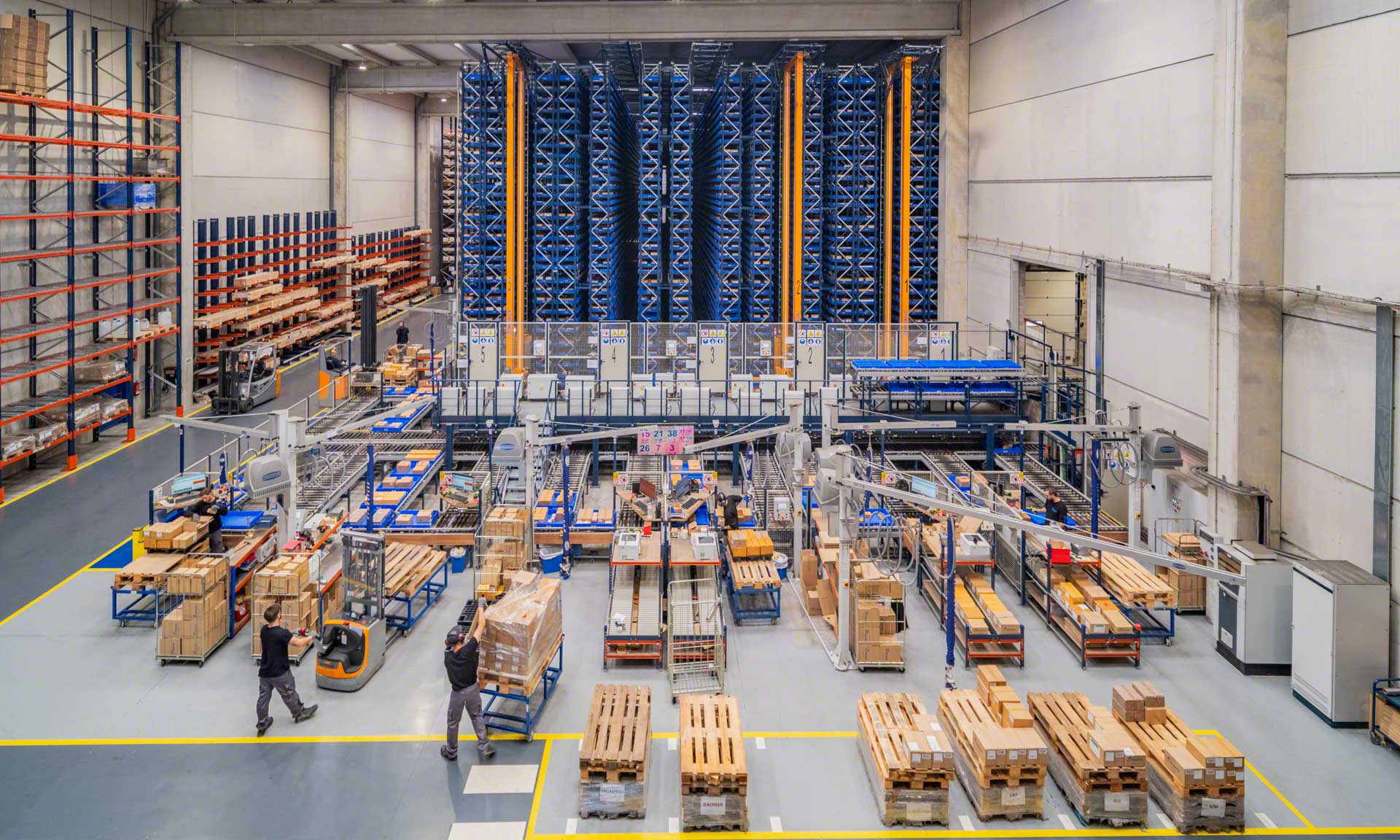
All-in-one solution for Hispanox: managing over a billion parts stocked
Easy WMS manages three warehouses for stainless steel bolt distributor Hispanox, enabling it to fulfil 1,800 order lines daily.

Hispanox, a leading Spanish stainless steel bolt distributor, has installed a miniload system managed by Easy WMS software. Technology and digitalisation enable the company to prepare more orders a day without errors.
