warehouse logistics strategies. These include the movement and extraction of products from the racks as well as order sorting, consolidation, packing and dispatch.
The organisation of picking is one of the major areas of work in warehouse logistics. There are many different methodologies, depending on the following factors:
- Height of the racks from which products are picked: floor, low, medium and/or high level.
- Direction of goods movements: whether the operator goes to the goods or the goods are brought to the operator via automatic systems.
- Picking method used for different products: discrete (order-by-order), batch, zone, wave and/or pick-to-cart picking, among other types.
To find the most effective picking method for your installation, you need to analyse in depth your warehouse’s activity and the goal you want to achieve in terms of handling costs (number of orders processed per day per time unit).
4. Stock and inventory management
Within warehousing logistics, stock management is the area tasked with regulating and optimising stock levels in the installation. To do this, computer programs that accurately track inventory movements are usually used.
This is carried out with the following tools:
- Data reading and transmission devices: radiofrequency terminals and other systems, such as voice picking and pick-to-light, serve as the link between the computer system and the physical world.
- Warehouse management system: this software organises all operations in the installation, together with your company’s ERP (Enterprise Resource Planning), which houses the common database. WMSs can optimise location assignments, picking operation arrangements and movements, among other actions. They also guarantee real-time inventory and assist with all document management tasks.
Thanks to these elements, it’s possible to set up a traceability system. This identifies the various stages a product goes through in the warehouse and, thus, provides you with comprehensive control over material flows.
5. Warehouse safety
In the daily management of an installation, both the logistics staff and merchandise in stock are exposed to a series of risks. Therefore, safety is something that absolutely cannot be ignored when it comes to warehousing logistics. It should be addressed in three areas:
- Prevention of occupational risks for operators: work in installations involves repetitive movements, manual load handling, long periods of standing, etc. A weary operator tends to make more mistakes and be less productive. So, it’s a good idea to perform a job safety analysis (JSA) and provide workers with tools and automatic systems that help them to fulfil their tasks more comfortably and ergonomically.
- Goods security systems: both the nature of the stock and misuse of automatic systems and manual handling equipment can have the potential to damage the installation and goods as well as harm operators. Therefore, it’s advisable to post signage throughout the warehouse, establish traffic rules and draw up good practices for operating equipment.
- Maintenance: for safety reasons, it’s also vital to carry out proper maintenance of the installations and devices. Thus, a mandatory technical inspection of the racks must take place periodically.
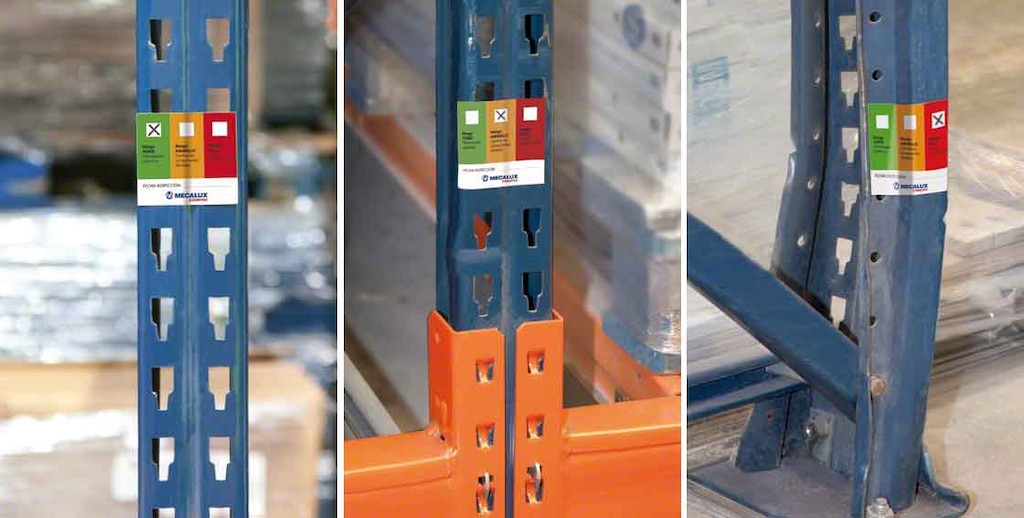
Achievement of effective warehousing logistics
As we’ve seen, warehousing logistics has its own organisational rules and specific areas of work that revolve around a set of common objectives. Knowing how to master this science isn’t easy — even less so in today’s logistics scenario, in which variability and new purchasing habits are transforming the ways warehouses are operated.
To optimise the management of your installation, we encourage you to continue consulting our specialised blog. And, if you’re looking for a trusted partner to implement your logistics projects, we encourage you to contact us. We’ll put at your fingertips over 50 years of experience in the warehousing logistics sector.