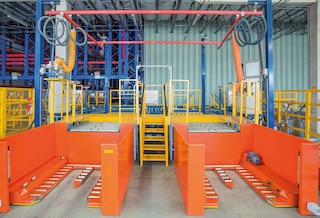
Picking area: how to design and equip the one for your warehouse
Studying the design of the picking and order preparation area is essential to ensure goods flows and streamline the warehouse sufficiently to satisfy customer demands. Because of this, the picking area can take many forms, depending on unit loads, service level and the installation’s handling equipment.
In this article, we’ll analyse design options for the picking area according to two factors: its location within the layout and the configuration of the pick stations themselves.
Picking area location options within the layout
Let’s take a look at the most common ones:
- Picking area at the front, a typical solution for automated installations
On occasion, the picking area is designed in conjunction with the dispatch zone. This is because the verification, packaging and freight groupage tasks (where applicable) account for the final phase of order prep, in the run-up to goods shipments.
This is a standard option for automated warehouses for pallets and boxes with high-density storage systems combined with stacker cranes and/or the Pallet Shuttle system. Roller conveyors transport the loads to the pick stations. There, operators execute the orders given by the WMS, check them and finish loading pallets for shipments as required. Examples of this type of picking can be seen in installations we built for Venis (Porcelanosa Group) in Spain and Basf in Brazil.
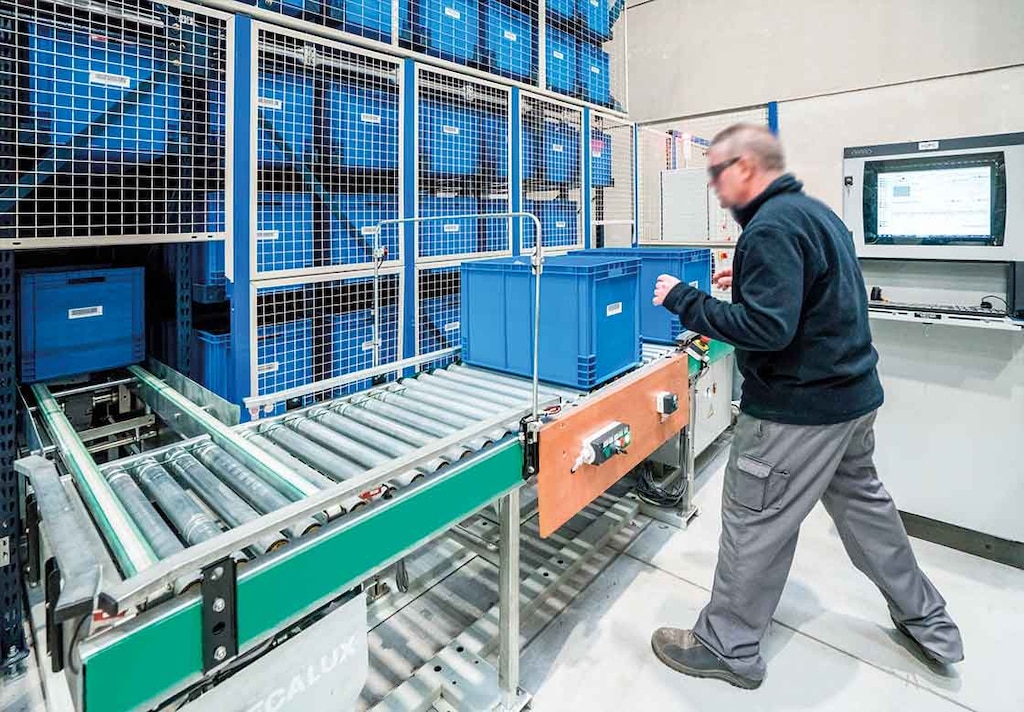
- Picking area in the center or at the side, for installations with high-volume order prep
In installations whose operations revolve around order preparation, picking tasks can become complicated. Thus, it’s necessary to distribute these processes over a larger area in the layout. This makes it possible to prepare more orders at the same time, although it’s also more labor-intensive. To compensate for this increased activity, one practical solution is to install conveyor circuits, which eliminate a large share of operator movements.