Hispanox: specialising in fasteners and screws
Hispanox distributes fastening elements such as nuts, bolts and washers manufactured primarily in stainless steel. The company supplies high-quality solutions for industries such as construction, automotive and renewable energies. Founded in 1987, Hispanox stands out for its ability to adapt to its customers’ specific needs, offering standard products and personalised solutions.
CHALLENGES
|
SOLUTIONS
|
BENEFITS
|
---|
Hispanox, a leading Spanish distributor of stainless steel bolts, houses more than a billion items imported from Asia and subsequently sent to its clients in southern Europe.
When it started doing business, the company had two warehouses at its logistics centre in Polinyà (Barcelona). The facilities were equipped with Mecalux pallet racking, which housed the 22,000 mainly small SKUs in Hispanox’s catalogue. Over time, the distributor’s logistics operations became overwhelmed by the increased demand. This prompted it to plan a modernisation and expansion project for a third warehouse.
Mecalux has supported Hispanox’s growth from the beginning. For the new facility, the intralogistics specialist designed and installed a miniload system. This solution boosts putaway and picking productivity while streamlining logistics operations. Thanks to the uninterrupted flow provided by the automatic handling equipment, the automated storage and retrieval system (AS/RS) for boxes optimises putaway, order fulfilment and shipping.
Mecalux also tailored this logistics modernisation process to the distributor’s omnichannel strategy to meet the needs of companies that place orders online. The all-in-one solution from Mecalux allows Hispanox to pick 1,800 order lines a day, 30% more than before. The Easy WMS warehouse management system plays a fundamental role in this raised productivity. It serves as the mastermind of Hispanox’s entire logistics centre, supervising automatic and manual operations across the three facilities.
The company distributes more than one billion stocked parts in various storage systems based on their attributes and turnover rates. For example, smaller and high-selling products are slotted in the miniload system. Larger merchandise, meanwhile, is placed on pallet racking. Hispanox has connected its three facilities to speed up internal bin and pallet transport. The end-to-end Mecalux solution was completed with cantilever racking, picking shelves and live channels.
Automated storage in a minimal space
The AS/RS stacker cranes for boxes and conveyors enable goods-to-person order picking. This streamlines operations by moving products to operator pick stations as directed by Easy WMS.
The miniload system has five aisles spanning 50 m long. In each aisle, a stacker crane for boxes inserts and removes goods from their locations. The two double-deep aisles on the ends optimise space and expand capacity, and the stacker cranes operating in them are equipped with telescopic forks. The entire system has been customised to accommodate three types of bins weighing up to 100 kg.
In addition to agile movements, one characteristic of this miniload AS/RS that most interested Hispanox was its ability to leverage the available surface area to house more products. In just over 770 m², it stores 25,780 totes.
30% more order lines
The picking process begins in the first and second warehouses, which supply the miniload system in the third facility with the items used to fill orders at the pick stations.
A decanting station has been installed in the second warehouse. There, pallets are broken down, and items are removed from their original packaging and placed into plastic bins. The station’s two mechanical handling arms enable operators to work ergonomically. The bins are subsequently placed onto a conveyor system, which transports them to the automated warehouse. A lift bridges the difference in height between the two facilities.
When a customer places an order, Easy WMS directs the product to be transported from the AS/RS to one of seven pick stations outfitted with handling arms, computers and RF scanners. This setup allows operators to fulfil orders quickly. Once picking is finished, the bins are placed on pallets sent to the loading docks.
Hispanox’s low-turnover products are stored on picking shelves located next to the miniload system in the third facility. Meanwhile, the cantilever racking houses long rods. The company employs the person-to-goods order picking strategy for these items. In this case, operators use RF scanners to follow Easy WMS’s instructions during the picking process. They also use these devices in the docking area, where they consolidate orders with products from the logistics centre’s various systems.
Easy WMS: the logistics mastermind
Mecalux’s Easy WMS oversees the operations and movements of all Hispanox storage systems, including the AS/RS, pallets and cantilever racking, and pick stations. The software strictly monitors all operations through continuous, bidirectional communication with Hispanox’s Sage ERP system.
