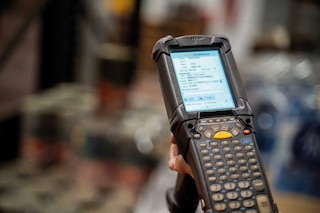
Inventory counting: doing it quickly and effectively
Inventory counting is a common practice carried out in the warehouse to accurately verify stock levels and locations. This is fundamental for planning procurement and logistics distribution tasks.
In our article, we’ll review the various options for conducting physical inventory counts in the warehouse and the tools and good practices that facilitate this.
What’s a physical inventory? What are its goals?
Inventory is the ordered, detailed and valued list of goods stored by a company. These materials are classified and assessed based on their characteristics in order to become part of the firm’s assets. Taking a physical inventory in an installation consists of contrasting stock, its quantities and its attributes with the data in the company’s records or IT system at a given moment.
The main objectives of conducting an inventory are to detect:
- Damaged or expired products.
- Obsolete stock: either due to modifications to the product itself or because it has been replaced by another. This type of stock needs to be closely monitored, as it directly impacts storage costs and occupies valuable space in the warehouse.
- Deviations due to human error and the system: the former are more common than the latter. The more organised daily operations are, the less imbalances there will be.
- Goods that have disappeared: this is known as shrinkage, generally produced by theft or other incidents.
In any event, when finishing the inventory, the warehouse manager has to issue a report highlighting:
- The variance percentage, by value and by unit, between the initial records and final inventory.
- The most significant differences found and possible causes identified following analysis of these imbalances.
- Actions proposed to improve stock management.
Main types of inventory
By taking as a basis the frequency with which goods counts are carried out, the following kinds of inventory stand out:
- Annual inventory:
An annual physical inventory count is usually required by the IRS for tax purposes.
This procedure is the most common type of inventory for companies that don’t have a large number of SKUs. However, with only one inventory per year, it’s difficult to perform analyses of imbalances and take measures to correct them in time.
- Periodic or cyclical inventory
The SKU and unit counts are carried out at certain time intervals (monthly, quarterly, etc.), which are defined by the companies. Generally, these counts are planned during times with less goods movement, since this avoids interference with normal warehouse activity.
- Real-time or perpetual inventory
Stock is controlled by a warehouse management system, whereby stock data are updated in real time. The system shows all goods movements without the need to stop operations. The implementation of a program is also advantageous for managing procurement, as it helps the purchasing department in terms of replenishing SKUs.
In addition, you can alternate inventory types with other exceptional recounts when you need to verify available stock in a specific area or location group.
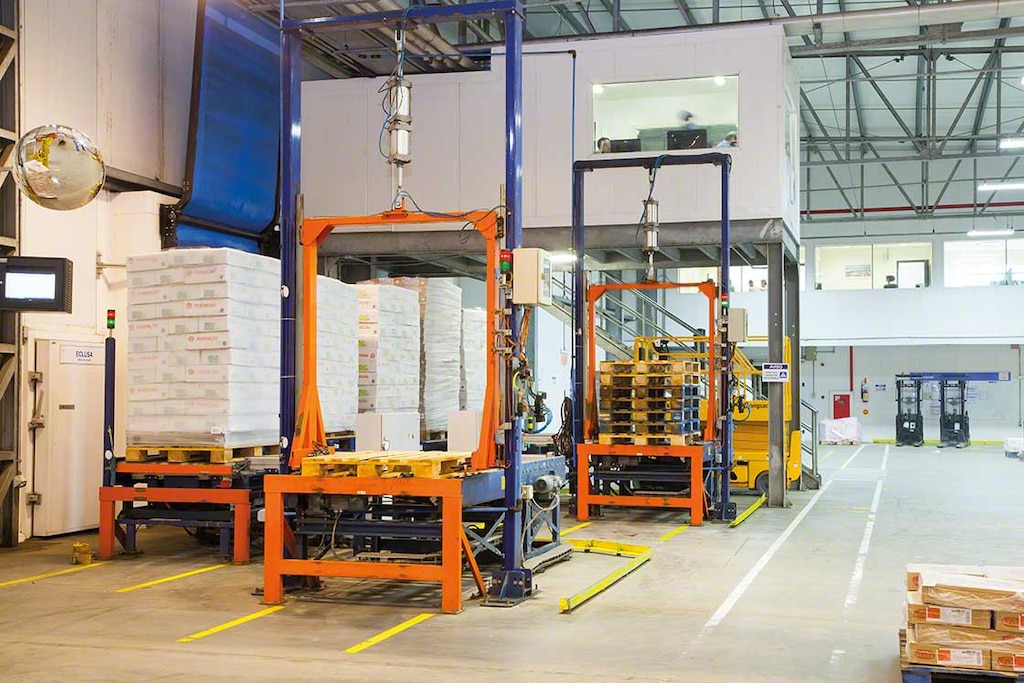
Taking a physical inventory: step by step
There are several essential actions you can carry out to perform a physical inventory in your warehouse, regardless of which technology you use:
1. Determine the methodology: this will depend on the type of goods stored. You need to decide which goods will be inventoried and how they’ll be quantified (by unit, volume, weight, economic value, etc.). When prioritising SKUs to be counted, one option is to apply the ABC method to sort them by turnover. They can also be organised by area or product family.
