Advantages of automated storage and retrieval systems
Automated storage and retrieval systems (AS/RS) are logistics solutions in which the vast majority of movements and operations are carried out automatically, with the help of handling equipment such as stacker cranes, conveyors, and electrified monorails.
We live in a globalized world in which Logistics 4.0 reigns supreme and businesses need to cut costs and streamline operations to be more competitive. Many companies consider the possibility of automating processes to lower the risk of error and raise productivity.
In this post, we’ll examine the advantages of automated storage and retrieval systems and what organizations should take into account when taking that step and incorporating automatic handling equipment to boost their supply chains.
Advantages of automated storage and retrieval systems
AS/RS are solutions that make it possible to manage, optimize, and speed up the storage, preparation, and dispatch processes for all kinds of products. Therefore, many companies resort to automated storage and retrieval systems to benefit from:
- Productivity and high availability. AS/RS ensure continuous, uninterrupted inflows and outflows of goods. The handling equipment is available 24/7.
- Economized labor cost. The equipment is charged with handling the goods automatically, so, forklift operators, order pickers, and administrative staff can devote their time to other more value-adding tasks.
- Lower maintenance costs. The automated handling of the goods reduces impacts and wear and tear on the handling equipment due to improper use.
- Employee safety. Automated storage and retrieval systems are designed to minimize the presence of humans. As a result, the operators are better protected, and their workstations are much more ergonomic.
- Goods security. The inaccessibility of the load helps to keep it in perfect condition: the goods aren’t lost or broken, nor do they spoil.
- Real-time inventory. Every automated storage and retrieval system has a warehouse management system (WMS) that identifies and controls the stock in real time. With the movement history, logistics managers can rigorously control product traceability.
- Space maximization. These solutions optimize the available surface area to provide the greatest possible storage capacity. AS/RS are flexible and adapt to the particular features of each building. At the same time, they’re scalable and can be added on to if need be.
Before implementing an automated storage and retrieval system, and reaping all these benefits, it’s essential to obtain the advice of a specialist. This expert should analyze the needs of your business and the limitations and specificities of your facility with the aim of finding the best solution for each case. Our company has extensive experience automating warehouses all over the world.
Data to consider before devising an AS/RS
Prior to implementing an automated storage and retrieval system, the first thing you need to do is identify your company’s objectives: What are its needs? What is it looking to improve? What are its prospects for future growth?
A business can automate an already existing warehouse, replacing traditional storage systems with automated ones (in which stacker cranes and conveyors manage the goods as opposed to operators). Alternatively, a new automated facility can be built from the ground up.
The difference between the two options lies in that, when designing a new automated warehouse, you have the possibility of making it a clad-rack warehouses. This solution leverages all the available space to provide increased storage capacity. By automating an existing facility, the company is conditioned by the space it has, the warehouse layout, and the organization of the operations.
Whichever option you decide on, first and foremost, you need to analyze several indicators regarding your company’s business activity:
Goods
These are a firm’s main asset, so they should be analyzed in depth:
- Unit loads used (pallets or boxes).
- Goods sizes and weight.
- Quantity of products stored.
- Number of SKUs to be stored and their particular attributes.
- Characteristics of the goods (strength, sensitivity to fire or humidity, etc.).
- Demand level and turnover.
With these data, you can decide which storage system is ideal and define the dimensions of the locations. Likewise, the logistics manager can also get an idea as to how the operations will be carried out and which types of working areas should be set up.
Space
When the automated storage and retrieval system is planned for a previously existing facility, it’s necessary to thoroughly examine several of its particularities:
- Building shape and dimensions.
- Characteristics and constraints relating to access, flooring, windows, pillars, etc.
- Floor strength.
- Local construction regulations.
- Obligation to carry out seismic calculations.
With this information, the storage system provider can design the racks with the appropriate strength and, above all, make sure every available inch of space is maximized to achieve the highest storage capacity possible.
Equipment in use
If your facility already has racks and handling equipment, it’s important to keep in mind:
- Rack sizes, quantity, and load capacity.
- Characteristics of the handling equipment employed, such as maximum lift height and load capacity.
- Willingness to purchase new equipment for the warehouse.
These data will determine whether it’s necessary to install new equipment and indicate possible limitations. At the same time, they serve to analyze the possibility of expanding the storage capacity.
Flows and turnover
These factors take into account the facility’s size and layout, as well as the way in which the different operations are currently carried out:
- Product entries (frequency and volume).
- Goods handling.
- Order preparation (quantity and number of lines for each one).
- Product exits (method for sorting orders, frequency, and quantity).
With all these data and their subsequent analysis, you’ll be able to come up with the most suitable solution: an automated or non-automated solution. Companies with high inflows and outflows, for example, usually turn to automation because of the enormous agility offered by the stacker cranes and conveyors. On the other hand, businesses with a slower pace of work tend to go with manual solutions.
There’s no set rule for determining which storage system will best meet a business’s needs. The optimal solution is the one that fulfills the requirements and constraints of each specific case.
