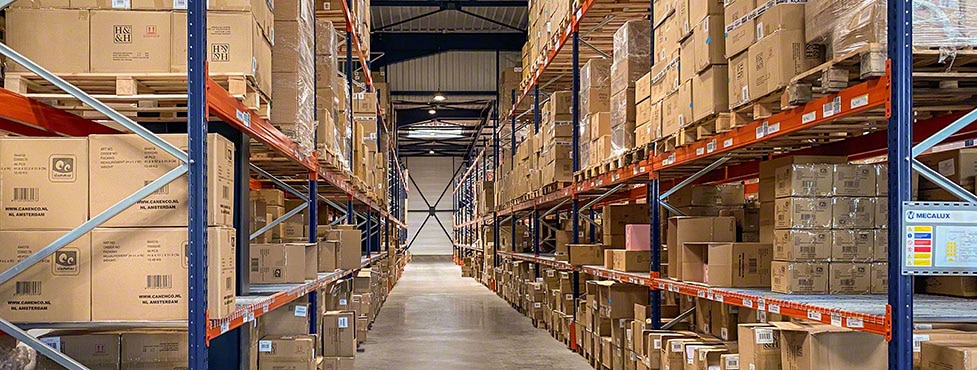
Kontiki perfects stock control and picking at its warehouse
The decorative items company has installed Mecalux's Easy WMS in its warehouse in France
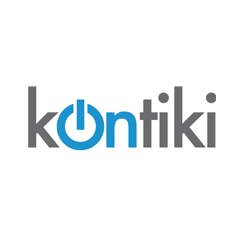
Kontiki, a French company that markets greeting cards and toys, has reorganised its logistics centre in Dommartin, near Lyon. Mecalux has proposed a comprehensive solution that has boosted Kontiki’s productivity as well as its business: pallet racking, a conveyor circuit and the Easy WMS warehouse management system. All this has minimised errors and optimised the control of the 2,400 SKUs that the firm manages.
Brands and SKUs galore
Kontiki was founded in 1994 with a view to distributing brands with strong sales potential. Diddl, an endearing mouse illustrated by designer Thomas Goletz, was one of the brands that helped Kontiki to establish itself in the market.
The firm has a large product portfolio, including paper and decorative items, collectable toys, fun gadgets and over 20 different brands, such as Plus-Plus, Heart and Home, Mani, History and Heraldry, Kimmidoll Collection and Keel Toys. Each of them follows its own marketing strategy and, likewise, has an extensive product catalogue for all ages. In recent years, Kontiki has expanded its distribution network so that this merchandise can be purchased at more than 3,000 sales outlets throughout France, such as toy and cultural shops, garden centres and service stations.
In Dommartin, 20 km from Lyon, the company has a 2,700 m2 warehouse where it deposits all its goods and prepares orders. Jérémy Barisci, Logistics Manager at Kontiki, explains, “For years, our goal has been to be more and more efficient and professionalise our supply chain. This challenge is daunting, as we manage multiple products from various brands and with different SKUs. Thus, we needed to better organise our business to know the exact location of each item.”
To perfect its logistics systems, Kontiki had to renovate its warehouse and “equip it with a solution that would help us to increase storage capacity and supply clients,” affirms Jérémy Barisci. Moreover, he points out, “We had already planned on implementing a WMS and automating goods management. Our objective was to be more productive, both in goods receipts and shipments.”
New warehouse, new logistics
Mecalux has installed 7-metre-high pallet racks that provide storage capacity for 1,712 pallets. Apart from direct access, this racking stands out for its ability to adapt to any type of load, weight or volume. This is fundamental for Kontiki, as it has 2,400 SKUs with different sizes and demand levels.
Mecalux has also installed a 16-metre-long conveyor circuit on one side of the installation. Its role is to automatically transfer the boxes of finished orders to the dispatch area, thereby streamlining goods movements. “The conveyor allows us to gain efficiency following the packaging phase. That is, once the orders leave the conveyor, they are ready to be dispatched,” states the Logistics Manager.
The racking and conveyor circuit stepped up warehouse operations, but that was not enough for Kontiki. What the company really wanted was to digitalise the management and control of all its processes and, hence, its products. Until recently, “We had been using the Navision ERP to organise all our business processes, including logistics. In the installation, however, we were relying on paper to prepare orders. Then, we would manually print the labels, together with the delivery note,” says Jérémy Barisci.
In terms of goods organisation, Kontiki lacked a defined, effective strategy; it merely sorted products by brand. “Operators would replenish stock at just the right time, when they found an empty location on their trips throughout the warehouse or when an order could not be completed due to lack of stock,” notes the Logistics Manager. This business is highly seasonal: products never remain on the shelves for too long.
Determined to modernise its supply chain, Kontiki chose to implement Mecalux’s Easy WMS warehouse management software “due to the excellent reputation of the Mecalux Group, recognised as a major industrial manufacturer in the logistics sector,” asserts Jérémy Barisci.
Jérémy Barisci - Logistics Manager at Kontiki
“We are very pleased about having chosen such a complete logistics solution that enables us to have a more efficient supply chain. Without it, we would not have achieved all the objectives we had set. The Mecalux team is extremely professional and receptive, and it was present before, during and after the commissioning.”