2. Train your team of operators: the team should know exactly what steps to follow, which section of the installation needs to be inventoried, how to use the tools, as well as any other instructions (for example, pulling obsolete or defective stock as it’s identified).
3. Take advantage of off-peak times: it’s important to take into account seasonality and to try to organise inventories during periods of less activity. This will limit their impact on the warehouse.
4. Notify suppliers: inventory paralyses stock inflows and outflows, so you need to plan it in advance and inform suppliers and customers.
5. Check your documentary tools and resources: this might seem like a less important issue, but the time spent conducting the inventory should be as limited as possible. Therefore, the necessary devices and documentation should be prepared in advance to prevent any last-minute issues.
Inventory: from Excel to warehouse management systems
Inventory results should be reflected in paper or computerised format, depending on the size of the company. Let’s go over the most popular options:
1. Inventory with Excel or on paper
Taking inventory on paper is the most basic version of this process. It’s only viable for businesses with minimal stock levels. Even in this case, though, counting goods without a warehouse management system exposes the company to problems that can be costly.
It works like this: operators check the stock against a list of products on paper, resulting in a very manual procedure that opens the door to human error.
An evolution of this method is the use of Excel inventory templates, which provide a bit of automation by making computerised calculations. With Excel, it’s also possible to install extensions that collect information directly from barcode readers, streamlining data dumping. Nevertheless, although it’s better than paper, this solution is error-prone as well. In the long term, as with paper, it doesn’t guarantee effectiveness or safety in stock control.
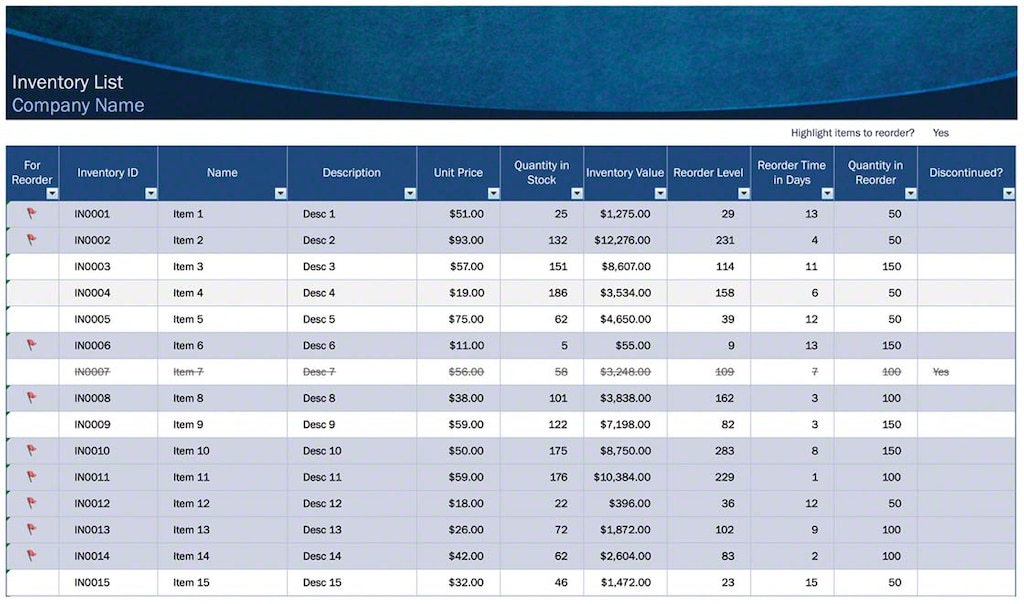
2. Inventory with a WMS
Warehouse management systems (WMSs) have accounted for a quality leap in terms of warehouse inventory accuracy and speed. In fact, they’re indispensable in businesses with a high number of SKUs. In these cases, inventory counting is extremely complex, and WMSs remarkably reduce the probability of errors.
Although it may sound surprising, according to data from the Warehousing Education and Research Council, two thirds of US warehouses still manage their stock by means other than a WMS, including by Excel. This is something that’s likely to change due to the functionalities offered by warehouse management systems.
For example, Easy WMS, the WMS by Mecalux, enables you to:
- Organise as many counts as the manager of the installation requires and with the necessary characteristics. For example, it’s possible to program counts of containers (pallets, boxes, etc.) or of specific items.
- Mark off the areas of the warehouse to be inventoried (counts by location).
- Establish rules of priority for products based on their logistics parameters (turnover level, unit cost, expiry date, batch number, etc.). This will let you select them easily and start the inventory according to those that are most important to the company.
