The pallet rack capacity information compared in this article can be used to identify the most appropriate system to provide the best physical capacity ratio. However, physical capacity is not the only criterion to be taken into consideration. There are other equally essential factors, such as the speed of handling the pallets with one specific configuration or another.
On the other hand, the physical capacity of a warehouse (the maximum number of pallets that can be stored at one time) is not always the same as its effective capacity, which is merely that which can be obtained in a normal working cycle, in accordance with the maximums and minimums for the SKUs and the space required for each. Here, the positioning system used is vital.
The specific positioning system requires a certain number of spaces to be reserved for each SKU, except for those that can share positions with others. When goods enter a warehouse, all available spaces are filled but are then emptied as the orders are prepared. Given that these are reserved and cannot be filled with other SKUs, the effective capacity will be lower than the physical capacity. Specifically, the effective capacity will be the minimum stock plus half of the difference between said minimum stock and the number of spaces assigned to that SKU. Effective capacity with these specific positioning systems is between 55% and 65% of real capacity.
When working with random positions, the management system assigns positions to the pallets, which will be stored at random in any empty space. The WMS records the position and provides it to the operator when necessary. In this case there are almost no empty spaces, so the effective and physical capacities will be very similar (between 80% and 92%).
Unless these differences are taken into account, the solution chosen for the warehouse may not be the correct one. While any system can operate with the two positioning types mentioned, compact storage systems, for example, are inflexible. They can provide greater physical capacity than other systems, but they may actually provide lower effective capacity.
To illustrate the differences that can arise in installations when using one storage system or another, the following is a hypothetical example of a warehouse with specific measurements and a particular unit load. Different solutions (configurations and handling equipment) are offered for this hypothetical case and the results of using each method are shown.
Capacity is calculated on the basis of the surface area and defined for a storage level, since height is a variable that depends on the building itself and the lifting height of the forklift. To help with the comparison, the space required for the reception and dispatch areas has not been taken into account either. The unit load chosen is a 800 x 1,200 mm pallet (Euro pallet), which in the pallet racking system means that up to three of these pallets can be stored in each 2,700 mm wide space.
The capacity (and therefore, the occupied capacity) is specified per level, i.e., by the surface, not by the total volume of the installation.
Unit load: 800 x 1,200 mm pallet.
Example 1. Pallet racks with counterbalanced forklift. 594 pallets per level. |
System: pallet racks. Aisle: 3,400 mm. A minimum 3,600 mm between racking units. Handling equipment: counterbalanced forklift Capacity obtained: 594 pallets per level. |
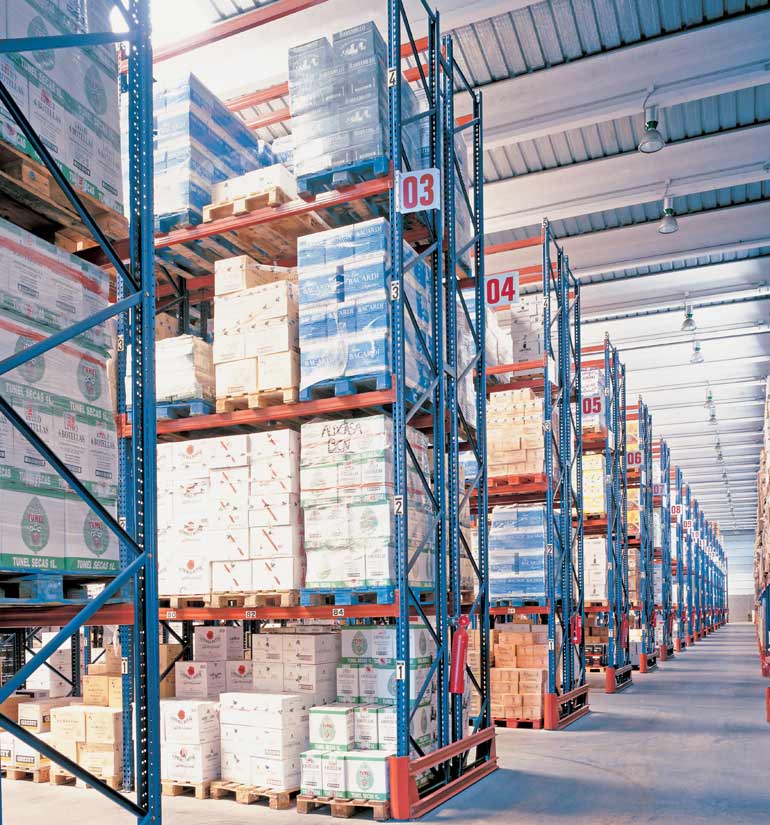
One company's distribution warehouse.
