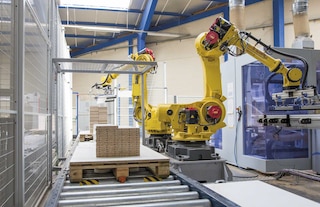
Industry 4.0: the Fourth Industrial Revolution
Industry 4.0, or the Fourth Industrial Revolution, uses digitalisation and hyperconnectivity as a springboard to transform organisational structure. In fact, 86% of company heads hope to reduce costs and increase profits through their investment in Industry 4.0, according to a study by PwC.
In our article, we’ll set out the main characteristics of the so-called smart or connected industry, the technologies contributing to this transformation of the sector and the way in which this is affecting logistics organisation and the reality of the supply chain.
What is Industry 4.0?
Industry 4.0 is characterised by the total integration of all information between the physical and digital worlds in the context of production processes. The huge amount of data collected by interconnected, increasingly smarter technology is at the core of the Fourth Industrial Revolution.
To understand the origin of Industry 4.0, let’s run through the previous revolutions:
- The First Industrial Revolution (also known simply as the Industrial Revolution), began in England at the end of the 18th century. It arose from the invention of the steam engine and the mechanisation of the textile industry.
- The Second Industrial Revolution started at the end of the 19th century and was characterised by the mass-production of goods.
- In the mid-20th century, the first computers ushered in the Third Industrial Revolution, marked by the use of IT in industry and the improvement of ICT (Information and Communications Technology).
Industry 4.0 involves going a step further: it’s revolutionising not only methods for manufacturing products, but also goods distribution, storage and the way in which customers relate to businesses.
Challenges of Industry 4.0 for companies
In their conversion to Industry 4.0, organisations are facing new challenges related to:
- The rise in overall competitiveness:
Businesses need to be able to adjust their production processes to rapidly changing demand and, at the same time, maximise their productivity. To do so, it’s essential to implement technological advances swiftly. The Digital Factories 2020 report by PwC states that 98% of company directors surveyed agree that the search for efficiency in production is the main reason for digitalising factories.
- The necessary digital transformation of industry:
The investment in R&D and innovation in logistics processes has become essential for the long-term economic growth of many firms. In many cases, it’s the key to their survival. Innovation in the Industry 4.0 environment translates into:
- The creation of new products for a digitised society.
- The adoption of advanced, smart production systems (smart factories).
- The proper management of a complex, globalised supply chain.
- Training and management of human capital:
Industry 4.0 is creating a demand for workers with new abilities, or what’s known as Talent 4.0. This will provide businesses with the knowledge needed to implement technological solutions in their processes.
- New digital risks: cybersecurity in Industry 4.0
The main challenge for cybersecurity implementations in Industry 4.0 is the rapidly evolving nature of computer attacks. Data and identity theft, computer system crashes…the threats are very diverse and can become critical in the connected Industry 4.0 scenario.