For every product that arrives at the miniload AS/RS, the Mecalux software receives an advance shipping notice (ASN) from the ERP. Based on this message, Easy WMS uses a set of rules and algorithms to assign a location to each item according to its characteristics and turnover rate. Hispanox has total traceability of all SKUs stored in its manual and automated storage systems. It knows the location of all its products in real time and can accurately track their movements through the warehouse management software.
Easy WMS’s Multi-Carrier Shipping Software module incorporates advanced capabilities for effectively performing the packing, labelling and shipping processes. The system communicates directly with carrier software to facilitate order distribution. It sends documentation to shipping agencies, which forward the data to generate the labels and tracking number. This way, when the vehicles arrive at the warehouse, they have all the information they need and simply have to collect the orders.
Warehouse with 1,800 order lines daily
The results achieved by automating and digitalising Hispanox’s logistics operations speak for themselves: the company has increased its order lines picked by 30%.
It benefits from a centre prepared to stock more than a billion parts and manage the traceability of over 22,000 SKUs. This outcome was made possible by Hispanox’s expertise and Mecalux’s comprehensive logistics solution.
Gallery
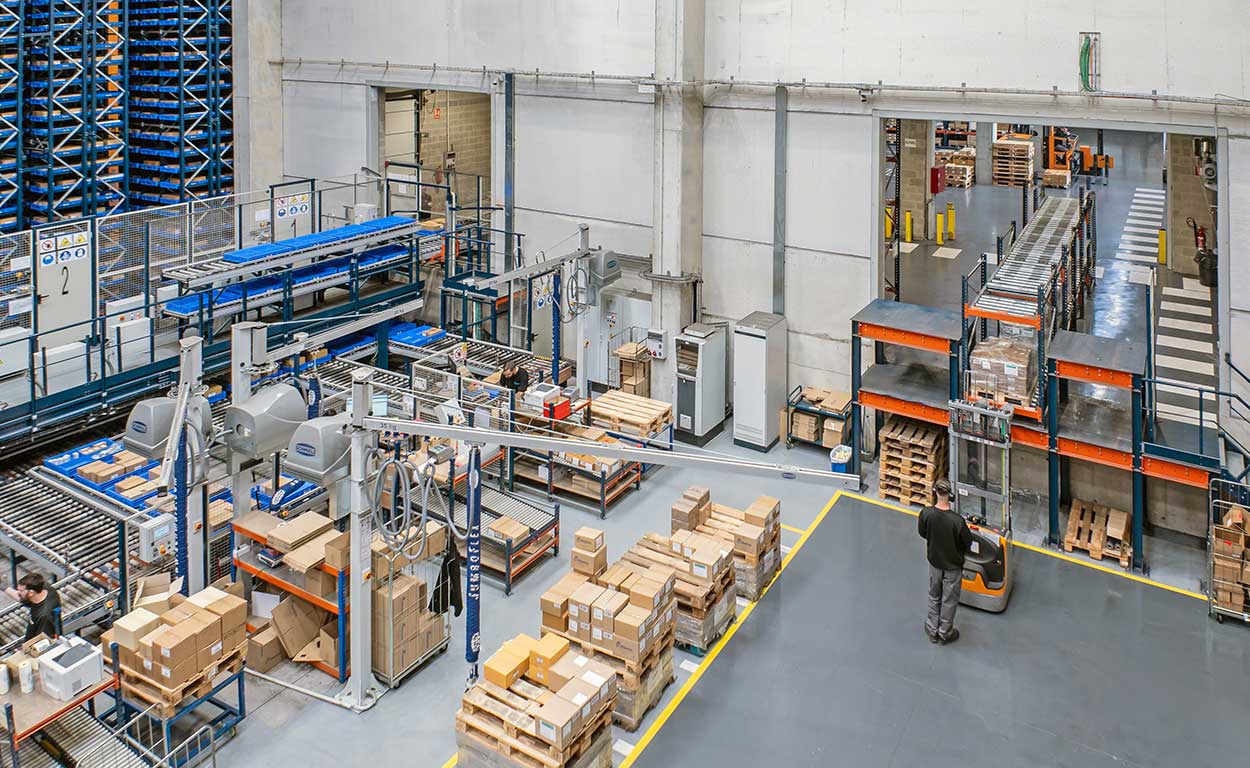
Conveyors streamline internal transport in Hispanox’s facility
Ask an expert