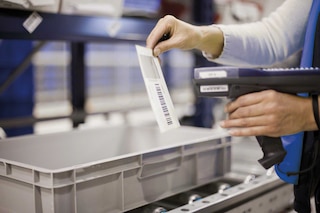
Product traceability: what is it and how is it implemented?
Product traceability has become an essential procedure in industry. Nowadays, logistics centres are responsible for tasks as diverse as location management, order preparation and dispatch, and even product personalisation according to customer demand.
A larger number of SKUs in a warehouse leads to increasingly complex logistics operations. Against this backdrop, poor control of shipping and receiving and of the condition of the goods can result in serious mistakes and cost overruns for the company.
What’s product traceability?
The concept of traceability refers to the tracking of a product throughout its production, processing and distribution phases, from the procurement of the raw materials for its manufacture until it reaches the end customer.
Being equipped with a good product traceability system helps companies comply with:
- Quality assurance: monitoring each process drastically reduces the number of errors produced in an installation, ensuring the utmost quality of the merchandise for end customers. An example of this can be seen in production tasks in a facility. When a material is in bad shape, only by controlling the operation by means of a warehouse management system (WMS) can you trace and identify which final product was made with the affected goods and, thus, quickly withdraw it from the market.
- Hygiene standards: any product traceability procedure should take into account effectiveness and hygiene in every logistics stage. With that in mind, implementing a WMS in the installation makes it possible to find out which product or batch could have been altered because of a drop in hygiene standards (cold loss, spillage, poor preservation, etc.).
- Safety in compliance with current regulations: product traceability makes it easier to verify compliance with the specific legislation for each design, manufacturing and distribution process.
Product traceability and its regulation
Traceability is increasingly common, due to logistics needs as well as customer and supplier demands. In fact, certain sectors already have specific legislation in place to ensure adequate control of product traceability.
This is the case of the food industry. ISO 9000:2005 (2005) highlights traceability as the ability to trace the history, application, or location of a product, adding that traceability can also relate to the origin of materials and parts; the processing history and the distribution.
The US Food and Drug Administration (FDA) has provided companies (and interested consumers) with advice to ensure the traceability of food and feed across all the stages of the supply chain.
But the food sector isn’t the only one that has to guarantee the traceability of its products; this also falls to the pharmaceutical industry. This sector has a special legislative framework in view of the harmful effects that poor-quality drugs could have on society if dispensed.
Thus, the FDA’s Drug Supply Chain Security Act obligates manufacturers, wholesaler drug distributors, repackagers and many dispensers (primarily pharmacies) in the drug supply chain to provide information about a drug:
- Quantity received and supplied
- Transaction and expiry date
- Batch identifier
- Phases and processes the product has undergone in the supply chain
The renowned International Organisation for Standardisation (ISO) includes product traceability in several of its reference standards. For instance, the ISO 9001 standard, recognised in the field of quality management systems, establishes the need to identify and know the status of each product.
Additionally, in 2007, ISO launched the 22205 International Standard for sectors with a greater demand for traceability, such as the food industry. This standard distinguishes companies committed to traceability in the food and feed chain.
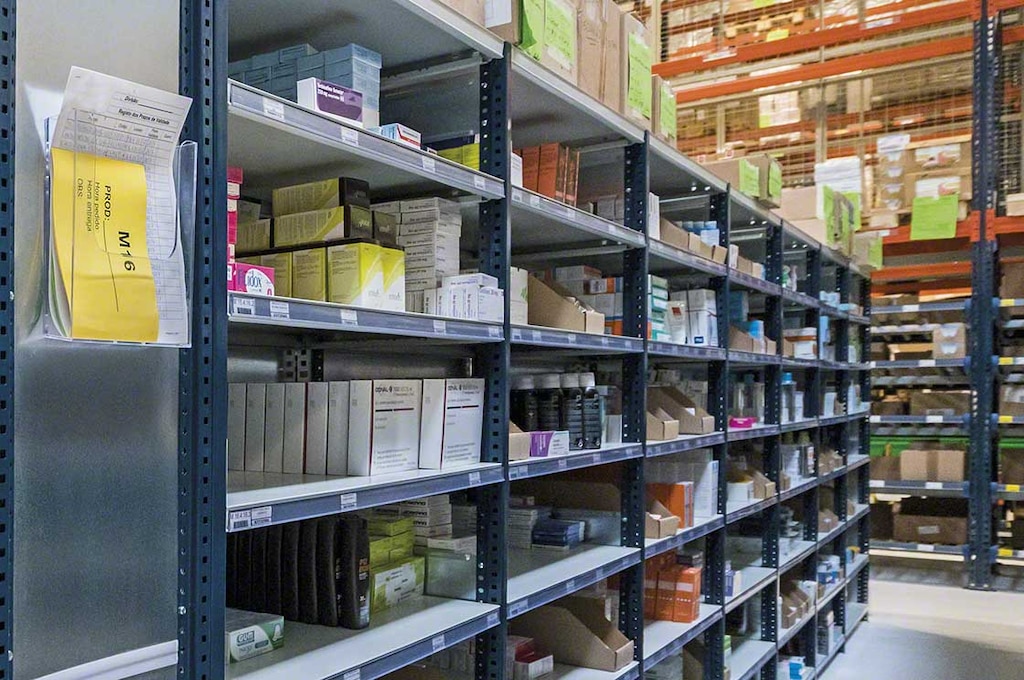
The solution: automated product traceability
In logistics today, more and more stakeholders are demanding to know detailed information on each phase a product goes through in the supply chain. Therefore, traceability requires tools that record information accurately and quickly.
Traditionally, companies have used effective methods for product traceability management that include barcodes or QR codes in goods receipt and dispatch processes in warehouses, especially when these tasks involve multiple SKUs.
However, for less complex operations ― for example, goods receipt or order prep with many items of a single SKU ― other technologies have progressively gained ground, such as RFID, which streamlines processes and multiplies productivity in the installation.
So, how do you manage product traceability without lowering your warehouse efficiency rate? Beyond boosting operational productivity, it’s vital to automate processes — storage and picking, for example — to ensure that both the goods and the employees working in the installation comply with hygiene and safety standards.
Moreover, warehouse automation drastically cuts down on mistakes made in processes. This means you’ll be able to provide your end customers with high-quality, agile, effective service.
In fact, businesses tend to automation with the digitisation of their logistics processes. Implementing a warehouse management system such as Easy WMS from Mecalux in phases such as storage, picking, and dispatch optimises resources and, particularly, stock control in any supply chain operation.