Enhanced stock control
“Since Mecalux’s Easy WMS started managing all our logistics processes, our installation has been less restrictive and more flexible. Consequently, most of the tasks are more agile and efficient,” enthuses Kontiki’s Logistics Manager after checking out all of Easy WMS’s functionalities.
The WMS provides full goods traceability from the moment the goods reach the warehouse. Before implementing Easy WMS and transforming its installation, the company managed 1,300 SKUs from all over the world. That number now stands at 2,400. Jérémy Barisci declares, “This growth has been made possible thanks to more accurate and real-time inventory control.” Optimal organisation of stock results in better use of space. By having access to all its indispensable products, the Company is now able to designate more locations to other types of items, thus, increasing the number of SKUs it handles.
Easy WMS has also had a direct impact on goods receipts. Each item incorporates a barcode that operators read with radiofrequency terminals. The system then decides where each product should be slotted. The process is extremely quick and — following instructions from the WMS — error-free.
Product restocking has also improved with the help of Easy WMS. “Operators no longer have to wait for a co-worker to replenish the items they need to finish preparing an order. Now, by controlling all the SKUs more effectively, the locations always contain the essential goods to avoid interruptions in picking,” says Jérémy Barisci.
Order preparation
Kontiki’s Logistics Manager contends, “Thanks to Easy WMS, operators are more independent when carrying out order prep tasks: SKU location, goods extraction, product grouping, consolidation, packaging, and printing of the transport label and order delivery note.”
Currently, the company prepares between 50 and 100 orders per day that are shipped to a wide variety of customers all over France. Operators pick the products from the racks following instructions from Easy WMS displayed on their radiofrequency terminals. “The simplicity and intuition of the radiofrequency devices facilitate the employees’ work enormously,” remarks Jérémy Barisci.
Once the order is finished and consolidated, it is deposited at the beginning of the conveyor circuit. The transport labels and delivery note are printed automatically at the end of the circuit. “Before using Easy WMS, we had to manually enter the relevant data in our ERP to print the delivery note and do the same in the carrier’s interface to print the transport label. All of this, which is now automated, used to amount to double the work,” observes the Logistics Manager.
At the same time, he notes, “Since we no longer need an operator to print the documentation, that employee can help his or her co-workers with the picking tasks.” All this enabled Kontiki to go from preparing 50 orders with four operators to more than 100 orders with five operators.
Easy WMS revolutionizes the installation
Kontiki’s new warehouse in Dommartin has adopted a personalised solution that lets it gain in efficiency and cut logistics costs by minimising errors.
The 2,400 SKUs with different sizes and demand levels are stored on pallet racks providing direct access to each one as well as versatility. The conveyor circuit automates the transfer of prepared orders to the dispatch area following instructions from Mecalux’s Easy WMS. The WMS, for its part, is responsible for managing all operations: goods receipts, storage, replenishment, order prep and dispatch.
The system carries all of this out with a user- friendly interface that “operators have quickly adapted to because it is extremely intuitive. Plus, the ability to customise the menus and simplify each operation has helped us to guide the workers and, thus, achieve maximum warehouse throughput,” assures Kontiki Logistics Manager Jérémy Barisci.
|
Before Easy WMS |
With Easy WMS |
---|---|---|
No. of SKUs |
1,300 |
2,400 |
No. of orders prepared/day |
50 |
100 |
No. of operators |
4 |
6 |
Advantages for Kontiki
- Greater number of SKUs: Kontiki has gone from storing 1,300 SKUs to 2,400 in a single space, thanks to the efficient goods organisation provided by Easy WMS and the transformation of the firm’s installation.
- Fewer errors and costs: Easy WMS has brought the number of mistakes made in picking and inventory management practically down to zero. As a result, it has also lowered Kontiki’s logistics costs.
Gallery
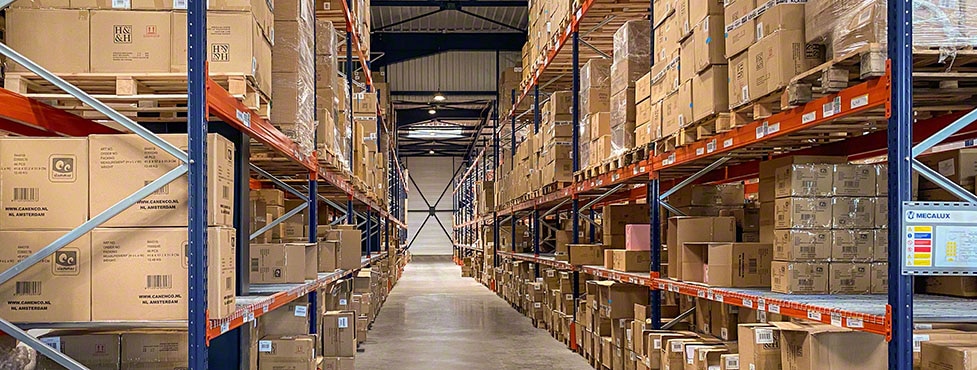
Kontiki stores paper products on pallet racks
Ask an expert