Example 2. Pallet racks with reach trucks. 678 pallets per level. |
System: pallet racks Handling equipment: reach trucks Aisle: 2,750 mm. A minimum of 2,850 mm between the racking units. Capacity obtained: 678 pallets per level. |
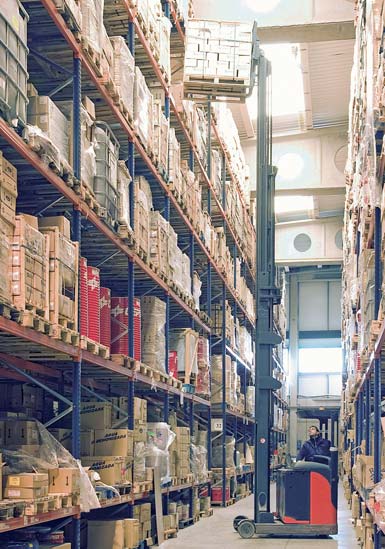
Warehouse of a logistics operator.
Example 3. Pallet racks with trilateral turret truck or stacker crane. 840 pallets per level. |
System: pallet racks. Handling equipment: trilateral turret truck or stacker crane. Aisle: 1,700 mm. A minimum 1,800 mm between racking units. Capacity obtained: 840 pallets per level. Please note: A stacker crane can work in a 1,500 mm wide aisle between loads, so the width of the space available in the example would be 40,000 mm instead of 42,100 mm to obtain the same result. |
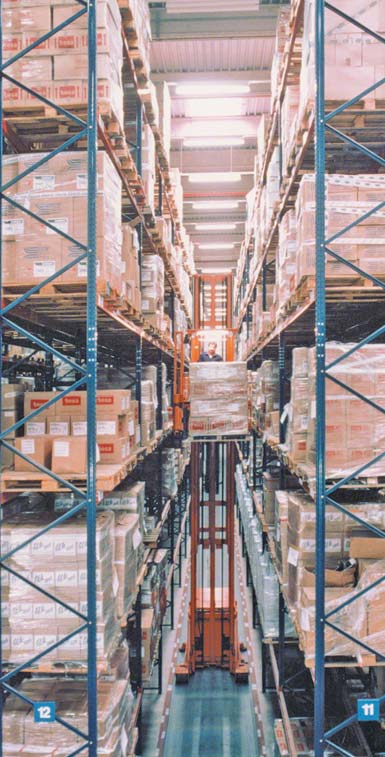
Trilateral turret truck run warehouse.
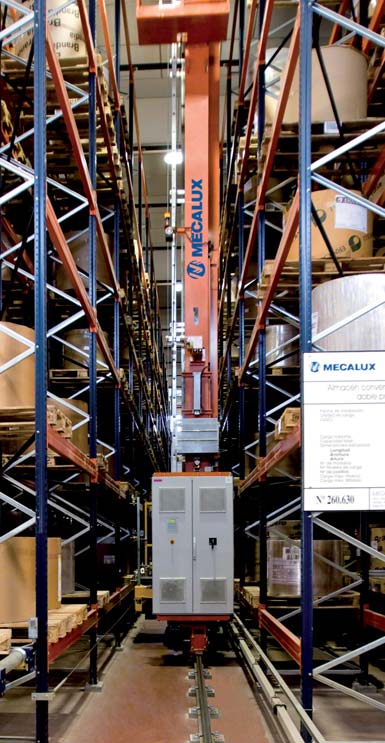
Automated paper reel warehouse.
