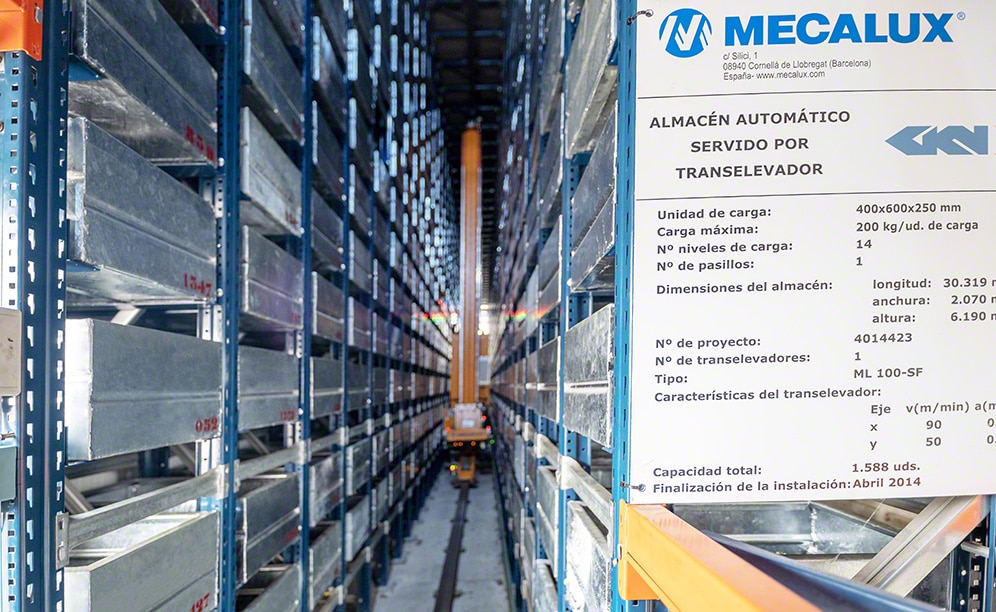
GKN Driveline’s automated warehouse connected to production and dispatch
Both automated warehouses for boxes manage second-hand automobile transmission parts
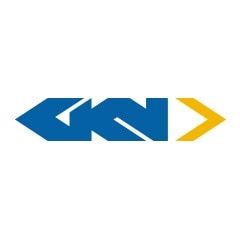
GKN Driveline has renovated its distribution centre in Carcastillo (Navarra), aiming to improve its logistics and provide its customers with more efficient services. Mecalux has installed two automated warehouses for boxes: one to supply production with materials needed each day and another to prepare orders that must be delivered to customers. These warehouses feature automatic storage tasks and, also, help operators put together up to 100 orders a day quickly.
Transmission solutions
Heading up its operations from its headquarters in the city of Redditch (UK), GKN is a multinational that focuses on manufacturing and distributing aerospace and automotive components.
GKN Driveline is one of its divisions and one which produces automobile industry solutions. As a leader in the sector, more than half of new cars sold worldwide are fitted out with GKN Driveline technology.
Currently, it owns and operates around 40 production centres spread throughout more than 20 countries. As far as Spain goes, it has two plants in the Basque Country and one in Barcelona, Navarra, Madrid and Galicia.
First glance at the Navarra plant
GKN Driveline makes transmission components for brand-new cars. Meanwhile, its plant located in the town of Carcastillo (Navarra) focuses specifically on repurposing used transmission parts from automobiles.
Since it started doing business more than 20 years old, this centre has experienced constant growth. Expansions were due to the company’s management searching for ways to grow that went beyond the typical move of setting up new production lines. From GKN Driveline’s point of view, logistics plays a key role in its business. Hence its keen interest in innovation and implementing overall operational changes to achieve greater flexibility, competitivity and to improve customer care services.
Initially, the company had the use of a single 1,800 m2 warehouse with pallet racks where it slotted 800 x 1,200 mm metallic containers. In 2011, it decided to renovate the warehouse and got in touch with Mecalux to get things rolling.
The first project comprised the installation of an automated miniload warehouse, allocated to raw materials and small iron transmission parts. The miniload system’s job is to supply transmission assembly and production lines with all the goods needed each day.
The following year, the distribution centre filled out operations with a second automated warehouse for boxes and pallet racks for the dispatch zone. Through these two systems, the company manages finished products ready to be sent to its end customers and to production plants that GKN Driveline has in France and Germany.
Recently, the company has added new picking stations in this latest automated warehouse for boxes that include a robot with artificial vision to prep error-free orders.
The two automated warehouses for boxes (both in production and dispatch) have brought about a more effective control over the goods in terms of box input and output processes, which, in the words of Guillermo Alonso, plant manager of GKN Driveline in Navarra, “has simplified product management and reduced logistics costs.” The reason being that a stacker crane is responsible for inserting and extracting boxes from their set locations speedily and with full autonomy.
Warehouse linked to manufacturing
Being well organised is crucial to provide the production centre with raw materials and components needed for assembly lines, when it comes to warehousing operations and the products. That said, this was not an easy task for the company since, according to Guillermo Alonso, “we carry a huge number of SKUs in our catalogue, around 5,000, give or take.”
Mecalux has constructed a clad-rack automated miniload warehouse, ideal for accommodating GKN Driveline’s multitude of SKUs. The racking must withstand its own weight and the weight of the goods, as well as the wall and roof cladding owing to the self-supporting construction. The advantage of this construction is that it makes full use of available space, both in length and from floor to ceiling, to provide better storage capacity.
