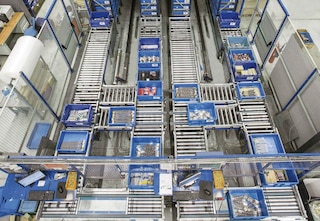
Kanban system: what is it and how does it work in logistics?
The Kanban system organises the supply and production of goods in manufacturing processes that operate according to the just-in-time (JIT) methodology (having the only necessary amount of raw materials on hand at the right time). The end goal is to adjust manufacturing capacity to demand in order to avoid overstocking and unnecessary wait times between processes.
The Kanban method was developed at Toyota in the 1950s as part of the Lean manufacturing methodology (minimising waste to increase productivity). Industrial engineer Taiichi Ohno designed the production model, which was identified as the solution for coping with the major depression into which Japanese industry had sunk following the Second World War.
What’s the Kanban system? Definition and origin
The Kanban methodology establishes a protocol for stock replenishment. It’s a system for communicating both production and materials replenishment orders. Kanban is used in production models that respond directly to demand (pull system, whereby manufacture of the product doesn’t begin until the production plant receives a firm order from the customer).
Taiichi Ohno devised the Kanban system inspired by the replenishment rules of US supermarkets. That is, customers remove the products, all of which are labelled, from the shelves. At the check out, the cash register compiles all the SKUs sold and sends a replenishment order to the warehouse, which identifies the goods using the same system. Once the replacement items are put on the supermarket shelves, the installation, in turn, sends another replenishment order to its suppliers or manufacturers, and so on throughout the supply chain. To determine when replenishment orders are triggered, the reorder point system is applied.
How does it work? Kanban cards and boards
The literal translation of Kanban in Japanese is “signboard.” This is because, originally, poster board cards were used to request the parts that were needed from the previous process. When the replenishment order was completed, the Kanban card went back into its original pigeonhole.
These cards contained the information that identified each batch of material: SKU, code, lot size, destination, customer that requested it, etc. The cards were hung on each of the containers or shelves that held the product.
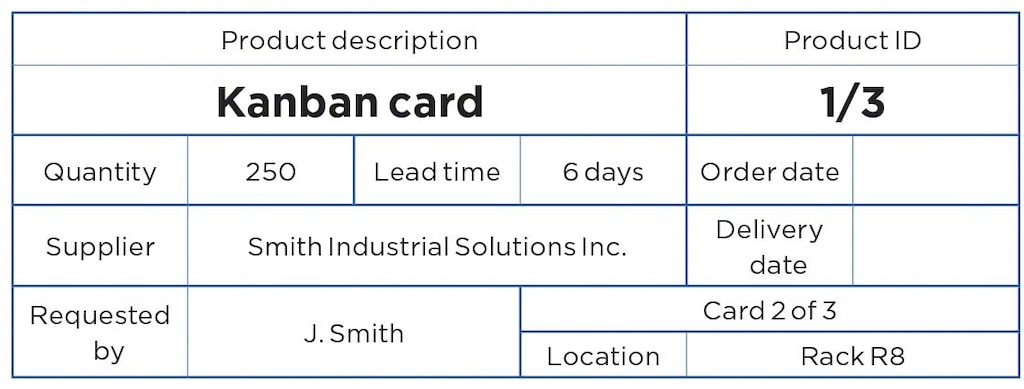
Nowadays, the Kanban system has been replaced by software applications, which activate the replenishment process. The working system can also be represented by means of Kanban boards, which consist of various columns where the cards or virtual labels can be placed. In this way, each column indicates the status of each task and the person in charge of carrying it out.
Although the Kanban system was originally conceived in an industrial context, nowadays, it’s also implemented in the management of all kinds of projects, such as those related to software development.
Kanban card types
There are two kinds of Kanban cards:
There are two kinds of Kanban cards:
- Transportation Kanban: these cards show how much product needs to be replenished to complete the next process in the supply chain. Taking the example of the supermarket, the transportation Kanban would be applied to indicate that a certain type of merchandise was sold and needs to be moved from the warehouse to the store shelf.