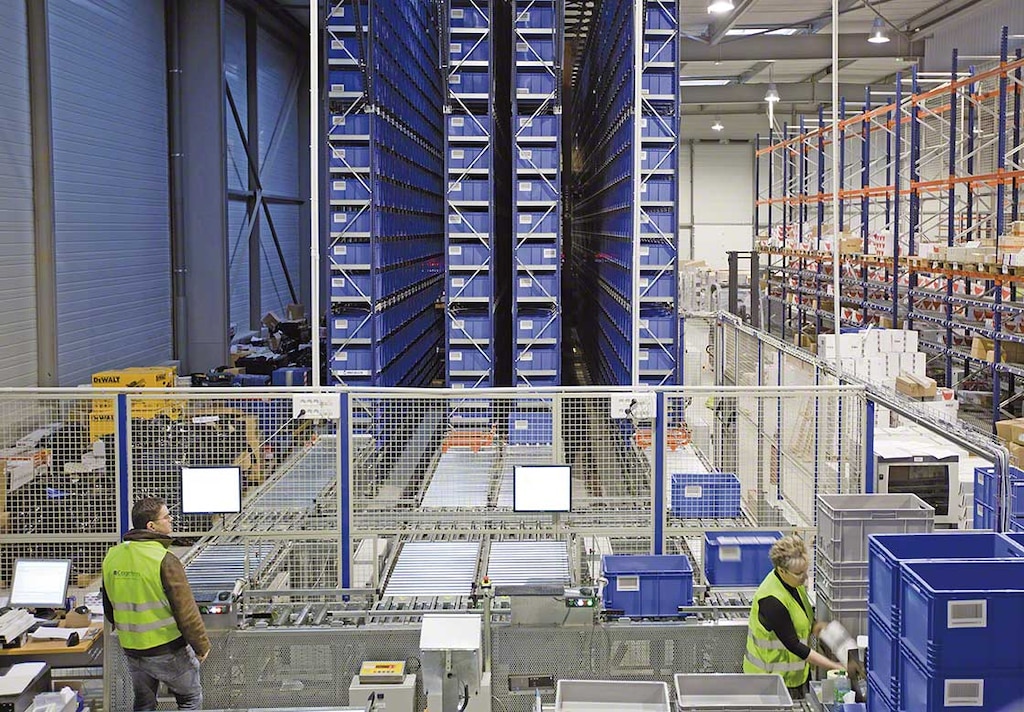
Technology 4.0, serving a connected industry
The expansion of the Fourth Industrial Revolution can’t be fully understood without mentioning the main technologies behind it:
- Internet of Things, or IoT : industrial machinery now has the ability to communicate and share information collected through multiple sensors in real time. This makes it possible to carry out a more in-depth analysis of the entire system and respond immediately to any contingency event.
- Big data, artificial intelligence (AI) and machine learning: these three disciplines are closely related to the collection and management of an enormous amount of data from different sources (big data). Thanks to machine learning, AI enables computers to learn and improve processes on their own, based on historical data and the repetition of operations.
- Augmented reality: this allows us to add layers of virtual information to real environments. Via electronic devices, such as glasses or screens, users access a mixed reality in which real and digital elements are combined.
- Digital twins: this technology takes data from the physical world and replicates it in a virtual scenario. With this process, we can analyse a problem or check the functioning of a system digitally, then apply the solution to the real world.
- Blockchain: this consists of a new way of structuring data transmission, distributed in encrypted blocks linked together and identified with unique and unrepeatable numbers. Based on complex mathematical algorithms, this technology ensures the complete security of the information, as it is able to detect and reject any unauthorised changes.
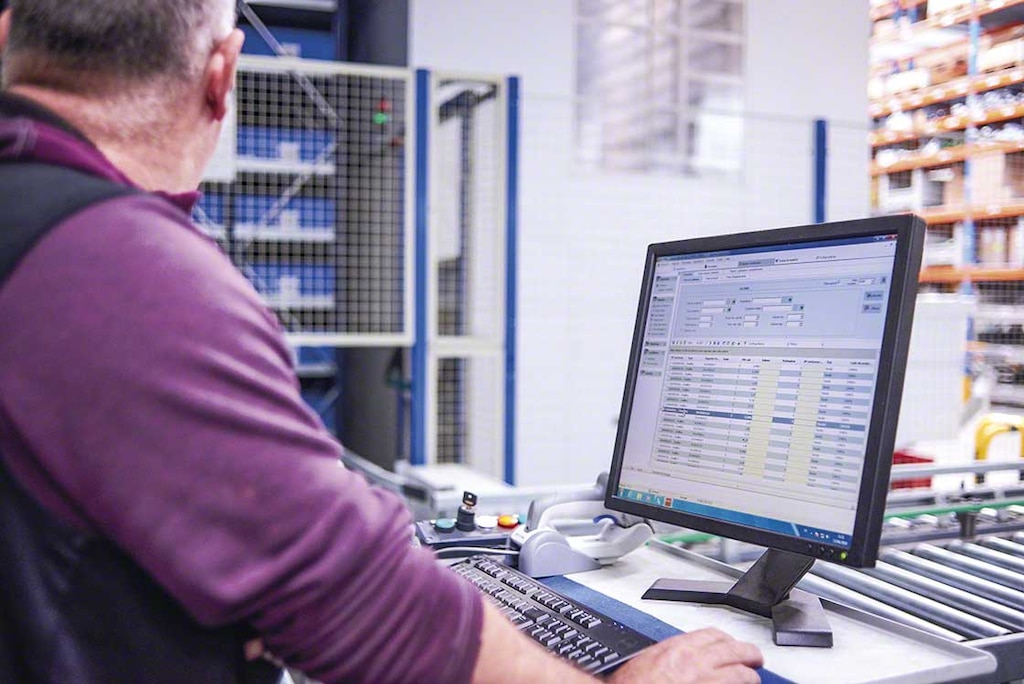
Supply Chain 4.0: smarter logistics
Like industry, logistics is up against a demanding and volatile market. Against this backdrop, the supply chain has to implement the latest technology in all its processes to create a more streamlined and efficient logistics network:
1. Cloud computing in warehouse management
The need to interconnect more and more systems and links in the supply chain makes software in the cloud or SaaS (software as a service) an almost indispensable element in establishing the Industry 4.0 model. According to forecasts from consulting firm Gartner, the cloud applications market is expected to continue registering double-digit growth in the coming years. What’s more, in 2020, the sector is slated to increase its revenue by 17%, reaching 266.4 billion dollars worldwide.
Compared to the traditional on-premise system, whereby the company’s own servers were installed in its facility, cloud computing facilitates access to information from anywhere. It also enables integration with other applications, such as the running of automatic updates that strengthen cybersecurity.
Warehouse management systems (such as Easy WMS) are a clear example of logistics software that can be used in both the cloud and on-premise modalities.
2. Technology for the traceability and automatic identification of goods