The warehouse is composed of a single aisle with single-deep racking on both sides. They stand 6 m high and 34 m long and, overall, serve up a 1,592-box capacity, for 200 kg maximum unit weight crates.
Two picking stations are enabled on one side of the racks where workers collect products that must be sent to production. GKN Driveline’s ERP is crucial in supplying the assembly lines, seeing that it is connected to the WMS warehouse management system –in this case, Easy WMS of Mecalux–, to communicate what it needs.
The two picking stations have a monitor where Easy WMS shows operators how much product must be extracted from each box.“This system avoids errors in picking and has minimised assembly line timeouts,” underlined Guillermo Alonso.
Dispatch warehouse
The warehouse comprises a 57 m long aisle with double-deep racking on each side that, all together, provide capacity for 2,600 boxes. This installation has been expanded and modified over the last few years to adapt it to GKN Driveline’s changing needs.
Up to 100 orders can be prepared per day comprising long lists of order lines: between 500 and 1,000 per order. A picking station was installed on each end of the racks taking into account this specific work volume. A robot with built-in artificial vision features was set up in one of the picking stations to prepare orders, while in the other, operators do order fulfilment tasks. The company will drive autonomous order prep levels through using the robot. However, picking could not be completely automated because some more fragile items need manual handling by operators.
Optimised pick flows are one of this installation’s feature advantages. Previously, operators would move around the warehouse finding each SKU. However, with the miniload warehouse system, this operation is much, much faster and is based on the “product-to-person” pick concept. In other words, the operators remain at the picking station, and the stacker crane and conveyors move the goods up to the station’s location.
“Load accessibility and ‘product-to-person’ criterion have significantly reduced order prep and dispatch times, which has streamlined our whole customer care cycle,” pointed out Guillermo Alonso.
Product oversight
Easy WMS of Mecalux coordinates all logistics and operational processes of the two automated warehouses for boxes. The company runs multi-function management, like organisation of inputs, outputs, of locations, inventory and stock control, goods tracking and traceability, queries and statistical reports, etc.
Easy WMS is a perfect fit for GKN Driveline, by being able to control the endless amounts SKUs that it carries in its catalogue, all in real-time. To make this a reality, The WMS pinpoints products by units (those from the dispatch warehouse) and others as per their weight (those from the production warehouse).
The WMS updates stock statuses to manage the production warehouse’s products based on box weights. Once picking is completed, the box stops on a scale so the system can update each product’s weight automatically.
Guillermo Alonso - Plant Manager of GKN Driveline in Navarra
“The on-site business support and technical service that Mecalux provided us with were deciding factors, clearly showing we could rely on the product, in addition to the impelling sales quote Mecalux presented us. The automated miniload system is the most logical solution and which best adapts to our business.”
Advantages for GKN Driveline
- Efficient management: by having a production warehouse and another for dispatches, this prevents mix-ups and errors, plus guarantees solid customer care.
- Increased picking speed: the ‘product-to-person’ criterion has been vital in optimising and speeding up in-warehouse picking tasks.
- Stock organisation: the racks make full use of the entire warehouse surface aiming to accommodate storage capacity for more than 4,000 boxes filled with a plethora of SKUs.
Production warehouse of GKN Driveline | |
---|---|
Storage capacity: | 1,592 boxes |
Box sizes: | 400 x 600 mm |
Racking height: | 6 m |
Racking length: | 34 m |
Gallery
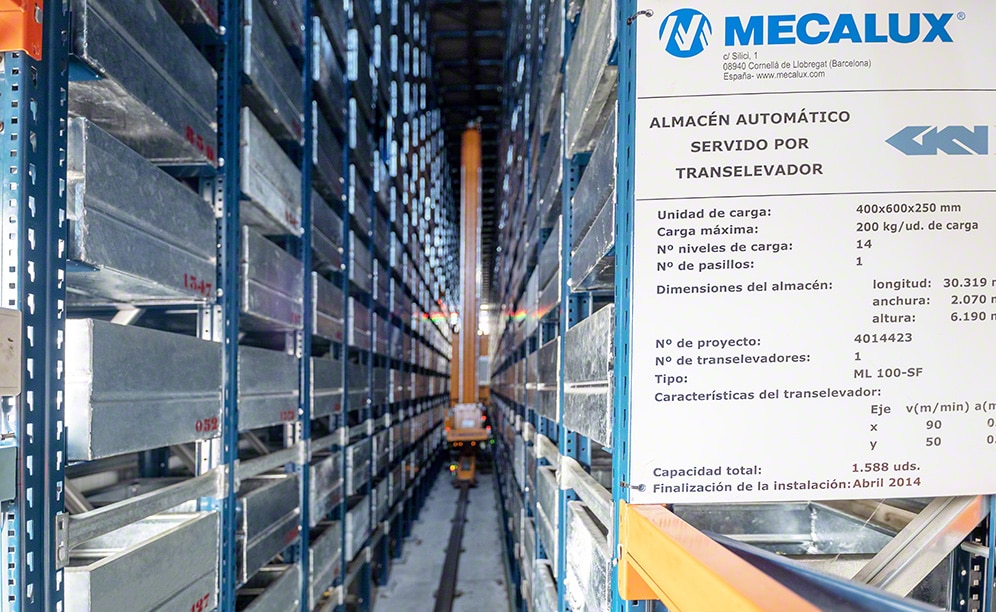
GKN Driveline’s warehouse connected to production and dispatch
Ask an expert