
Supply chain diagnostic: improving processes
Are your logistics systems effective and productive enough? Before answering, you need to carry out a supply chain diagnostic, that is, an analysis of the performance of your logistics processes. The goal is to define actions that can enhance your company’s results.
Logistics fulfils the function of delivering orders to customers at the right time and as per the agreed-upon terms. To achieve this, it’s essential for operations in your supply chain to be well organised. At the same time, you have to decide what goods you need and in what quantities to, thus, be able to provide the desired service.
Carrying out a supply chain diagnostic is a starting point for many businesses looking to raise productivity in their installations. In this post, we’ll demonstrate that making improvements resulting from a supply chain diagnostic reduces costs, helps to provide more efficient service, and, in turn, enhances the organisation’s corporate image.
Why conduct a supply chain diagnostic?
A supply chain diagnostic is an analysis of the different processes that take place in and outside of the warehouse. It assesses throughput as well as the status and particulars of operations such as storage, procurement and picking.
Many companies aspiring to be more competitive find themselves facing difficulties and inefficiencies: they have overstock issues, a slow return on investment, low productivity, long response times and/or excessive logistics costs. These problems are the result of shortcomings in terms of the management systems used and the lack of foresight and planning when addressing market needs. The good news: these complications can be detected and resolved by means of a supply chain diagnostic.
This study can be undertaken by a supply chain consultant, such as a supplier of storage solutions and warehouse management systems (as in the case of Mecalux). This evaluation can also be made by 4PL and 5PL logistics providers, which also offer consulting services.
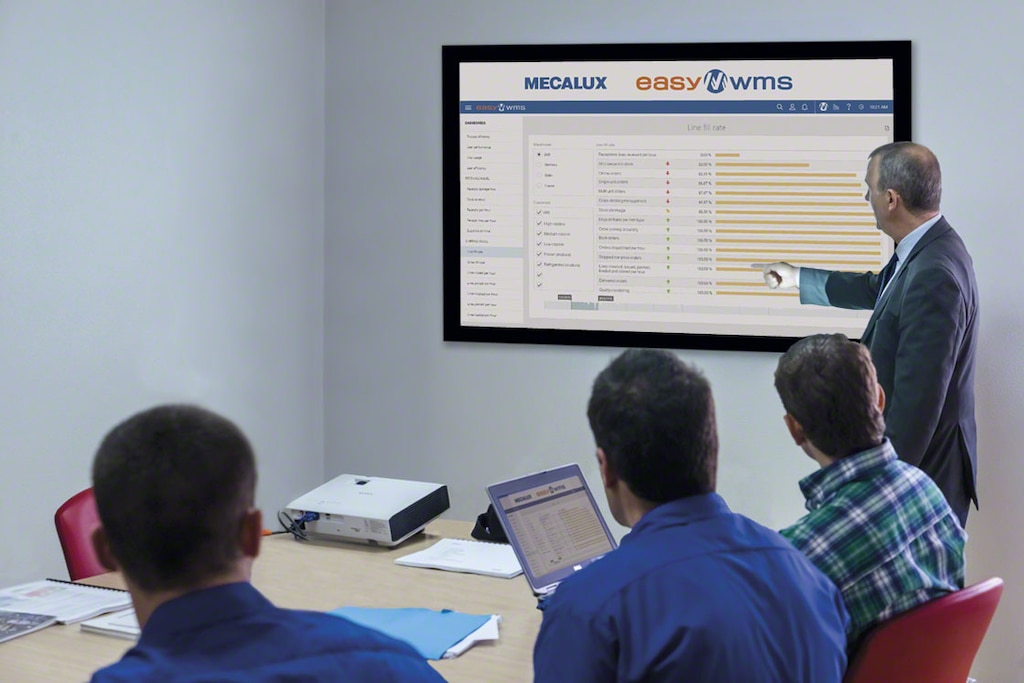
How to conduct a supply chain diagnostic?
When a consulting firm performs the diagnostic, it’s important that it work together with the logistics manager; this person knows the installation’s ins and outs better than anyone and, thus, is in a better position to propose enhancements. It’s also advisable to be equipped with specialised software that enables you to interpret warehouse data and monitor workflows in real time to then make appropriate decisions. In a diagnostic, data analysis is crucial for arriving at the right conclusions.