Having precise control over logistics traceability data is crucial, as it allows you to know the location and condition of the product at all times.
In this vein, one of the most well-known IoT device applications in logistics is automatic identification via RFID (radiofrequency identification). Inside the warehouse, this system improves the accuracy and speed of making inventories of parts and products. Outside the installation, in the transportation and distribution stage, it helps to reduce phenomena such as the bullwhip effect.
3. Warehouse automation
One of the objectives of internal logistics is to optimise material and personnel flows in a firm’s installations. The design of systems capable of speeding up these movements has made warehouse automation the main growth engine of the global service robot market, according to data from the International Federation of Robotics (IFR).
Automated warehouses are equipped with systems that facilitate the loading and unloading of goods, as well as the movement of products and their slotting in the racks. This is the case, for example, of stacker cranes for pallets, stacker cranes for boxes and conveyors that connect the various areas of the installation.
Fourth Industrial Revolution: logistics success stories
The warehouse is one of the logistics elements with the most interaction with other business areas. As such, its automation has a considerable impact on operations management. The following are two examples of Industry 4.0 in logistics:
- Installation of distribution company Cogeferm: a zoned layout based on ABC analysis, a miniload warehouse, conveyors for boxes for the preparation of small orders and smart management with Mecalux’s Easy WMS are the components that have made up an Industry 4.0 facility for this French distributor of hardware products.
- Warehouse of manufacturer Dafsa: this clad-rack warehouse is equipped with an extensive network of conveyors. In combination with AGVs, they move pallets from the production centre, depositing them in the area designated by the WMS (by means of transfer cars and stacker cranes) or bringing them to the dispatch zone. This installation is fully integrated with the rest of the systems operated by the factory. In addition, it’s been designed for possible future expansion.
Future expectations for Logistics and Industry 4.0
Flexible production, increased integration between the various business areas, and the digital transformation of production centres have become the basis for Industry 4.0. Nevertheless, the connected industry can only work when all the gears are in sync, controlling flows of materials and of information linked to each product.
By combining sensors, connectivity and greater data processing power, rapid technological evolution is increasingly bringing to the table solutions aimed at building the logistics model required by smart industry. These solutions will undoubtedly respond to challenges such as warehouse complexity, the 24-hour delivery standard and omnichannel retail.