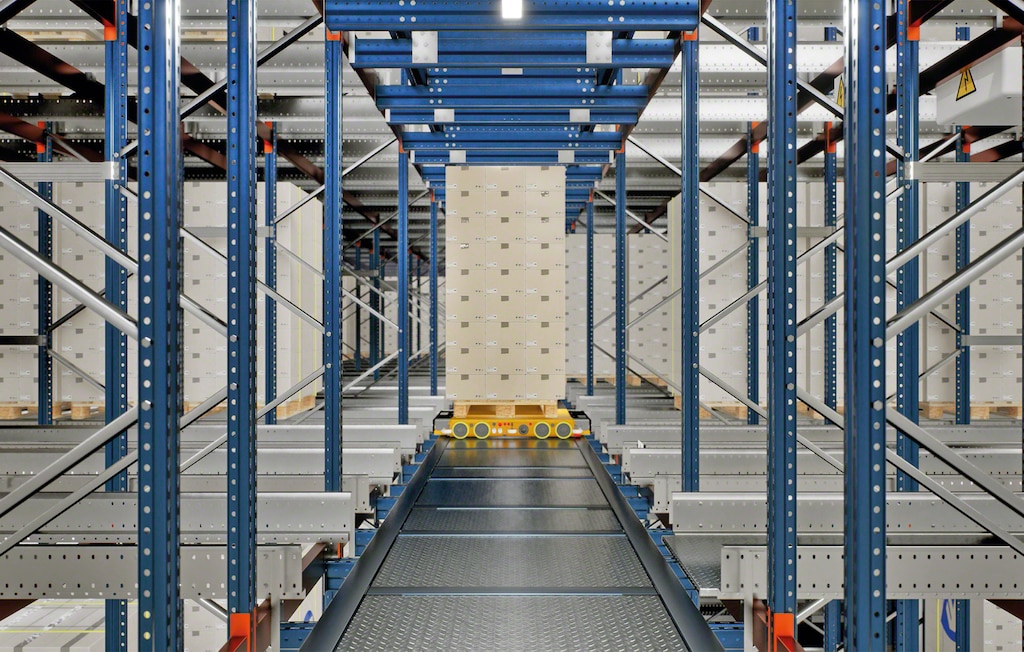
3D Automated Pallet Shuttle
High-density pallet storage system employing autonomous, multi-directional shuttle cars to maximise warehouse capacity, productivity and flexibility.
The product
The ultimate automation solution for maximising high-density storage, productivity and flexibility in an automated storage and retrieval system (AS/RS) for pallets
The 3D Automated Pallet Shuttle is a high-density storage solution featuring an innovative multi-directional electric shuttle. This autonomous shuttle car stores and retrieves pallets from racking with unparalleled efficiency and precision. Notably, these shuttles navigate the aisles and channels within the racking structure independently, eliminating the need for additional material handling vehicles (e.g., stacker cranes or transfer cars). To move between storage levels, the shuttles employ a series of lifts.
Mecalux’s 3D Automated Pallet Shuttle is a cutting-edge AS/RS at the forefront of warehouse automation. In addition to increasing warehouse productivity and optimising space utilisation to boost storage capacity, it provides extraordinary versatility. This flexibility allows businesses to meet the requirements of dynamic scenarios, such as demand peaks and high-priority tasks. Moreover, its completely modular design enables rapid scalability to tailor the AS/RS’s capacity and throughput to business growth.

Advantages of the 3D Automated Pallet Shuttle
- High productivity: the rapid navigation speed and operational versatility of the multi-directional 3D shuttles significantly enhance warehouse performance.
- Maximum flexibility: the shuttle cars move between levels and aisles. Additionally, several shuttles can operate in a single aisle simultaneously. This allows managers to adjust the system’s throughput to changing scenarios, including the execution of priority tasks and the occurrence of demand peaks.
- Greater capacity and diversification: compact storage optimises the use of space to increase warehouse capacity. Moreover, each channel can house more than one SKU and pallet size.
- Autonomous, smart operation: the shuttles move through the aisles and channels without assistance from other material handling vehicles. Mecalux’s fleet management software controls shuttle traffic in the racking structure. This ensures continuous and fluid vehicle circulation, prevents jams and avoids collisions between shuttle cars.
- Operational efficiency and agility: a series of sensors ensure safety and effectiveness in detecting, handling and positioning pallets. Moreover, the design of the wheels and rails enables the shuttle vehicles to run smoothly and change direction with ease and stability.
- Scalability: the AS/RS’s modular design facilitates future expansion tailored to business growth. To increase productivity, new shuttles can be added. Likewise, new aisles and levels can be created to expand capacity.
- Wide temperature range: the shuttles’ ability to operate at low temperatures makes them suitable for cold-storage and freezer warehouses. The implementation of high-density solutions in such facilities provides considerable savings in energy costs.
- Comprehensive solution: Mecalux designs, manufactures, installs and commissions all AS/RS components. These include the shuttles, lifts, racking, conveyors, fleet management software and warehouse management system (WMS).

Applications of the 3D Automated Pallet Shuttle
High-density automated storage and maximum productivity
The 3D Automated Pallet Shuttle is the AS/RS solution best suited to scenarios with intensive loading and unloading cycles or high variability in demand. Its compact design leverages available space, while its versatility makes it adaptable to the requirements of companies in multiple sectors.
How does the 3D Automated Pallet Shuttle work?
The multi-directional movement of the 3D shuttle cars through the racking block greatly enhances the system’s flexibility. This streamlined operation significantly facilitates pallet loading and unloading, making this AS/RS adaptable to various demands.
3D Automated Pallet Shuttle components
In the 3D Automated Pallet Shuttle system, the shuttles and lifts control all pallet movements within the racking structure. This significantly simplifies its design and implementation compared to other high-density AS/RS solutions, as there is no need for additional handling equipment such as stacker cranes or transfer cars.
With its compact design, ample autonomy and high load capacity, the 3D shuttle is the system’s operational powerhouse. Its 12 translation wheels enable its multi-directional navigation as well as agile, stable movements.
The 3D system’s racking consists of compact and robust high-density structures. They stand out for their extensive rail circuit designed to facilitate the multi-directional movement of the shuttles.
Catalogues
3D Automated Pallet Shuttle
Maximum high-density pallet storage and operational productivity
DownloadAsk an expert