- Production Kanban: these cards are used to request the manufacture of a product. Taking the same example, this type of Kanban card would be issued by the installation when it is out of stock (because it has sent it to the store).
The diagram below illustrates the chain reaction initiated by the production and transportation Kanban cards in a simplified production line:
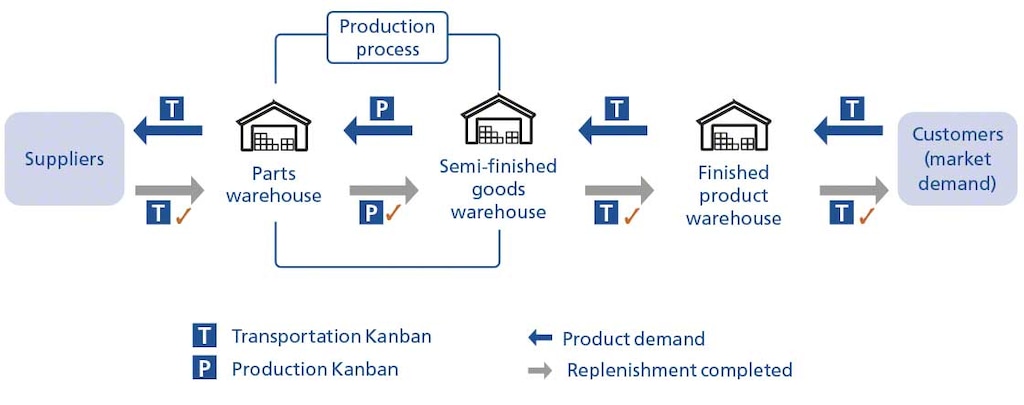
Advantages of the Kanban method in logistics and production
The Kanban system is a perfect match for the just-in-time method because it:
- Allows you to visualise the work being carried out and, thus, easily identify each stage of the production or replenishment cycle.
- Enables you to set work in progress (WIP) limits to prevent bottlenecks.
- Lets you measure lead times between processes, that is, the time it takes to complete each phase.
- Works, by linking the various stages, as a control system for production and for the materials available in the different warehouses.
- Prevents overproduction and excess stock, thereby saving storage space.
Disadvantages of the Kanban system
Due to certain restrictions imposed by Kanban, it’s not always the most appropriate method:
- The Kanban system provides optimal results when the production flow is distributed uniformly throughout the year and is organised in short series with similar volumes. However, if the business is subject to high demand volatility that requires sudden adjustments to production, the Kanban method proves inefficient and is not recommended.
- If one of the links fails, the supply chain could experience delays (if a card is lost or an order is issued incorrectly, for example).
- The Kanban system isn’t the most flexible for coping with major changes in product manufacturing techniques.
- It won’t work properly if the suppliers don’t implement the same Kanban rules for procurement.
When to use Kanban in the warehouse: the role of a WMS
Today, implementation of the Kanban method in organisations no longer involves paper cards: this is now done by means of a warehouse management system (Easy WMS, for instance) in combination with automatic identification systems, such as barcodes and RFID tags. Every datum recorded in the WMS acts as a Kanban card, since, when reading the data with a scanner, the system returns all the information linked to that SKU.
In logistics, the Kanban method is used to organise restocking on different levels:
Kanban under one roof
If the locations dedicated to picking and storage are divided, the Kanban system is especially helpful when replenishing stock from the picking shelves.
Once the SKUs in those picking slots have been exhausted, the WMS sends an automatic replenishment alert that functions as a Kanban card. Nevertheless, operators can also activate this notification manually when they detect material shortage.
In this way, the change in location of the goods is scheduled according to priority, although this action is usually carried out during off-peak times in the installation (this occurs, for example, in wave picking).
When moving products from storage to picking, if an operator notices that there are no more SKUs in the storage area either, the WMS can send a notification directly to the purchasing department so that it takes this into account in its supplier order requests.
