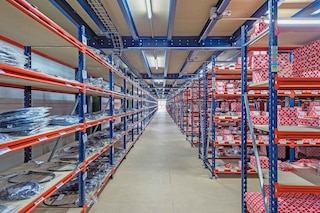
Industrial Storage: How to be a skilled product organiser
Sometimes, knowing where to start is what makes storage planning not quite as easy as it looks. That said, don’t let this challenge scare you off track. In fact, if you can achieve optimal industrial storage, all your warehouse operations will reap the benefits, logistics will flow and handling too.
Each SKU has its own story
Even before you dive in and start organising your goods or products, you need to pre-sort them by:
- Product type: Are my products in gas, liquid or solid form?
- Packaging: How are my SKUs packaged? Am I dealing with goods set on pallets or in racks, cans, storage lockers or barrels?
- Features: Are my goods big or small, heavy or bulky?
- Temperature conditions: Are some goods more sensitive to heat, humidity, movement or light?
These issues help narrow down how you will go about organising your goods in the choicest possible way. Actually, for example, very heavy liquids and unpackaged goods don’t need the same storage approach as other more weather sensitive goods.
Pick a storage system or solution
Once you have a solid grip on the characteristics of the SKUs you need to store, move onto the next step and choose a storage solution that meets your needs. Getting a hold of quality storage material is fundamental, material that will last long enough for your investment to more than pay off.
To hit the nail on the head, keep these points in mind:
- SKU rotation: As a matter of fact, if your SKUs are slow movers, the best option is a high-density rack storage solution.
- Expiration dates: Live pallet racking systems are often the method that best suits companies that sell and distribute food products.
- Warehouse type: Are you dealing with cold-storage, traditional rack or courier storage?
- Your aims: If automation is on your mind, weigh the pros and cons of an Automated Storage/Retrieval System.
It is crucial to pin down all these issues so you can choose the storage solution that is right for you. In the end, your facility will stay safe, with a smooth-running product organisation.
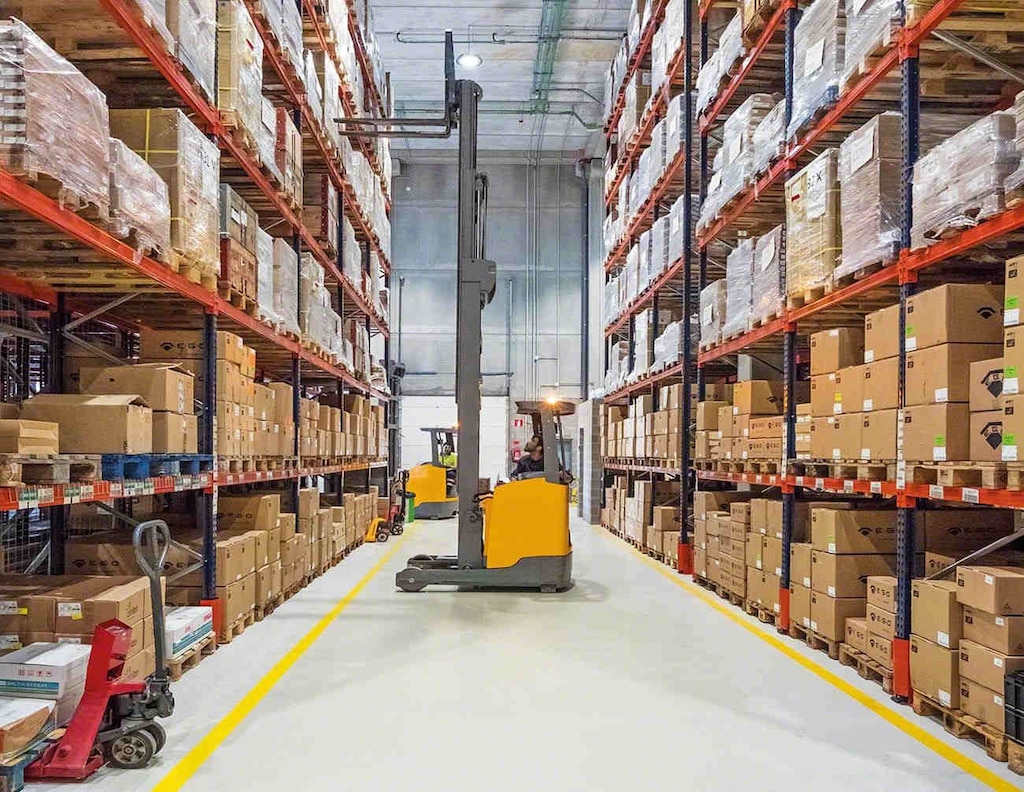
Label your racks, containers, etc.
Every single one of these units or elements plays a vital part in your warehouse. So, that’s why your installation should be labelled or identified before diving into any storage process.
This labelling system is essential to guarantee proper material tracking, and not only for the sake of the goods.
By doing so, you can identify your equipment, separating them into different categories, like racks, containers, forklifts, etc.
Don’t forget to take this step if you want to ensure your material’s durability.
Regular maintenance is key
Schedule periodic checks and maintenance of your storage solutions so that your warehouse is always in perfect order.
Caring for your material and equipment will, in turn, keep your goods in top condition while they are stored and avoid breakdowns and accidents.
Rethink storage processes
Organising your warehouse is an ‘unending cycle’. By being circular, the whole process loops back to where it began, which is your chance to rework storage techniques from time to time. The objective of this re-examination is to ensure efficiency, productivity, and optimisation of your product arrangement.
If your company realises it must rethink its warehouse’s layout, it is even more crucial than ever to start the entire industrial storage process all over again.
Anyone who works in logistics knows that the sector’s keywords are «storage» and «organisation». Without being organised, a company experiences a drain on its time and money, safety levels drop in its facilities, and damage is more frequent. Consequently, it lays the way for customer dissatisfaction or strained user experiences.