
Warehouse shipping and receiving: the advantages of automated stock control
The objective of managing entries and exits to and from the warehouse is to reflect inventory fluctuations as accurately as possible. Thanks to this, you can know your goods flows inside and out and assess whether the design and operation of the installation are responding efficiently.
In our article, we analyse in depth how to control warehouse shipping and receiving activities effectively to maintain a high level of service. In addition, we’ll examine the advantages offered by a WMS in recording material flows.
Stock inflows and outflows: common challenges
Carrying out thorough, error-free control of inventory receipts and shipments is complicated, especially when done manually (for example, with tools such as Microsoft Excel).
Some of the usual problems include:
- Lack of standardisation in registering goods, or deficiencies in the process.
- Discrepancies between inventory data shown by the system and goods physically present in the installation.
- Absence of a harmonised coding system for all SKUs.
- Mistakes in the inventory data dump shared by the entire company, which complicates procurement management for the purchasing department.
One solution that solves most errors in controlling warehouse inflows and outflows is to rely on a WMS that computerises the data and organises the process automatically.
Warehouse management systems are integrated with identification devices (scanners or radiofrequency terminals, for instance), resulting in a guided, optimised way of working at all times.
Why automate shipping and receiving inventory operations?
To review the benefits of using a warehouse management system to control inflows and outflows of stock from the installation, we’ll take as a basis Mecalux’s Easy WMS.
Overview of inflow control with a WMS
As seen in our article on goods receipts, this warehouse work area is made up of various phases that include the physical movement of products, document verification activities and other tasks performed by operators, such as labelling.
However, in reality, behind every goods receipt is a wide range of possibilities. During this logistics process, questions may arise, such as: what steps should I follow for multi-SKU receipts? How should I handle unscheduled receipts so that they don’t create bottlenecks? And, on top of all this, what if I’m dealing with cross-docking and/or returns?
With a WMS, you’ll be prepared to respond effectively to each situation, maintaining control of warehouse entries and exits at all times. Physically, the software is integrated with systems that transmit information when managing goods receipts. The most common are:
- Pallet checkpoints: in many automated installations goods entries and exits are managed with minimal human intervention. The checkpoints check the pallet status and transmit those data to the WMS (which then dumps them into the ERP database).
- Radiofrequency terminals: operators scan the codes on each container and verify the information, following instructions from the WMS.
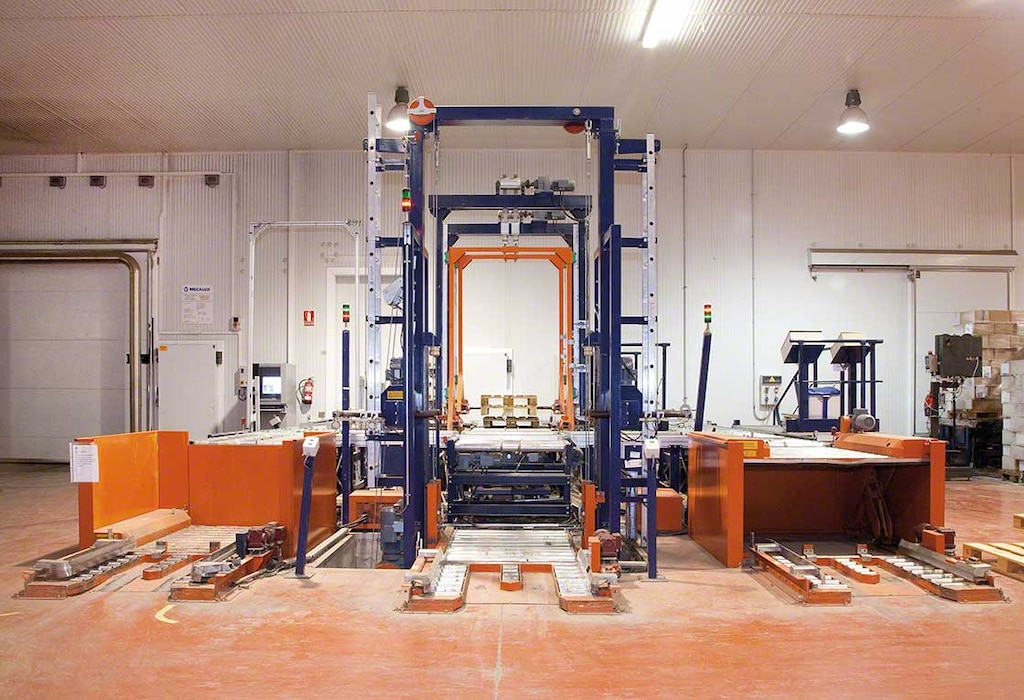
Once the data is entered into the WMS, the system adapts its operations by adjusting tasks to the type of goods received. The WMS either assigns the products received to an entry buffer (temporary storage area) or sends them directly to be slotted, whether by means of automated or manual handling equipment.
Using Easy WMS as a model, these are some of the functions related to the various types of product entries:
- Receipt from the supplier: this is a standard process applied to any kind of goods inflow. This function checks the data in the purchase order against the information on the product label when entering the item into the inventory.
- Receipts of full containers: these are the quickest, as they’re meant for single-SKU goods arriving on pallets. Therefore, the stock is recorded in clusters and the system assigns an automatic identification code to each package.