- Integrate various sorts of scanning devices, such as radiofrequency terminals, voice-picking systems, and the like.
- Maintain maximum control of the warehouse by implementing a real-time inventory system. This will ensure that information on available stock is updated on a daily basis. In the case of Easy WMS, the Supply Chain Analytics Software module is charged with managing this huge amount of data.
Inventory with barcodes or RFID tags?
One element that largely influences how an inventory is carried out is the identification system used. This can range from traditional barcode scanners to sophisticated RFID tags. Let’s analyse these two options:
- Inventory with barcode readers or radiofrequency devices
The barcode identification system is the most widespread one due to its effectiveness, universality and low implementation cost. The transfer of information between the physical and digital worlds, whether via Excel or more advanced software, is made by using devices that scan product barcodes. This requires a direct line of sight between the reader and the goods.
Radiofrequency terminals are also barcode readers, with the added capacity to communicate with the warehouse management system through radiofrequency waves. Thus, operators can receive orders and run checks directly via the terminal, streamlining tasks.
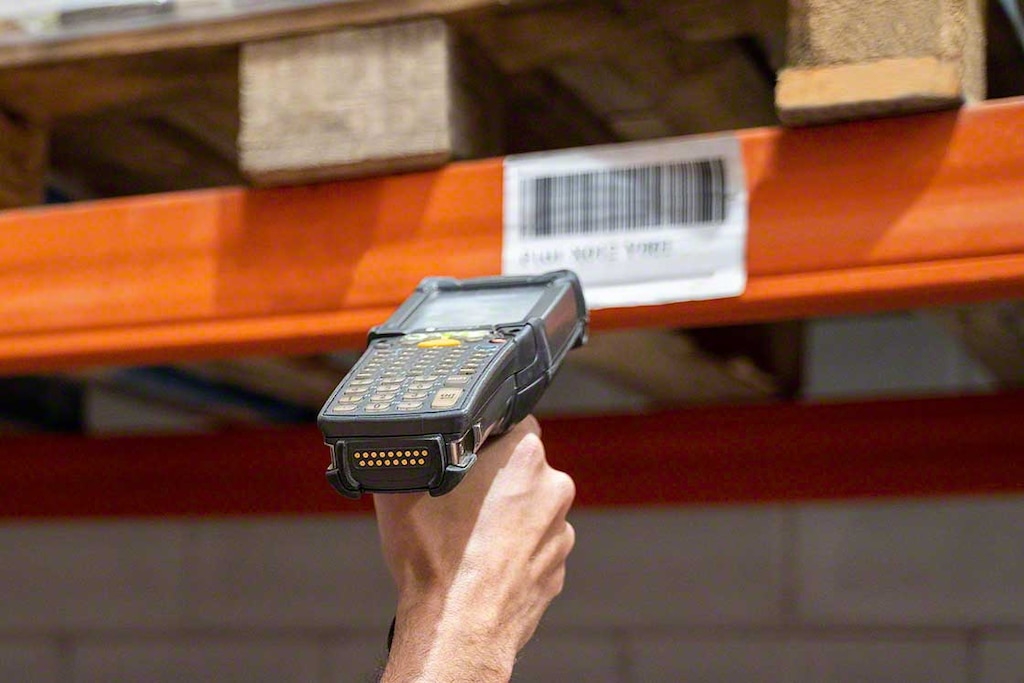
- Inventory with RFID readers:
The implementation of an identification system using RFID (radiofrequency identification) tags has constituted an enormous advance for fast stock counts.
This technology uses radio waves to send and receive data linked to an object. Comprised of chips integrated into a sticker, these tags store a greater amount of information, which can be modified throughout the product’s journey along the supply chain.
In terms of inventory tasks, one of the main advantages is that these labels don’t require a direct line of sight between the tag and the reader. So, by simply moving the reader past the container, the data are uploaded directly into the system.
Two major barriers that have hindered mass implementation of the RFID system are, on the one hand, its cost, and, on the other, its lack of precision. Nevertheless, the market has evolved; in 2018, the average cost of IoT sensors such as RFID tags was 200% less than that of 2004, according to Microsoft’s Manufacturing Trends Report.
What’s more, there have been numerous successful case studies that show that technology has clearly improved in the accuracy of readings. A study done by the organsation GS1 US and the RFID Lab at Auburn University revealed that 70% of orders analysed contained some kind of error when identified using barcodes, while that figure stood at only 0.01% for orders processed with RFID tags.
Inventory counting: the importance of doing it well
The objective of proper inventory control is to maximise profits while minimising storage costs. Simultaneously, you want to make sure that this doesn’t affect your installation’s service levels and that you improve customer satisfaction.
Technology such as warehouse management systems and RFID are contributing towards making the entire process more accurate. However, there is still some way to go, as many companies still rely on more manual methods of taking inventory in the warehouse.