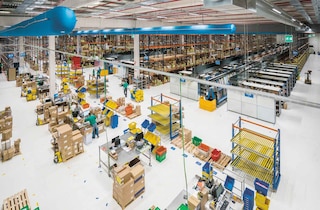
Picking and packing: what's the difference?
Although you seem to have mastered the basic rules of warehousing, in logistics, there’s always room for knowledge and improvement. That’s why, today, we’re going to go over two operations that are vital to the proper functioning of your warehouse: picking and packing. What tasks make them up? How do they differ? In our article, we’ll delve into the definitions of picking and packing and the main strategies to consider to optimise these processes.
Definition of and differences between picking and packing
Picking and packing refer to sets of tasks performed in the warehouse or distribution centre.
- Picking in logistics
In the logistics context, picking, of course, refers to the preparation of orders. It consists of:
- Advance planning.
- Routes and movements.
- Picking or extraction of goods.
- Verification and preparation of orders for dispatch.
However, if we stick to the strict meaning of the word, picking — in contrast to packing — covers the initial phase of the process, namely, the movement of the operator to the shelf and extraction of the indicated product.
- Order conditioning
Packing, meanwhile, refers to the conditioning and packaging of orders for their subsequent dispatch. The main tasks making up this operation are:
- Selection of packaging material: this is carried out according to the size, number and specific characteristics of the products. The strength of the box and the right type of filler are essential to preserve the contents of the shipment in good condition.
- Final verification of model, quantity, weight and cubic size or dimensional weight: this check is vital for catching any mistakes that may have been made in picking and for ensuring that the parcel complies with the transport service’s requirements.
- Labelling for dispatch: this is placed on the outside of the cardboard box and contains the parcel reference number, shipping address and, on occasion, its tracking number. It also has a barcode that, once scanned, accesses the information linked to it, ensuring traceability.
If the merchandise leaves the warehouse palletised, the packing process will also include pallet loading. This consists of stacking or staggering the boxes, wrapping them with straps and/or stretch wrap and affixing their corresponding labels. On the other hand, if pallets are sent as they are stored, the packing work may be reduced to quality control and labelling of the loads for dispatch.
In addition, depending on the picking method your installation follows, there might be an intermediate phase between picking and packing. This involves goods consolidation, that is, reorganising and grouping the products by order. It takes place, for example, when batch picking or wave picking are employed.
Relationship between picking and packing processes in a warehouse
In warehouses with a significant amount of orders to be prepared, it’s common to find certain operators assigned to specific picking tasks (extraction and movements) and others charged with packing (verification and final packaging). This saves time on operator runs and changes in roles so that the order prep cycle never stops.
Picking and packing are usually consecutive tasks, although the pick-to-box method brings them closer together. For coordination to be precise, it’s necessary to implement a warehouse management system (WMS). Before initiating the picking route, the WMS calculates the number of products and their size so you can select the type of packaging to be used ahead of time. Thus, after picking the merchandise off the shelf, operators place it directly in the corresponding box.

How can I streamline my picking and packing processes?
Having a warehouse management software opens up a wide range of possibilities for optimising picking and packing. Some of these are:
1. Limit the number of movements and points of contact
In logistics, the phrase “less is more” definitely rings true. The more you reduce the number of movements and handling operations, the greater your efficiency will be. Besides, second chances are too costly: ideally, picking and packing should be performed well the first time around.
To limit operator movement, you should:
- Equip yourself with picking software: the system takes a digital snapshot of the warehouse layout and designs the lists of orders to prepare, taking into account the location of the products and planning of dispatches, among other logistics parameters.
- Review the location management policy being followed according to SKU turnover.
- Make sure the pick stations or area dedicated to order prep has all the necessary equipment and packaging material. This way, workers have everything they need, which prevents interruptions in processes.
2. Analyse the efficiency of the picking method
Logistical realities are constantly changing. To maintain quality customer service, your installation needs to adapt to new methods and technologies. In this sense, WMSs help tremendously in testing changes made to picking and packing procedures. The warehouse management software allows you to collect data and display them as KPIs so you can analyse and evaluate operations at your installation.
The successful optimisation of picking and packing lies in breaking down both operations into subprocesses and calculating the standard times dedicated to performing each one. In this regard, the Labor Management System module increases control and improves operator productivity.
3. Assess automated solutions
One of the areas with the most options and potential for automation is picking and packing. Picking, in the load extraction and transport sense, has come a long way in logistics facilities. Systems such as stacker cranes and conveyors are made up of extremely effective technology to streamline the more repetitive load transfer and handling tasks.
Packing can also be fuly automated via anthropomorphic robots. However, due to cost and throughput, these solutions are a good match only for warehouses with massive order volumes that, in addition, have to follow regular patterns. In installations with very intense picking and packing work, it’s not always possible to automate to this degree due to the volatility and unpredictability of demand. This is the case for many e-commerce warehouses.
However, less ambitious automatic systems such as voice picking devices and cobots that help prepare orders can considerably boost workers’ productivity when performing these tasks.

4. Don’t forget about the packaging
In making the most of packing, you can’t overlook the packaging materials used in your warehouse. The following examples facilitate the packing process:
- Installation of automatic packaging machines: these produce paper filler or air bags and serve them directly to operators, who merely have to place them inside the parcels. Likewise, automatic stretch wrappers wrap and seal the pallets, relieving the operators of this task.
- Standardisation of packaging: this limits the space used for these materials, thus, preventing errors and exorbitant amounts of multi-sized packaging materials.
- Self-assembly boxes: these save time and reduce operator movements.
The lines between picking and packing are often blurred, since warehouse material flows are closely interlinked. Nevertheless, it’s advisable to analyse each subprocess in depth to locate those points of friction that are jeopardising warehouse efficiency.
If the complexity of picking and packing operations is interfering with the efficient management of your installation, be sure to get in touch. One of our specialists will help you find the solution you need.