Automated storage and retrieval systems
Studying the specificities of the various storage systems is a good starting point for making your decision. First, let’s divide the AS/RS into two general categories: those with direct access (goods can be directly accessed from the aisles) and those offering compact storage (the products are not as easily accessible, but the warehouse space is better leveraged). We should note that these two types aren’t mutually exclusive — they can coexist under the same roof.
Systems with direct access
A traditional warehouse can be automated relatively easily by means of a configuration consisting of single- and double-deep conventional pallet racks served by Automatic trilateral stacker cranes. One of the particular features of this type of handling equipment is its ability to be adapted to any warehouse that’s already managed with narrow aisle forklifts driven by operators. Thus, this system is easily implemented in preexisting facilities, as the structure doesn’t need to be modified. One last plus point to underline is that your investment will pay off quickly.
If, on the other hand, you have the chance to build a new automated facility from scratch, the most common solution for this case would be stacker cranes for pallets (as opposed to trilateral stacker cranes). These stacker cranes for pallets can be installed in taller buildings (Mecalux’s MT-5 model can reach up to 45 m), providing for greater storage capacity.
Compact systems
These high-density systems comprise racking units that make the most of the surface area to provide the highest possible storage capacity, with the trade-off that part of the goods can’t be directly accessed from the storage aisle. Compact storage systems typical of traditional warehouses include: drive-in/drive-thru pallet racks, live pallet racking, push-back racks, and the Pallet Shuttle system.
In automated warehouses, only pallet flow racks and the Pallet Shuttle system can be fully automated. In both cases, it would be necessary to incorporate a stacker crane tasked with handling the goods and inserting and retrieving the pallets to and from their corresponding locations. In the event you choose the Pallet Shuttle configuration, the automated Pallet Shuttle model will be used, which doesn’t require operator intervention to work.
A high-density AS/RS system leverages space much better, as it provides a greater storage capacity compared to single- or double-deep racks while expediting operations. However, as with all compact systems, these type of solutions are only viable in facilities without an excessive variety of SKUs.
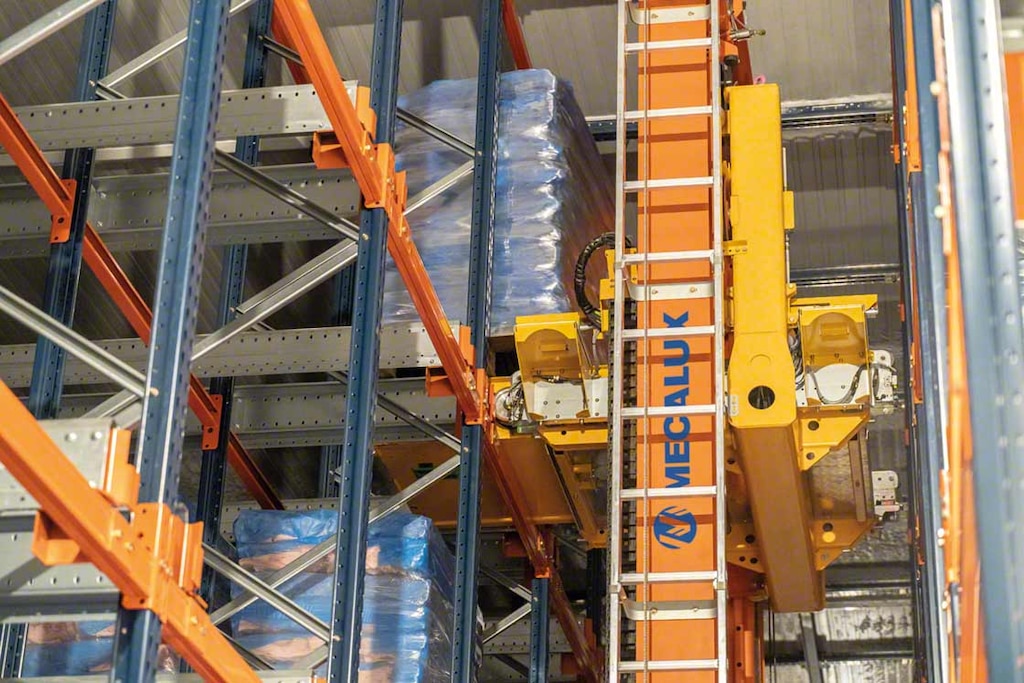
On the road to an automated warehouse
If you’re thinking of automating your facility, we recommend you seek advice from experts who can guide and propose the right solution for your needs.
At Mecalux, we have considerable expertise in automating warehouses for companies from all varieties of sectors. For example, electromagnetic component manufacturer SMA Magnetics asked our firm to automate its facility in Zabierzów, Poland, with trilateral stacker cranes that insert and extract pallets from their slots.
Other companies have turned to us to implement their new automated storage and retrieval systems that will help to bolster their growth. This was the case of Brazilian logistics business Iceport. This firm needed to strengthen its position in the Latin American market and boost the growth it had experienced in recent years, so it decided to erect a large-capacity freezer warehouse. Our company built it an automated self-supported facility that operated at a constant temperature of -28 °C.
When designing an automated storage and retrieval system, some decisive factors to be considered are the size of your facility, the number of pallets to be handled, the work shifts, and, ultimately, your particular needs. Don’t give it a second thought — get in touch. We’ll come up with the best solution for you.