Reducing movements is one good way of improving operator efficiency, but not the only one. To go further and do away with dispatch notes, pick-to-light (PTL) devices can be used.
Example of a pick-to-light system in a pharmaceutical lab.
In front of each channel in the carton live storage racks is a numerical sensor with buttons. These devices are controlled by the warehouse management system (WMS). This software turns on the light sensor (to indicate to the operator that goods have to be removed from this channel) and shows onscreen how many units of the SKU in question have to be picked.
When the operator finishes removing the corresponding units, they press a key to confirm that the operation has been completed. This is relayed to the WMS, which turns off the light. When a new order must be prepared, the lights in the positions where the products have to be removed are automatically switched on. There are pick-to-light systems that enable several orders to be prepared at the same time.
The two major advantages of this type of picking are the speed they provide and the considerable reduction in errors that are possible in the preparation of orders.
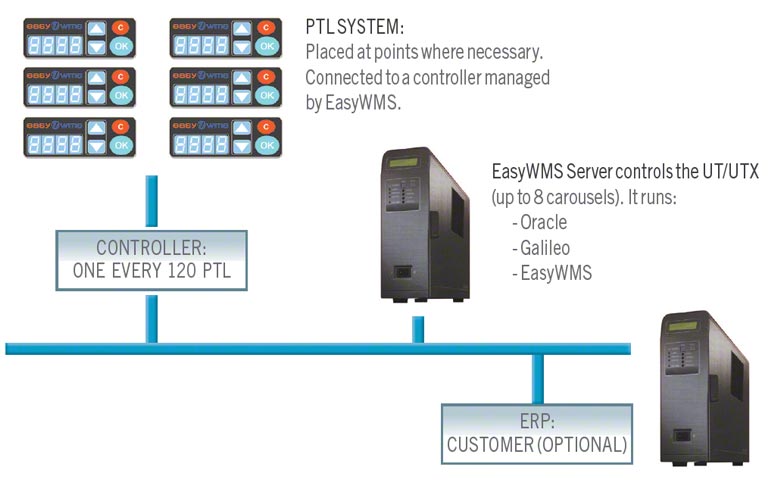