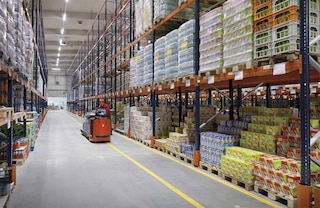
Cycle counting: how to implement it in the warehouse
Cycle counting is an inventory technique commonly used in small and medium-sized installations. But what exactly does it mean? This method consists of periodically counting groups of SKUs instead of conducting a one-time annual inventory.
These sets of SKUs are determined according to a particular criterion, for instance, their turnover rate (A, B, or C), size, SKU type, etc. The number of times a product is counted throughout the year is known as count frequency.
The advantages of inventory cycle counting over annual or semi-annual audits are that cycle counts reduce the risk of stockouts, ensure better knowledge of the SKUs in stock, and, above all, make it easier to detect errors and imbalances between the ERP and WMS systems and the stock actually in the warehouse.
Types of cycle counting
There are three inventory cycle count methods, based on the criteria applied when determining the groups to be counted:
- ABC cycle counting: this is the most common technique in installations. It’s based on the Pareto principle, by which 20% of the SKUs account for 80% of the sales. With this in mind, the logistics manager should assign a turnover — A, B, or C — to each SKU according to its sales frequency (A is the category with the highest turnover, while C is the lowest). With inventory cycle counting, A items are counted more frequently than C products.
- Control group cycle counting: this is usually employed the first time a company implements cycle counting. Logistics managers choose a series of SKUs to be inventoried various times in a short period. The objective of this method is to pinpoint stock-counting errors and streamline the inventory process.
- Random sample cycle counting: when the SKUs have similar characteristics — turnover, size, weight, value, etc. — random sample cycle counts are done. That is, since there are no distinguishing features that differentiate the various SKUs, groups of products are created randomly.
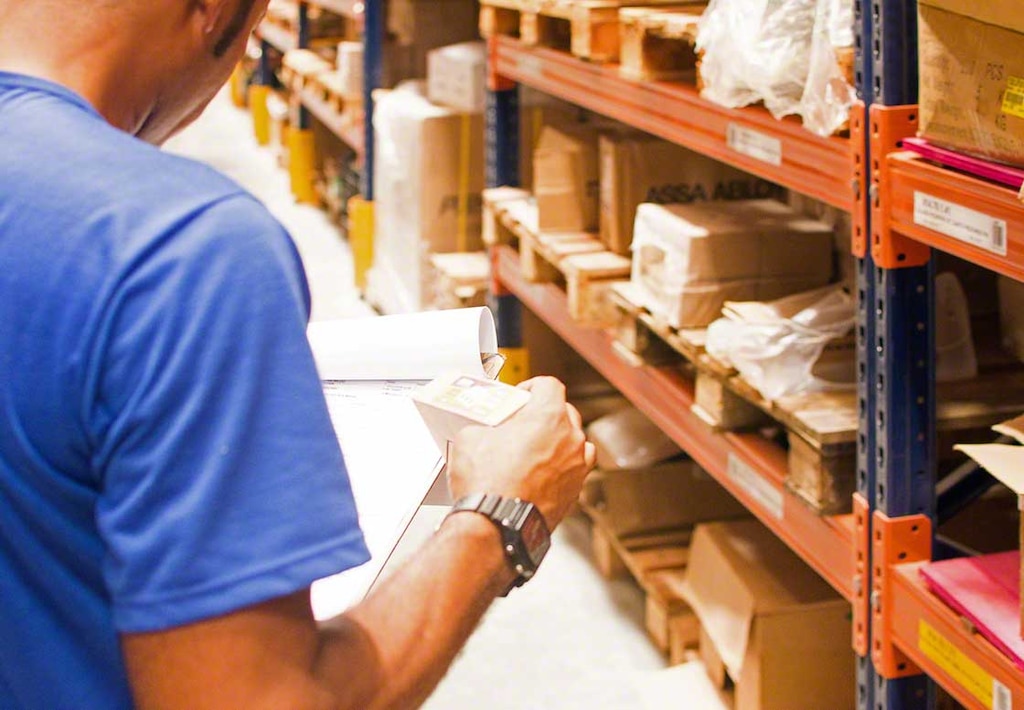
Pros and cons of cycle counting
Inventory cycle counts allow you to:
- Have more accurate stock records; this improvement is easily measurable through Inventory Record Accuracy (IRA).
- Efficiently organise item counting, reducing the work that a single yearly inventory entails.
- Streamline the detection and removal of defective or damaged products.
- Maintain productivity while counting stock, without interrupting other warehouse operations in the process.
- Make better logistics decisions in procurement, storage and order prep.
Generally speaking, inventory cycle counting enables improved control over SKUs in the warehouse, preventing situations as detrimental to the company as stockouts or, alternatively, overstock.
Cycle counts vs. periodic inventory
As we’ve seen above, cycle counts have become established as a viable alternative to annual inventories done in installations.
Periodic inventory, meanwhile, lies somewhere in between the cycle counting and annual methods. As its name indicates, this audit takes place periodically, various times a year. However, it is not conducted by groups of SKUs, as with cycle counting; instead, it is done throughout the whole warehouse.
