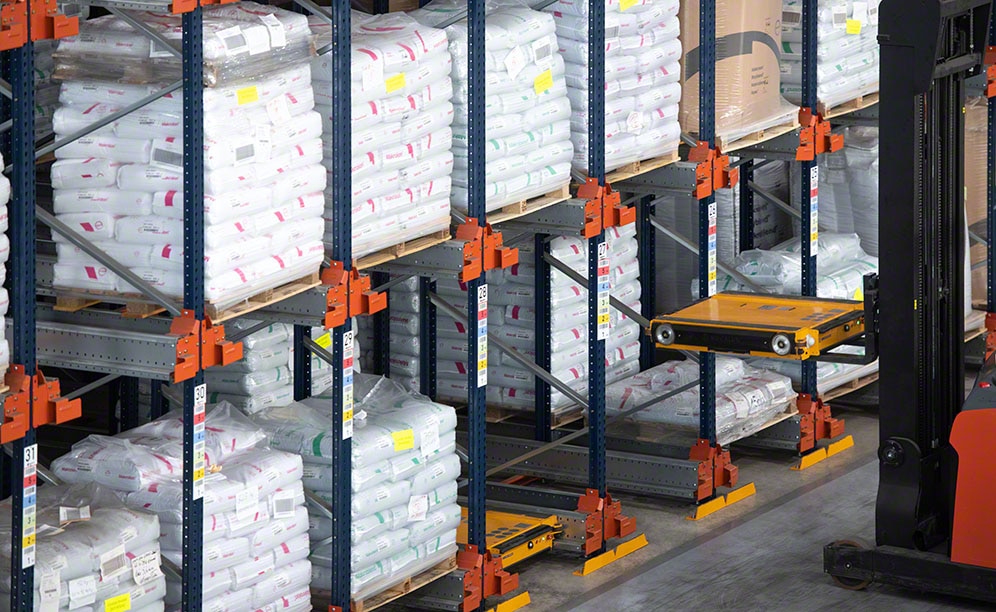
Industrial services company WISAG is opening a warehouse in Germany
Mecalux has equipped the warehouse of industrial services company WISAG with the Pallet Shuttle and Easy WMS
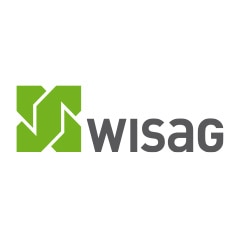
Chemicals require impeccable treatment and special storage conditions. That is why WISAG, one of Germany’s biggest service companies, has implemented the Easy WMS warehouse management system in its Krefeld warehouse. The objective is to organise all the goods of one of its customers, a prestigious multinational chemical company, as efficiently as possible while providing top-quality service. The centre, equipped with two racking units with the Pallet Shuttle system, has a total storage capacity of 16,000 pallets.
A new line of business
With the Logistics Competence Centre, WISAG Industry Service Group, one of Germany’s leading providers of industrial services, has opened a new business line. The centre consists of a new 10,000 m² warehouse in the city of Krefeld (Germany) where the logistics infrastructure of a leading multinational company in the chemical and pharmaceutical sectors is managed. There, all of this company’s products are organised and shipped, stored in industrial bags (like big bags) and in octabins on pallets.
Storage space
Every day, this centre receives an average of 500 pallets from production that are stored and then distributed to the chemical company’s customers throughout Europe. WISAG asked for Mecalux’s help in finding a solution that would enable it to accommodate all its items and manage them efficiently to prevent any mistakes.
After analysing the warehouse’s special features, Mecalux equipped it with two racking units with the Pallet Shuttle system to optimise the storage area. These stand 9.5 m high, are divided into five levels and have storage capacity for 10,695 pallets with a maximum unit weight of 1,000 kg.
WISAG chose this high-density system because it is particularly suitable for handling a small number of SKUs, each with a large volume of pallets. This solution also makes it easier for its customer’s chemicals to remain in storage for the appropriate time and, when the time comes, to be mass-distributed to end customers in the manufacturing industry.
One of the advantages of having a motorised shuttle is that product handling is completely safe, preventing sudden movements and blows (which is imperative, especially with chemicals).
Storage processes with the Pallet Shuttle system are controlled using tablet devices. Thanks to their touch interface and a highly intuitive menu, operators interact with all the warehouse shuttles, sending out movement orders to them from inside the forklift.
Goods management, a priority
In addition to achieving optimal storage capacity, WISAG’s priority in this project was error-free goods management. Accurate stock arrangement and organisation have a positive impact on warehouse activities, including the work of operators.
The company wanted to monitor the goods with precision from the moment they arrive in the warehouse until the orders are delivered to the customers. This required a warehouse management system (WMS) that would record all the products to ensure that they were easily located and identified at all times.
WISAG chose Easy WMS, the WMS developed by Mecalux, because it can get more out of all the activities carried out at the centre.
Easy WMS has been implemented in SaaS (Software as a Service) mode. This version is based on a high-performance Microsoft Azure cloud server infrastructure.
Easy WMS creates a virtual image of WISAG’s warehouse and divides it into two separate areas:
- Racks with Pallet Shuttle. The channels are 24 pallets deep, thus optimising the storage area. Operators use a tablet to control the four available motorised shuttles and, in turn, to communicate with the WMS in real time. This system is based on the LIFO goods management principle.
