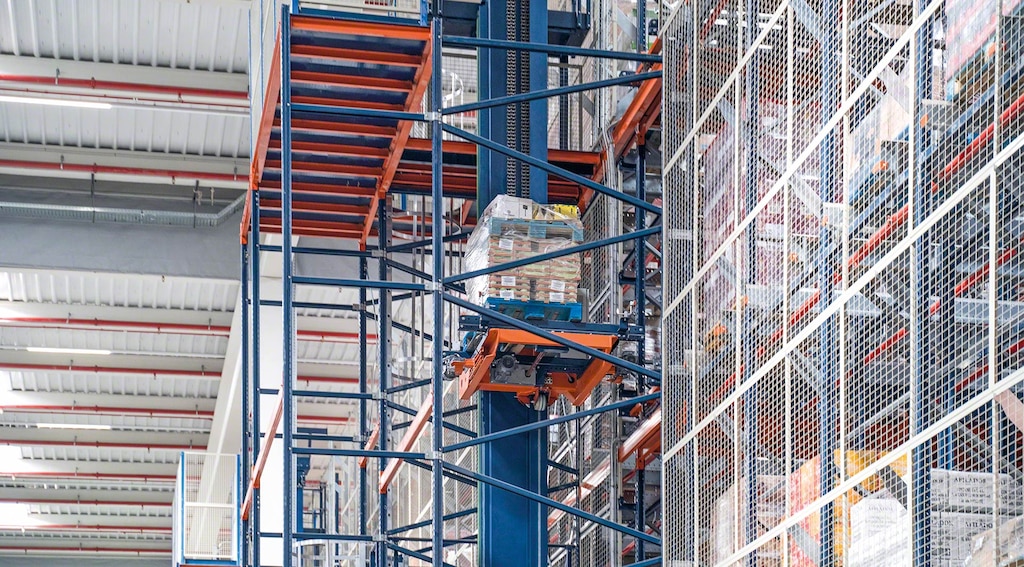
Vertical conveyors (pallet elevators)
Vertical transport system that automates pallet lifting and lowering to overcome heights and streamline the internal flow of goods.
The product
Automation of vertical pallet movements
Vertical conveyors are automatic lifts designed to ensure the smooth movement of palletised loads between a facility’s various floors or storage levels. They enable the controlled, stable transport of pallets to the desired height.
Mecalux’s elevators are highly robust systems that integrate easily into automated and conventional storage systems. Equipped with an electric motor and a conveyor for accurate load transfers, their implementation ensures the continuous internal flow of pallets. Moreover, pallet elevators boost productivity by reducing transport times.
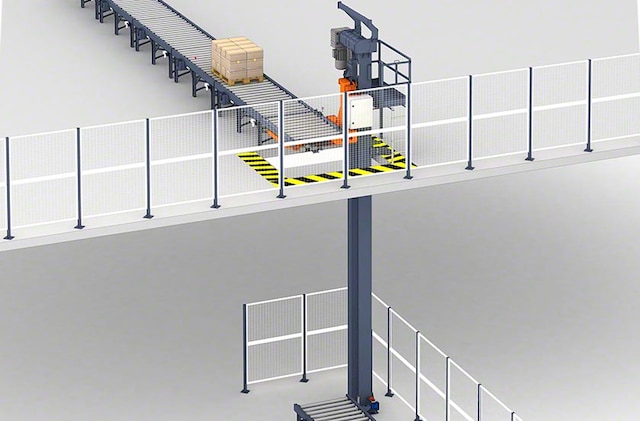
Advantages of pallet elevators
- High-bay capability: this multi-level solution lifts pallets up to 40 m in height.
- High load capacity: thanks to their robust construction, vertical lift conveyors can transport pallets weighing up to 1,500 kg.
- Great speed: pallet elevators expedite the vertical transport of palletised loads. They can achieve speeds of 80 m/min for maximum payloads of 1,000 kg and 60 m/min for payloads of up to 1,500 kg.
- Easy integration: their compact single-mast structure occupies little space, making them adaptable to different layouts and warehouse configurations (with conveyor lines, electric monorail systems, etc.).
- Safe operation: pallet elevator lifts raise and lower pallets in a stable manner, safeguarding the integrity of the goods transported.
- Wide temperature range: vertical conveyor systems can operate in both low and high temperatures (from -30 °C to 40 °C).
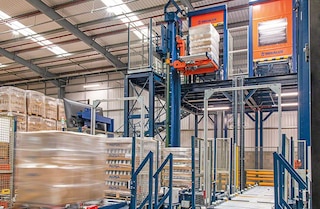
Thanks to the automatic vertical conveyors, flows are much faster
Pallet elevator applications
High-throughput solution for transporting pallets vertically in all types of facilities
Vertical conveyors are designed to work in multiple scenarios. Their implementation speeds up movements of palletised loads in intralogistics operations that require goods to be transported along various levels.
Case studies
See more case studiesFAQs
Vertical conveyors, also commonly known as pallet elevators, are devices that automate the process of lifting and lowering palletised loads in certain intralogistics operations.
Vertical conveyor lifts can reach up to 40 m in height.
A pallet lift conveyor can support payloads of up to 1,500 kg.
Vertical conveyors travel at a maximum speed of 80 m/min with payloads of up to 1,000 kg and 60 m/min with payloads of up to 1,500 kg.
Mecalux’s vertical conveyors are compatible with the main types of pallets available in the market. These range from Euro-pallets (800 x 1,200 mm, 1,000 x 1,200 mm and 1,200 x 1,200 mm) to North American (GMA) pallets measuring 48" x 40".
The single-pallet elevator incorporates a roller or chain conveyor. The choice of conveyor employed will depend on the direction of movement and the type of pallet handled.
Pallet elevator systems are primarily used to overcome height differences and transport pallets between the different floors of any kind of warehouse. They are also installed to move pallets between storage levels in certain automated storage and retrieval (AS/RS) systems. Another application involves connecting the upper levels of high-bay storage structures such as mezzanine floors and pick modules.
Stacker cranes are machines designed to store and retrieve pallets automatically. They move along the height and length of the storage aisle, carrying out translation and elevation movements simultaneously. Their telescopic forks enter the racking structure to place and remove pallets autonomously.
Pallet elevators or vertical conveyors, on the other hand, were designed to perform a single movement: to transport palletised loads vertically. Nevertheless, they can also be employed in automated systems such as the 3D Automated Pallet Shuttle. In this AS/RS, they move pallets between the racking block’s input/output stations and the various storage levels. In this solution, the 3D shuttle moves along the aisles to store and retrieve pallets.
Generally, in an AS/RS requiring pallet elevators — such as the Pallet Shuttle with transfer cars and the 3D Automated Pallet Shuttle — 2 lifts are installed. One is positioned at the input station, while the other is set up at the output station. However, for clients looking to increase the volume of cycles per hour, it is possible to install 2 input and 2 output vertical conveyors.
Ask an expert