Take, for example, a company affected by a high volume of complaints due to late order deliveries. The simplest answer would be to attribute this problem to slow order prep. However, following the supply chain diagnostic process, it’s found that the inefficiency lies in the receiving area. Because of lack of planning, the goods remained there for too long before being stored. To solve this, various decisions could be made, such as implementing a WMS to manage inflows more efficiently, automating goods receipt and/or changing the working method by putting in place cross-docking. In any event, a data-based diagnostic is the only real way to accurately identify the causes of the problem and apply the appropriate corrective actions.
Symptom: Order delivery delays |
|
---|---|
Consequences | - Customer complaints - Returns - Bad corporate image |
Causes | - Lack of organisation in the receiving area |
Possible corrective actions | - Implement a warehouse management system - Automate goods receipt - Establish logistics planning - Change the work methodology - Set up cross-docking |
Supply chain diagnostic: techniques and methods
Conducting a supply chain diagnostic gives you a complete overview of everything that occurs in your logistics chain, identifying errors and, of course, opportunities. This analysis should be performed in phases, ranging from understanding the business, its current situation and the state of the industry to identifying the various problems specifically arising in the installation.
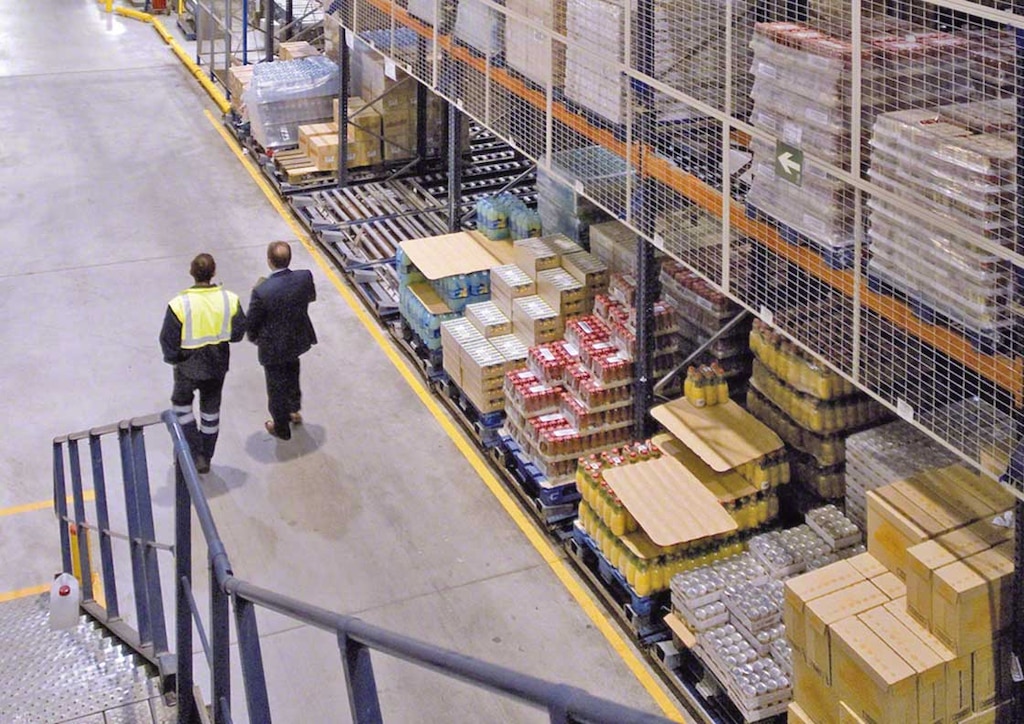
A supply chain diagnostic takes into account the particular characteristics of a company’s logistics systems (size of the logistics centre, warehouse layout, order picking method, number of workers per shift, automation level, etc.) to analyse the throughput of each operation. It’s necessary to achieve a balance between all these elements; otherwise, bottlenecks could occur, reducing productivity.
Let’s take a look at the variables to examine in a supply chain diagnostic:
- Infrastructure. The installation’s location and attributes directly impact operational performance. Therefore, the following areas should be analysed:
- Floor. This should be in good condition, without holes or dampness that could pose a risk.
- Loading and unloading docks. These are critical, so fast goods entries and exits should be a priority.
