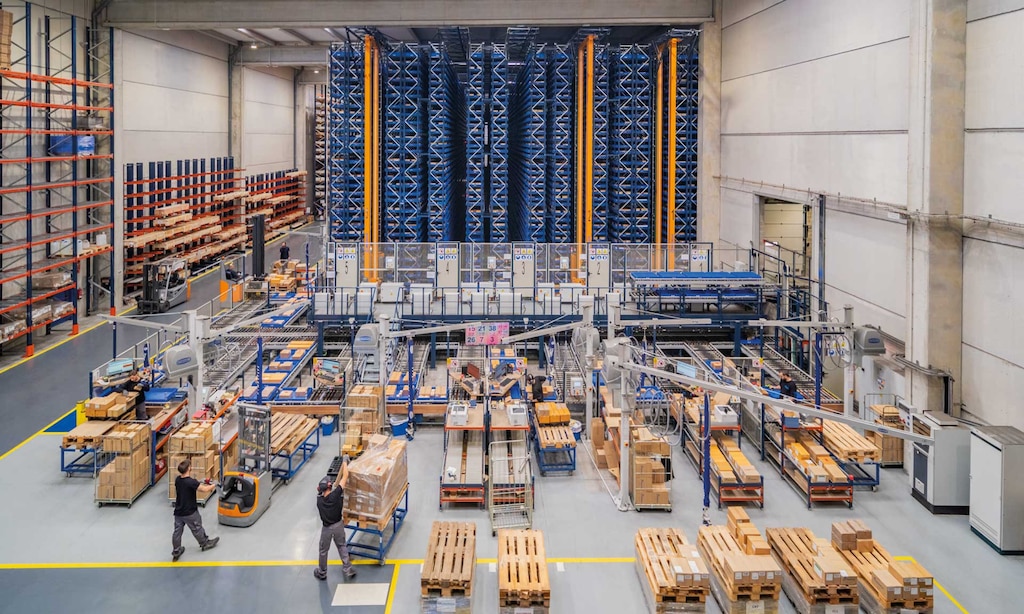
LOGISTICS RESEARCH
By Diego Pacheco, Daniel Møller Clausen and Jendrik Bumann
Warehouses are a key element in the supply chain and the end-customer experience. However, the managers of these facilities face ongoing challenges that they must respond to in their daily operations. Some of the most critical are inadequate quality controls, redundant processes, poorly designed layouts and inaccurate inventory information. If not addressed, these issues can lead to additional costs, decreased performance and, ultimately, dissatisfied customers.
In the Toyota Production System, non-value-adding activities are called muda, the Japanese term for waste. The seven types of waste include waiting times, overproduction, unnecessary motion, transport, inappropriate processing, defects and overstock.
Being aware of the current state of the warehouse is an essential step in identifying the wastes present in it. This is done through data analysis, facility observations, interviews and/or questionnaires, Pareto analysis of the products, and Lean tools such as value-stream mapping (VSM) and Genba Shikumi, a quantitative technique based on successive correlation vectors and matrices, among other methods. To achieve high-performance operations and remain competitive, it is necessary to implement continuous improvement programmes.
Finding bottlenecks in a distribution warehouse
In this study, we examined the operations of a Danish distribution facility belonging to a small to medium-sized enterprise (SME). The warehouse has a full-time manager and a part-time assistant. The company sells products across Europe under both the B2B and B2C models. The study investigated the strategies for identifying and reducing operational wastes and then applied the findings to this business.
During the initial interactions, our research team found that the top managers were aware of various operational problems affecting the SME’s performance. If the company failed to respond to the situation proactively, these difficulties could eventually hinder its potential scalability in the market.
Data collection for analysis took place in several phases. First, an interview was conducted with the business owner to understand the organisation, its staff and the issues facing the warehouse. The project group subsequently made three visits to the company for additional data acquisition. Additionally, a questionnaire was distributed to collect supplier and shipment information. Sales and inventory reports were also used to determine the profit of product families.
Detection of inadequate processes
We observed that when there was no precipitation, goods could be offloaded and sorted outdoors, where there was more space for the activity. In the packing and shipping process, the most influential factor was the availability of appropriate boxes and filling materials. When a truck arrived, there was no system for assigning the goods to a storage location. Furthermore, when fulfilling orders, merchandise could sometimes not be found. In these cases, the picker would search for the item, ask a co-worker for help or fulfil the order without the product in question. If suitable packaging was unavailable, the operator had to find an adequate box in another part of the warehouse.