In these types of warehouses, the picking area extends throughout the warehouse. The backbone of this zone is a line of roller conveyors along with scattered tables and pick stations. Operators remove the products from the shelves and deposit them in boxes (in the form of final packaging or plastic boxes) on the conveyor. The goods can be extracted from live storage for picking via the pick-to-light system or directly from the standard picking shelves using the pick-to-cart method.
Examples of organising the picking area in this way can be found at the Spanish army’s logistics center (PCAMI) in Spain and at the installation of e-commerce retailer eobuwie.pl in Poland, which is also equipped with a sorter to classify products by order and transport route.
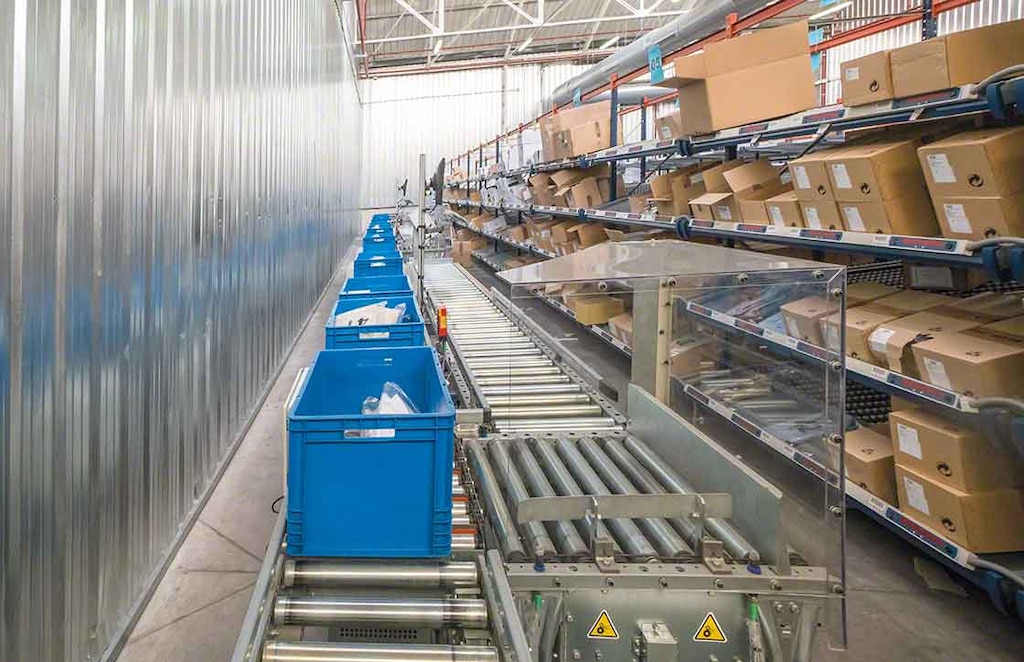
Pick station configuration
To design the picking area, you have to take into account the ergonomics and safety of the workers that are going to be operating in it. The pick stations should have a work table with a computer and printer for managing labelling tasks and documents associated with the order, as well as for operating with the warehouse management software.
In addition, there’s a wide variety of automatic systems with which you can outfit your pick stations, for example:
- Hydraulic lift tables whose height can be adjusted to make manual pallet loading more ergonomic. They’re usually integrated into the conveyor circuit and include other mechanisms that control goods weight and volume.
- Pneumatic arms to lift and move heavy loads manually while guided by operators.
- Devices that make picking tasks more accurate and comfortable, such as the voice-picking system, which frees up operators’ hands.
- Packaging machines that automatically generate filler for packages, or automated strapping or stretch-wrapping systems for pallets.
In search of the optimal picking area design
In any installation, picking tasks bear the brunt of the operations, not only because of the complexity of organising them, but also due to the movements and labor needed to execute them.
Therefore, it is vital to provide your picking area with the ideal layout and equipment. If you think your warehouse is floundering in the order prep department, get in touch. One of our experts will check to see whether your picking area has the right setup for your installation’s operational requirements.