Example 4. Pallet racks with double-deep stacker cranes. 1,008 pallets per level. |
System: double-deep pallet racks. Handling: stacker crane. Aisle: 1,500 mm. A minimum 1,600 mm between racking units. Capacity obtained: 1,008 pallets per level. Please note: as in example 3, for this installation the warehouse would be 40,000 mm wide instead of 42,000 mm. |
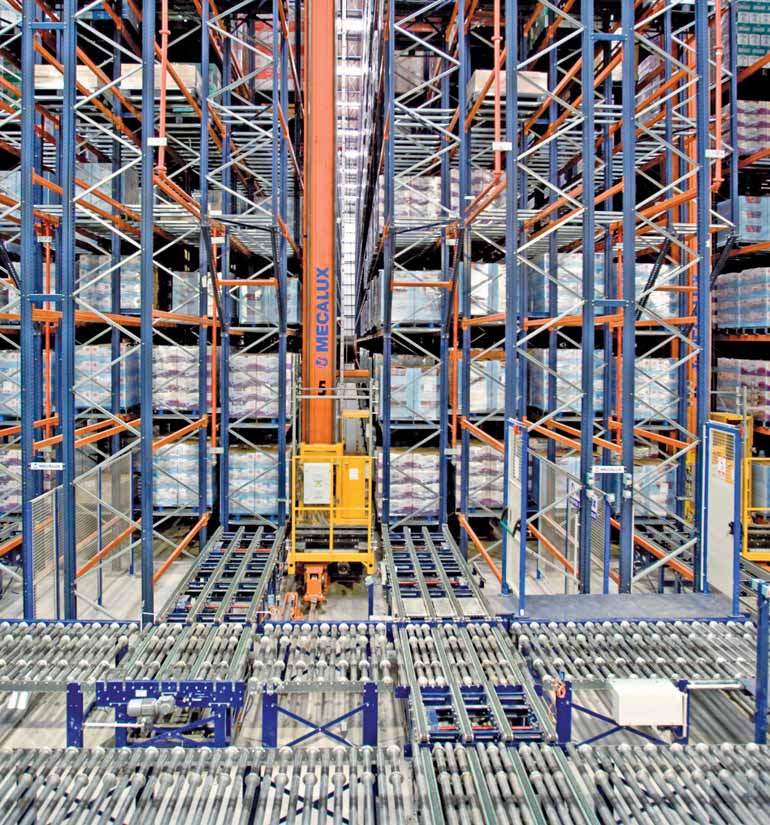
Consumer products warehouse.
Example 5. Pallet racks on mobile bases. 1,144 pallets per level. |
System: pallet racks on mobile bases. Handling equipment: forklifts. Aisles: two, each 3,750 mm wide. Two forklifts can pass each other (observing suitable margins). Capacity obtained: 1,144 pallets per level. |
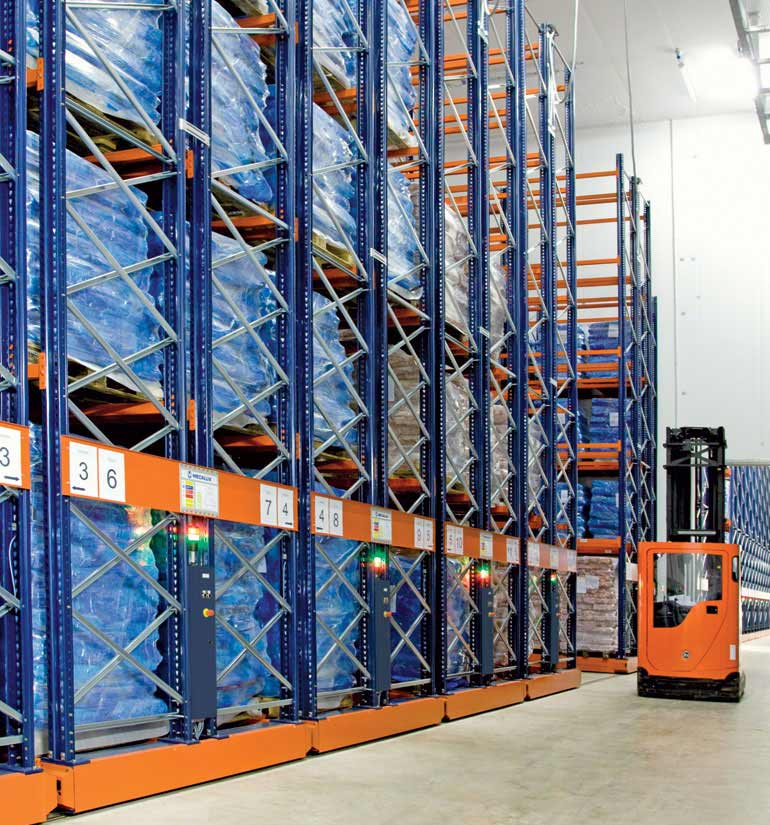
Frozen meat warehouse.