On average, the business distributes 128 products daily in a single shipment. It receives 367 packages containing 9,175 items every two months from its leading supplier. Although they exchange data electronically, the information flow within the SME is still manual.
Without a system for allocating SKUs, all knowledge rests with the warehouse manager, making the business vulnerable if this employee leaves or is unavailable for extended periods
With just one full-time employee, office workers have to help with offloading. If the operation lasts more than an hour, the business must pay the delivery company an extra fee. Without the correct equipment, this process is physically tiring. Moreover, as goods are placed onto the truck randomly, workers sort products by category during unloading, which is quite time-consuming.
Without a system for allocating SKUs, all knowledge rests with the warehouse manager, making the business vulnerable if this employee leaves or is unavailable for extended periods. The lack of inventory information and limited training cause operators to ask many questions, taking time away from the manager and office employees.
The picking process starts when a warehouse employee takes a printed order from the batch. The order then functions as a pick list, which the worker places on a tray. It was found that accidentally placing a new order at the top of the tray instead of the bottom resulted in delays of previous orders. Furthermore, the labels on several boxes are small and unclear, making them difficult to read. Boxes are stacked on top of each other, complicating picking. Without a warehouse management system, workers rely on their memory to find the fastest routes, posing additional challenges for seasonal workers.
Results and value-stream mapping
The findings showed that most warehouse processes could be improved. Although the organisation was growing, it had not changed its way of working, leading to multiple problems, including double handling. Meanwhile, operators received no feedback on their work via customer satisfaction ratings or a visual display of errors made.
The study found that the three types of waste primarily affecting this Danish company were process wait times, unnecessary motion and transport. Together with overall facility operations, offloading and sorting were the areas requiring urgent attention. Based on the findings, several changes were proposed to enhance warehouse performance. These are detailed in the future VSM.
Implementing a warehouse management system (WMS) was the most significant change proposed in the future VSM. This software improves the entire value stream and contains master data for all SKUs. It provides information on supplier shipments in advance, allowing workers to prepare to receive new SKUs effectively. A WMS ensures the availability of sufficient space in a facility by assigning all products a location before they arrive. In this scenario, the software is also connected to a voice-picking system. Moreover, by reading advanced shipping notices (ASNs), the WMS issues alerts for the offloading and sorting processes.
Another conclusion was the need to establish standard operating procedures (SOPs) for the supplier, the offloading and sorting process and packaging. These SOPs include requirements for label size and visibility and for structuring SKUs prior to shipment.
Leveraging a WMS
A WMS would positively impact all warehouse operations, whether installed as a standalone solution or integrated with an enterprise resource planning (ERP) system. Implementing a WMS can reduce lead times, excessive goods handling and unnecessary travel. Likewise, sales forecasting results in more accurate inventory levels, thus avoiding waste.
WMSs can solve slotting issues and put away new SKUs according to ABC analysis. This ensures that the heaviest merchandise is stored near the pick stations and places products often sold together near each other. It can also serve as a planning tool, determining whether there are enough boxes of different sizes available for packaging.
Warehouse performance affects multiple areas, and streamlining processes benefits organisations overall
Studying and understanding the origin of operational waste enables employees to realise the importance of their work, increasing job satisfaction. The research demonstrates that applying waste reduction techniques leads to better resource allocation, fostering business growth and new commercial opportunities.
Warehouse performance affects multiple areas, and streamlining processes benefits organisations overall. In the case of the Danish distribution company, the current VSM revealed an overall production time of 1,721.29 hours. Implementing a WMS and making improvements across all operations would reduce that figure by 41.4%.
AUTHORS OF THE RESEARCH:
Diego Pacheco, Daniel Møller Clausen and Jendrik Bumann. Department of Business Development and Technology, School of Business and Social Sciences, Aarhus University (Denmark).
Original publication:
De Jesús Pacheco, Diego Augusto, Daniel Møller Clausen and Jendrik Bumann. 2023. “A Multi-Method Approach for Reducing Operational Wastes in Distribution Warehouses”. International Journal of Production Economics 256 (Elsevier).
© The Authors. Licensed under CC BY 4.0