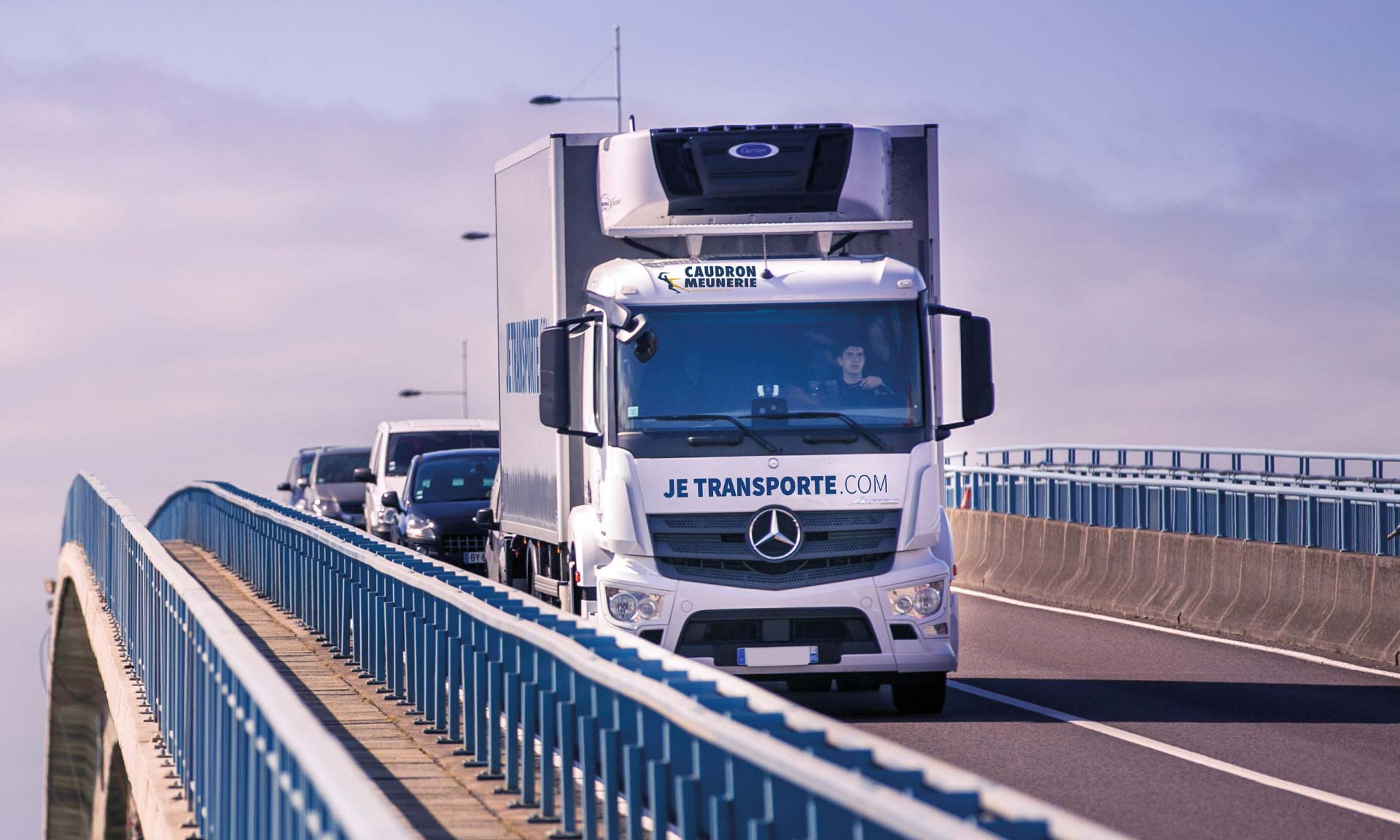
Easy WMS ensures traceability of flour for 40% of France’s bakeries
Logistics service provider Caudron Meunerie ships 250 tonnes of milled product daily.
Caudron Meunerie, a logistics provider specialising in flour, has implemented Easy WMS in its warehouse in France to monitor inventory. The company manages the daily distribution of 250 tonnes of flour to bakers nationwide.
Caudron Meunerie: Leader in flour management
Caudron Meunerie is a third-party logistics (3PL) provider specialising in raw material for bakeries. Since 2020, it has been part of the MOUSSET-JETRANSPORTE group, a transport company with over 60 years of experience in France. The 3PL provider supplies 4 in 10 bakers nationwide, supporting the daily production of 11 million baguettes enjoyed by 22 million French people. Caudron Meunerie has a team of over 420 employees and a fleet of 360 vehicles with tipping tanks for bulk flour, tailored to the characteristics and needs of its clients.
CHALLENGES
|
SOLUTIONS
|
BENEFITS
|
---|
Logistics service provider Caudron Meunerie stores more than 8,000 tonnes of flour in its distribution centre (DC) in Bondoufle (France). “We consolidated two warehouses into a single 8,500 m² facility to meet the growing demand of the French market. Our new DC provides more storage capacity and flexibility for handling pallets,” says Logistics Manager Abdesslam Laoukili. “We work safely thanks to wider aisles and a height-optimised storage system from Mecalux.”
The 3PL provider has installed Easy WMS software to ensure inventory traceability and boost all warehouse operations. These span from the arrival of flour from the mills to its delivery to 40% of France’s bakeries. “The Mecalux software has modernised our logistics processes and enabled us to adapt them to consumers’ changing needs,” says Laoukili.
Integration and communication with carriers
One of Easy WMS’s key features is its ability to integrate with other computer systems. This has streamlined supply chain management for Caudron Meunerie.