Example 6. Drive-in pallet racks. 960 pallets per level. |
System: Drive-in pallet racks. Handling equipment: forklifts Aisle: 3,500 mm wide, where two forklifts can pass each other. Capacity obtained: 960 pallets per level. |
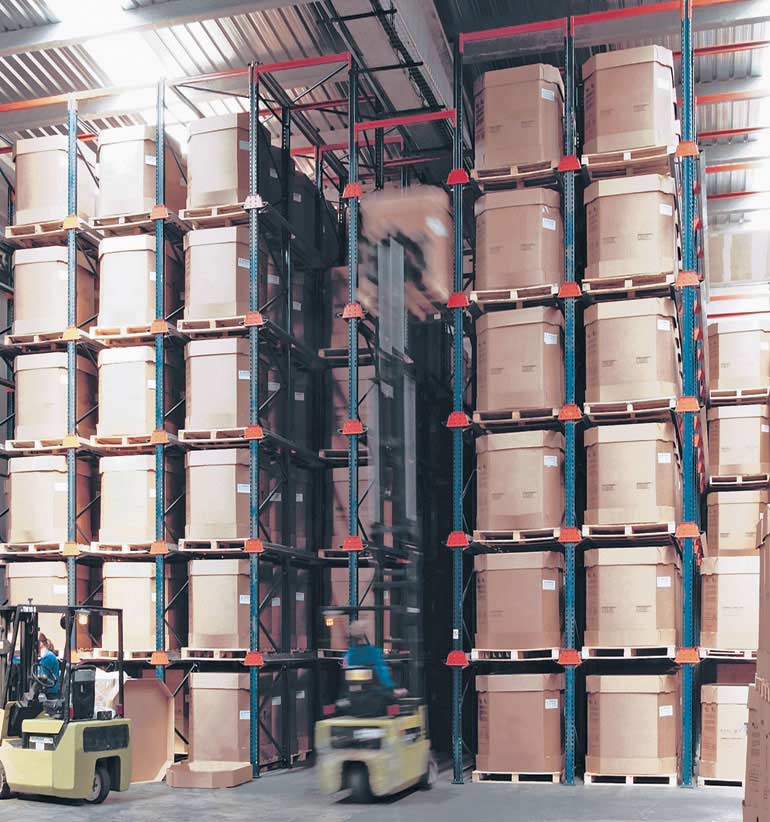
Example 7. Push-back with trolleys. 848 pallets per level. |
System: push-back with trolleys. Handling equipment: forklifts. Aisle: At least 3,500 mm. Capacity obtained: 848 pallets per level. |
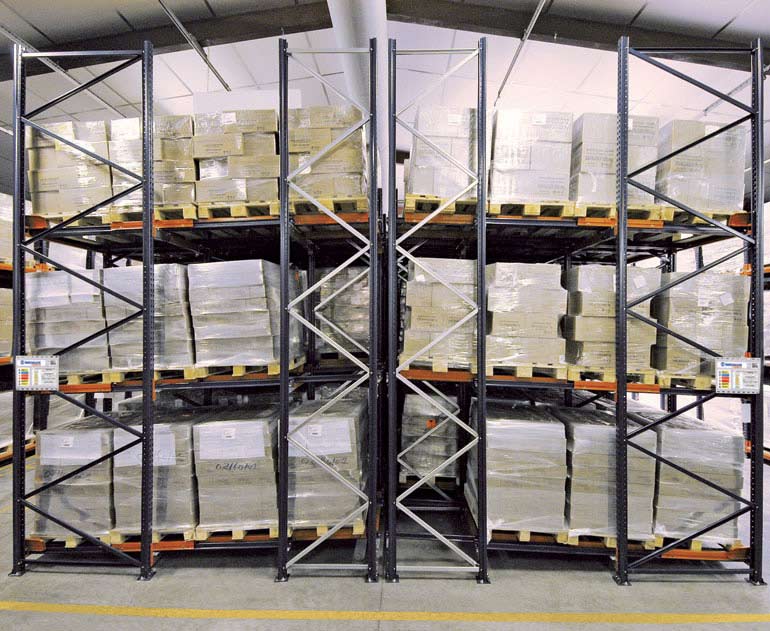