- Layout. The warehouse layout should facilitate flows and product organisation according to the ABC analysis.
- Space. The aisles should be wide enough for forklifts to maneuver as required.
- Processes. This point indicates how to perform operations in the installation in order to identify irregularities and determine whether everything is properly documented. For starters, it’s a good idea to compare how operations are carried out based on the SCOR (supply-chain operations reference) model. This tool was developed by the international organisation Supply Chain Council in 1996 (there are now 12 versions available) and serves to standardise supply chain processes.
- Inventory. Stock management is a priority for every company. A WMS such as Easy WMS from Mecalux provides you with details on the goods (date of arrival, obsolescence, turnover, availability, etc.). In addition, this software takes into account variables such as lead time and demand forecasts to avoid stockouts.
- Workplace safety. The interaction between operators and handling equipment increases the possibility of accidents. As a result, occupational risks must be evaluated. To ensure warehouse safety, aspects such as the condition of the racks and forklifts, lighting, cleanliness and aisle organisation are considered. OSHA rule 1910.176(b) effectively states that material stored in tiers must be made safe to establish safe working conditions that minimise any potential damage to people and storage equipment.
What’s measured can be upgraded
Transformation and change constitute the true essence of logistics, as all companies must adapt to new market trends if they want to stay in business. To do so, they should carry out a supply chain diagnostic assessing the quality of their processes and state of their installations.
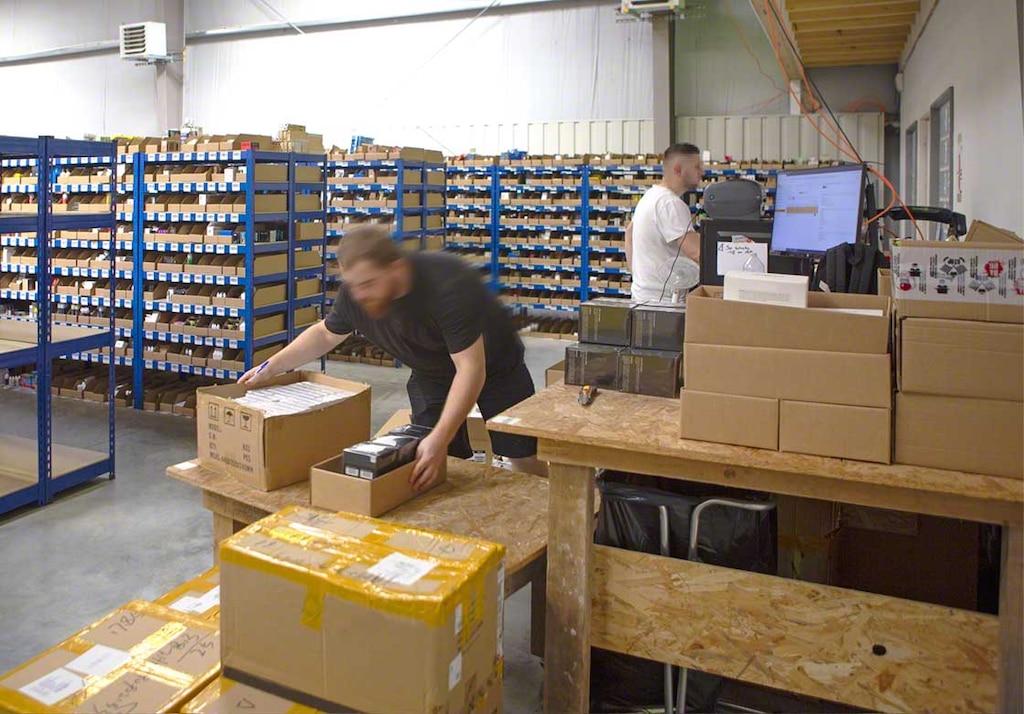
After analysing their supply chains, businesses identify and apply upgrades to achieve greater productivity and better results. For this, it’s vital to have real-time data and information on how to fulfil the various tasks.
But how do you obtain and analyse those data? Get in touch with Mecalux to learn how Supply Chain Analytics Software can help. This system groups together a large amount of data generated in the installation to then convert them into useful information. Make the most of all that information to overhaul your processes, boosting their efficiency!