“We were looking for software that could communicate with our clients to exchange information regarding product handling,” says Laoukili. Bakers notify Caudron Meunerie about the type and quantity of flour they need so that Easy WMS can coordinate order fulfilment.
The Mecalux software has also been integrated with the company’s AxioRoute transport management system (TMS), which plans and organises delivery routes across the country. “The connection between Easy WMS and our TMS minimises distribution errors and guarantees all shipments have the required documentation,” says Laoukili.
The Mecalux system directs fulfilment. Once completed, it strategically arranges the placement of orders within each vehicle based on delivery routes. This way, Caudron Meunerie avoids making incorrect deliveries that could negatively impact its customer service.
Easy WMS installed autonomously
Caudron Meunerie’s parent company, the MOUSSET-JETRANSPORTE group, had already been using Easy WMS in some of its warehouses, so the company was familiar with the system. With the experience and know-how gained from previous implementations, Caudron Meunerie took the initiative to deploy Easy WMS independently in the Bondoufle DC. Mecalux’s technical team remained remotely connected solely to guarantee a smooth and issue-free start of production.
The 3PL used Easy S, a digital tool that allowed it to configure and customise the software. Caudron Meunerie carried out four processes:
- Warehouse configuration. This stage consisted of entering the storage racking, available item types, and work areas into the software. The initial configuration was crucial for maximising the warehouse management system’s efficiency and accuracy.
- Software parametrisation. The business determined the criteria for assigning each item a location and distributing tasks among operators. With these data, the system now operates optimally and is tailored to the specific needs and characteristics of the DC.
- Staff training. Operators, area managers, and key users gained proficiency in the main software tools and features to manage the warehouse’s daily operations.
- Go-live. This stage involved activating the software and running tests to ensure the proper implementation of all processes and functionalities. Final adjustments were made, with system availability guaranteed at all times.
Efficient flour management
The DC stands out for its high work pace. Every day, it receives flour from 13 mills and ships 250 tonnes to 40% of France’s bakeries.
“Our products have a high turnover. They’re distributed in less than a month, especially wheat flours, which are the most widely used and consumed,” says Laoukili. The software sends instructions to operators. Assisted by exoskeletons, they handle and transport 25 kg flour sacks with agility.
“We’ve gone from working with pen and paper to automatically connecting with our customers to know their needs and ship products in record time,” says Laoukili. Orders are fulfilled every afternoon and shipped as soon as possible for delivery starting at 2:00 a.m., when bakers need the raw materials to begin preparing their products.
Speedier service
Easy WMS has represented a major step forward in inventory traceability and the modernisation of Caudron Meunerie’s logistics processes. With this digital tool, the company manages orders more efficiently and accurately, delivering the best bread to tables across France.
The Mecalux software has modernised our logistics processes and enabled us to adapt them to consumers’ changing needs.
Gallery
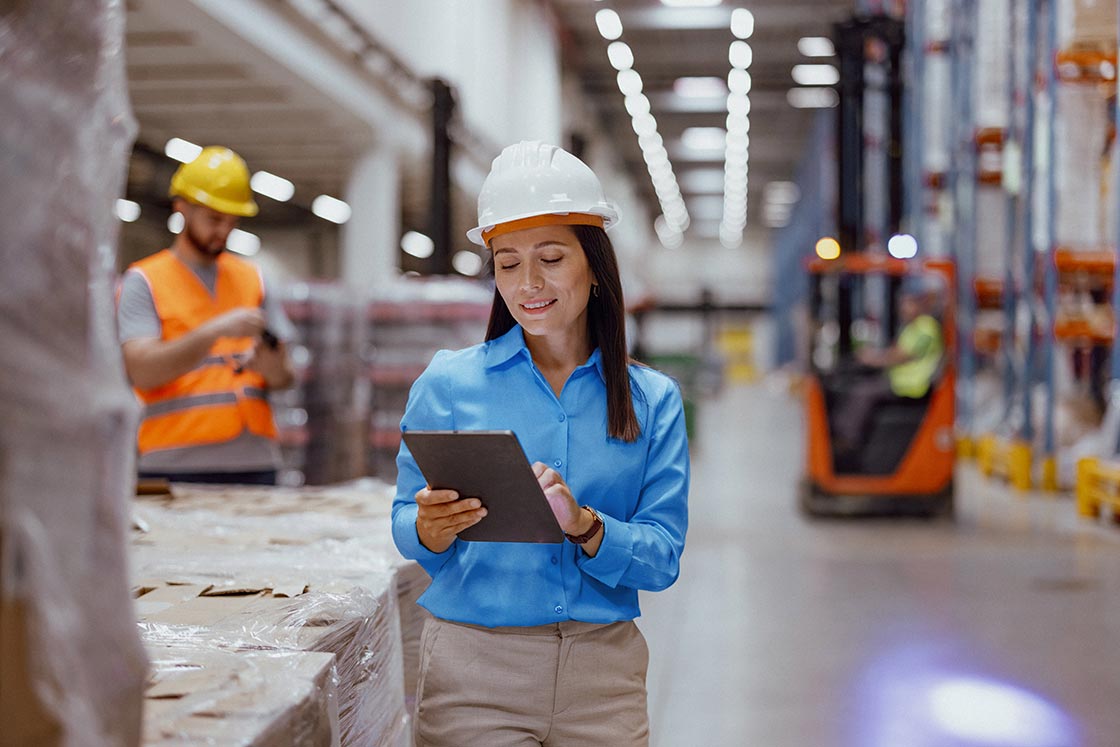
Caudron Meunerie’s warehouse ships 250 tonnes of flour daily
Ask an expert