Example 8. Push-back with rollers, 893 pallets per level. |
System: push-back with rollers Handling equipment: forklifts. Aisle: At least 3,400 mm. Capacity obtained: 893 pallets per level. |
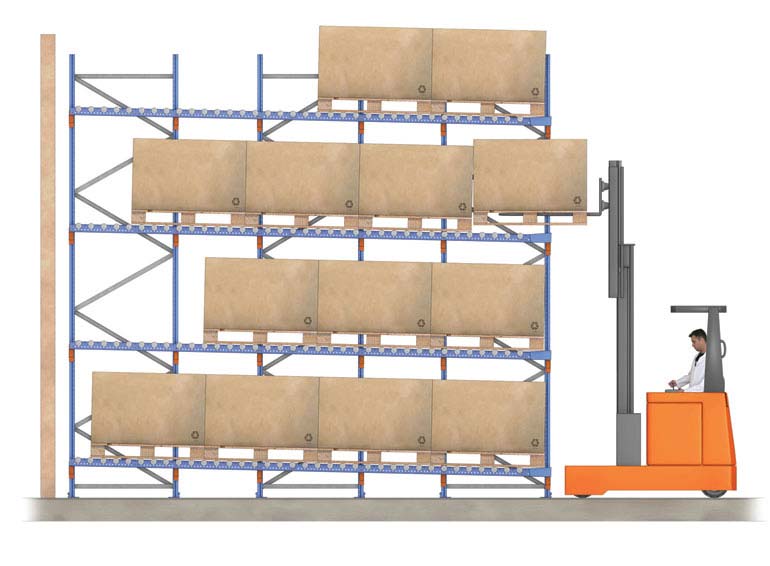
Example 9. Pallet racks with Pallet Shuttle. 1,080 pallets per level. |
System: pallet racks with Pallet Shuttle. Handling equipment: forklifts. Aisle: At least 3,500 mm (space for two forklifts to pass each other). Capacity obtained: 1,080 pallets per level. |
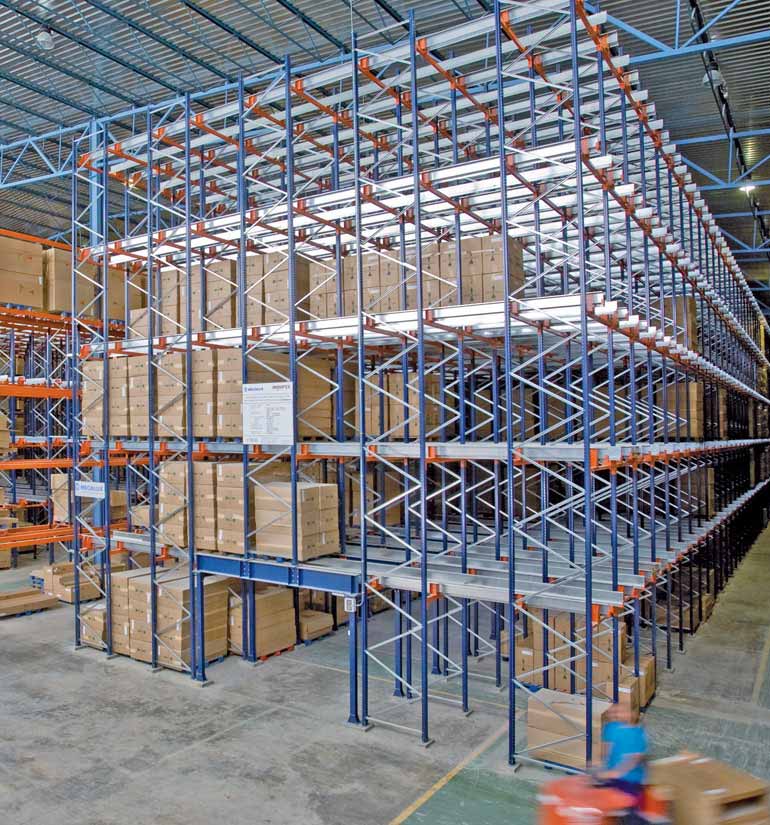
Furniture kit company.