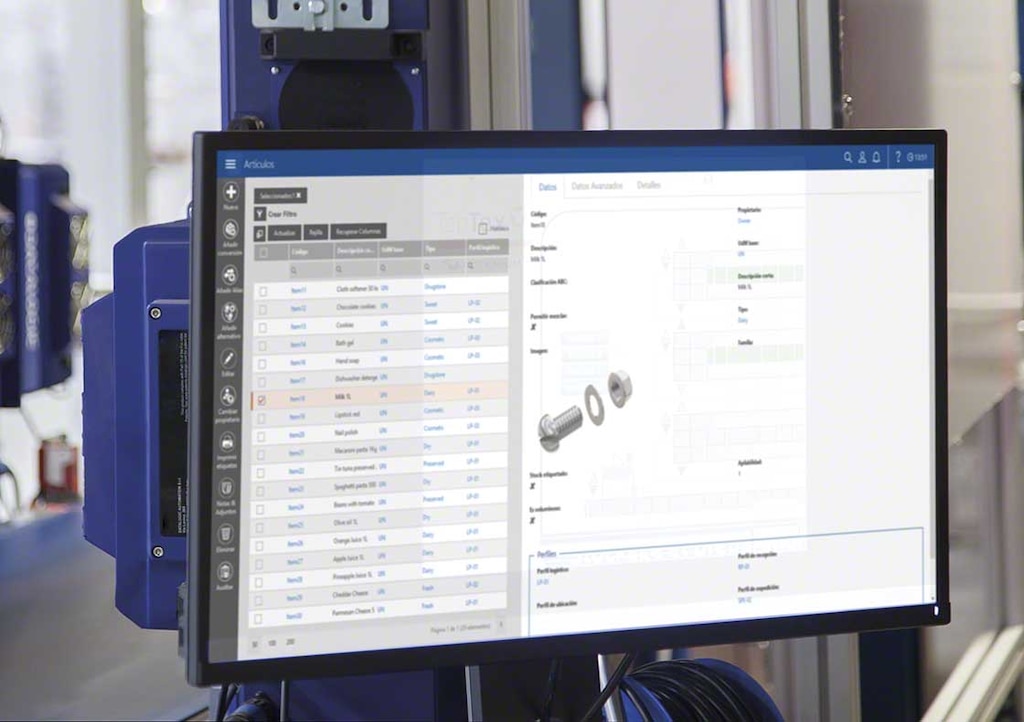
Kanban in a network of logistics warehouses
The Kanban method can also be implemented in companies that work with inventory distributed among various storage centres. These facilities can serve a single production line (such as in manufacturing logistics) or form part of the same logistics network (as in retail supply chains).
Let’s take a look at how the Kanban system works in each case and the functions of a WMS:
- Kanban in production installations: the main feature of warehouses that supply production centres is that they handle inventory classified as raw materials, semi-finished goods, and finished products. To prevent stockouts in the production process, it’s fundamental to have computerised stock control. In this vein, WMS for Manufacturing operates according to the Kanban system: when a new order is received, the WMS issues work orders to the production centre and monitors the safety stock available for each SKU.
- Kanban in retail supply chains: in this case, the logistics network is made up of installations (central and regional) and physical shops. Following the Kanban method, product demand is registered at the points of sale; from there, the replenishment orders to the warehouses are generated. In this scenario, the WMS works as a catalyst for replenishment between centres, as it contains overall inventory data. Plus, in the case of Mecalux’s Easy WMS, the Store Fulfillment module makes it possible to organise and arrange stock movements between centres — without intermediaries — making the most of your company’s logistics capacity.
Stock management with the Kanban system
Implementing the traditional Kanban method with an extensive inventory spread among various facilities and a very high volume of SKUs is inefficient due to the increasing complexity. However, it is possible to plan stock replenishment and take advantage of the benefits of the Kanban system with the help of a WMS.
Easy WMS features advanced functionalities for integrated inventory management and enables you to operate with different restocking rules. To learn more about how our WMS works, get in touch. One of our specialists will show you in detail how it can help to optimally manage your installation.