- Multi-SKU receipts: in contrast with the previous type, this functionality manages inbound pallets containing various SKUs. In this case, each SKU is registered separately.
- Goods pending delivery (also known as advance shipping notice or ASN): the goods entry is planned in advance, so the information has already been transferred from the ERP to the WMS. Although the products aren’t physically in the warehouse, containers are created for them in the system. Once the pallets arrive, the physical and digital data are linked.
- Blind receipts: this enables you to open a stock entry order without having scheduled it in the system in advance. The operator creates it via his/her radiofrequency terminal. The aim is for warehouse activity to continue and for the goods not to cause inflows to become blocked.
Let’s take a look at two specific cases for the control of received goods:
- Returns management: the procedure is adapted to the particularities of inbound product returns. These returns are added to the installation’s inventory and their status is updated throughout the quality control process. Normally, they’re placed in an area reserved for this operation so as not to get in the way of the other tasks.
- Cross-docking operations: the system saves the direct route to the cross-docking location or sends the goods received directly to dispatch (pure cross-docking ). The WMS organises the distribution of this stock, cross-referencing the information with the data on scheduled goods outflows.
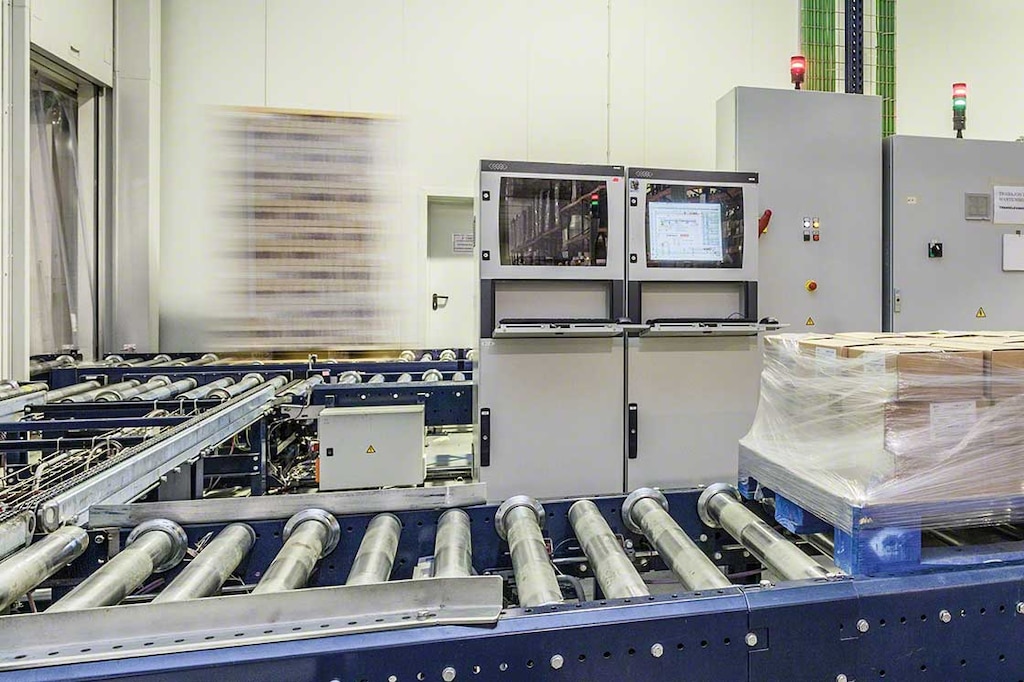
Options for controlling outbound goods with a WMS
Managing outbound flows is of fundamental importance when it comes to warehouse activities. In the end, picking is entirely coordinated around the priority set out in dispatch operations. With WMSs, there are various ways to manage the shipping process.
- Control of exit orders by status: dispatch visibility is vital for the early detection of incidents. Therefore, the system facilitates the identification of each change to the exit order with indications such as: on standby, out of stock, released (its shipping date has arrived), in preparation (it’s already integrated in the picking routes), paused, closed or completed and canceled (if done so for any reason).
- Strategic selection of priorities in exit orders: the system processes a large amount of logistics information linked to shipments in order to subsequently arrange the picking tasks. For example, it takes into account dispatch routes, stops (the pallets are placed in the lorry based on where they will be delivered first), goods stackability (especially with multi-SKU pallets, it’s essential for the goods to arrive damage-free) and location of the stock in the installation, among other factors.
- Control of the final goods exit stage: the WMS helps to verify that the products picked are correct. Immediately afterwards, they are ungrouped (if previously consolidated), packaged and deposited, waiting to be picked up by the carriers.
Warehouse shipping and receiving operations: manage them optimally for a healthy inventory
The control of warehouse inflows and outflows allows you to improve the visibility of goods movements taking place in the storage installation.
In carrying this out automatically with the help of a WMS, the system provides the warehouse manager with highly relevant information for decision making. These decisions not only affect the work being done in the installation, but also have an enormous impact on procurement tasks and inventory management.
If your warehouse is controlling goods entries and exits to and from the installation manually with paper or with programs such as Excel, feel free to request a demo of Easy WMS. An Mecalux specialist will show you the potential of this WMS for the automated management of warehouse shipping and receiving operations.