Example 10. Live pallet racks. 910 pallets per level. |
System: live pallet racks. Handling equipment: forklifts. Aisle: At least 3,400 mm. Capacity obtained: 910 pallets per level. |
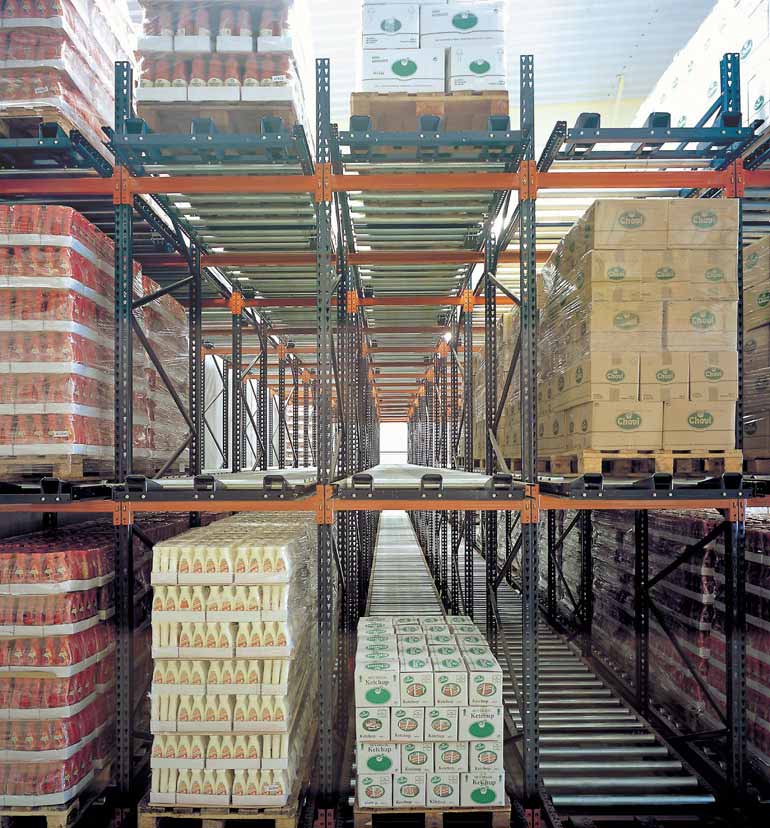
Juice making business.
Comparative table of physical capacities |
|||
Storage system | Pallets per level | Surface area for pallets | Ratio (proportion of the site filled with pallets) |
Pallet racks with counterbalanced forklifts | 594 | 570 m2 | 32.2 % |
Pallet racks with reach trucks | 678 | 651 m2 | 39.2 % |
Pallet racks with trilateral turret trucks or stacker cranes | 840 | 806 m2 | 45.7 % |
Double-depth pallet racks operated by stacker cranes | 1,008 | 968 m2 | 54.9% |
Pallet racks on mobile bases | 1,144 | 1,098 m2 | 62.2 % |
Drive-in pallet racks with reach trucks | 960 | 992 m2 | 53.8 % |
Push-back with trolleys | 848 | 814 m2 | 46.0 % |
Push-back with rollers | 893 | 857 m2 | 48.0 % |
Pallet racks with Pallet Shuttle | 1,080 | 1,037 m2 | 58.8 % |
Pallet flow racks | 910 | 874 m2 | 47.6 % |
Volume capacity is not linear since there are always other influencing factors, like the useful height of a warehouse and the optimisation of the height of the pallets. Another determining factor is the constructive system, since the flow racks produce a height loss due to the slope this system uses; in the double-depth installations with stacker cranes there needs to be a larger separation between the levels, for example; and in other cases support profiles are required and a specific height in level one.
This table is for informational purposes only and refers to the physical capacity only, not the effective capacity.