Logistics planning establishes the point during the year at which operators will stop performing their duties to dedicate themselves to the periodic inventory.
Below are the main differences between both techniques:
Cycle counting | Periodic inventory |
---|---|
SKUs are audited in cycles and by group. | A record of all warehouse assets is made in line with the logistics planning (semi-annually/annually). |
The process is routine and can even be done daily. | The process is carried out at specific times of the year. |
It isn’t necessary to halt logistics operations. | Operators must stop doing their usual tasks to work on the inventory. |
The method detects errors quickly. | The method detects errors accumulated over time. |
It increases the accuracy of warehouse records. | Its aim is to comply with tax obligations or red tape. |
In short, inventory cycle counts have succeeded in implementing the continuous improvement methodology in stock management in the warehouse: they’ve lightened the burden of periodic stock audits and boosted efficiency in asset management in logistics facilities.
Example of how to implement cycle counting
Let’s take a look at how to implement cycle counting in a business in which SKUs are organised and slotted by value and sale frequency.
Suppose it’s an automotive company with a production and distribution centre with mechanical car parts. The logistics manager’s first step is to analyse, as per the Pareto principle, the turnover of each SKU (A, B, or C). Following this, the manager can affirm that engines account for almost 80% of the profits (A), sales of brakes represent 15% (B) and gearboxes constitute 5% (C).
Taking into account the SKU locations and the frequency of the count established to avoid stock management errors, this company’s ABC cycle count model should look like this:
SKU | No. locations | Count frequency | Counts per month | Workdays/month | Counts/day |
---|---|---|---|---|---|
A | 600 | Monthly | 600 | 22 | 27 |
B | 240 | Weekly | 40 | 22 | 2 |
C | 240 | Annually | 20 | 22 | 1 |
A + B + C | 1080 | 22 | 30 |
Accordingly, the logistics manager of the automotive company should do 30 counts a day to reduce the number of inventory-related errors. Otherwise, not applying this stock management technique means the firm would have to review its more than 1,000 locations once a year, resulting in the shutdown of the logistics operations in its installations.
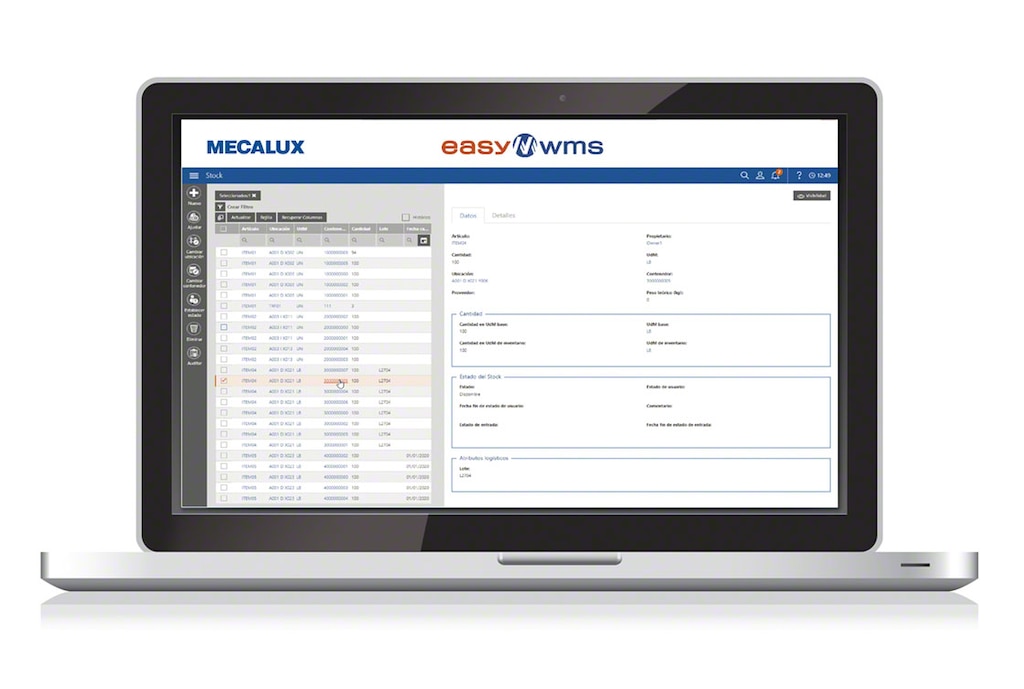
Comprehensive stock control: the need for a WMS
Cycle counting is an inventory technique aimed at improving stock records in the warehouse. However, in cases such as the example above — in which inventory is complex because of the number of slots — it’s advisable to implement a warehouse management system (WMS). This type of software provides you with full control over your inventory in real time, automating stock organisation techniques such as cycle counting. For example, Easy WMS by Mecalux is able to organise cycle counts, improving the precision and accuracy of the inventory in the installation.
To find out about all the benefits the deployment of a WMS can bring to your company, don’t hesitate to contact Mecalux. An Easy WMS expert consultant will listen to you and offer you the best technology solution tailored to your needs.