- Storage on the ground. There, the newly arrived pallets are grouped together before being placed on the racks while, at the same time, the pallets to be distributed are organised. Picking can also be performed if necessary. Operators use radiofrequency terminals to identify each product and follow the instructions given out by Easy WMS.
The use of radiofrequency terminals and tablets helps workers to concentrate on the operations and tasks that the WMS points out to them. The WMS sends them highly specific instructions on what to do with each product, and the workers confirm that they have complied with them to receive new orders. “The throughput is higher, and they make virtually no mistakes,” confirms Michael Lederer.
The WMS knows the inventory status of the goods in real time. To do this, it identifies each item as it enters the warehouse and automatically assigns it a location based on the SKU and demand level.
“Actually, Easy WMS operation is very simple, because the operators only need to read the barcodes using radiofrequency terminals for the WMS to tell them where to deposit the items,” says Michael Lederer.
Receipt
Easy WMS receives notification of the goods that will be arriving on the lorry and then generates and prints a label for each pallet.
Operators place these labels on each product and identify them with the RF terminals to enter the articles into the system. Once all the products have been checked, Easy WMS generates a report on the load received, which is then sent to the customer. This report specifies in great detail the product characteristics (batch, number of containers received, colour, type of pallet, etc.).
Dispatches
As far as dispatches are concerned, Easy WMS also organises pallet exits (around 500 per day). It tells the operators which pallets to remove from the warehouse and in what order to load them onto the lorry (according to the route the carrier will take when delivering the orders).
Once all the pallets have been placed on the lorry, the operators need to take a photo and send it to the customer so that the customer can check that the goods have been shipped safely and securely on the lorry. The radiofrequency terminals are equipped with a camera, and Easy WMS reminds the operator to take a picture.
Good communication
If there is one thing that characterises WISAG’s warehouse, it is coordination. All the operators work in synchronisation, storing the goods as quickly as possible.
To achieve greater efficiency and eliminate mistakes, the operators need to communicate with Easy WMS via tablets and RF terminals. With these devices, they receive orders from the WMS on how to manage the products in an orderly manner. As a result, WISAG is able to serve its customers with agility and expedite orders without delay.
With the success of this installation, the company foresees strong growth in the coming years. “Thanks to the support of Mecalux, we hope to move forward with more projects and expand the activities of our centre in Krefeld,” said Michael Lederer.
Michael Lederer - Director of the WISAG Logistics Competence Centre business unit
“The start-up of Easy WMS was a success because of the commitment shown by the Mecalux technical team. Now that the warehouse is operational, we have been able to confirm that this software is very practical and intuitive, bringing us a host of advantages, mainly in the control of goods.”
Advantages for WISAG
- Space optimisation: the Pallet Shuttle system makes use of the warehouse space and provides storage capacity for 10,695 pallets.
- Pallet control: Easy WMS gives operators precise instructions for error-free storage and dispatch of 1,000 pallets/day (500 incoming and 500 outgoing).
- Operation adapted to the customer: the WMS organises pallets according to the type of SKU and level of demand. It also ensures that orders include a photograph that shows the goods have been prepared properly for the journey.
WISAG’s warehouse | |
---|---|
Storage capacity: | 10,695 pallets |
Pallet sizes: | 1,000 x 1,200 mm |
Max. pallet weight: | 1,000 kg |
Rack height: | 9.5 m |
No. of shuttles: | 4 |
Gallery
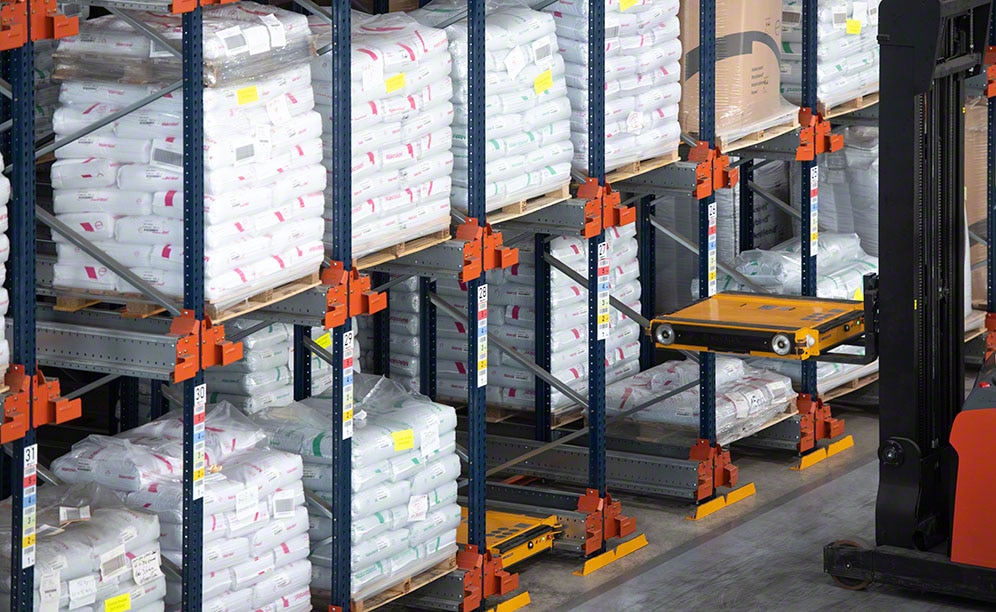
Semi-automatic Pallet Shuttle system in the WISAG warehouse
Ask an expert