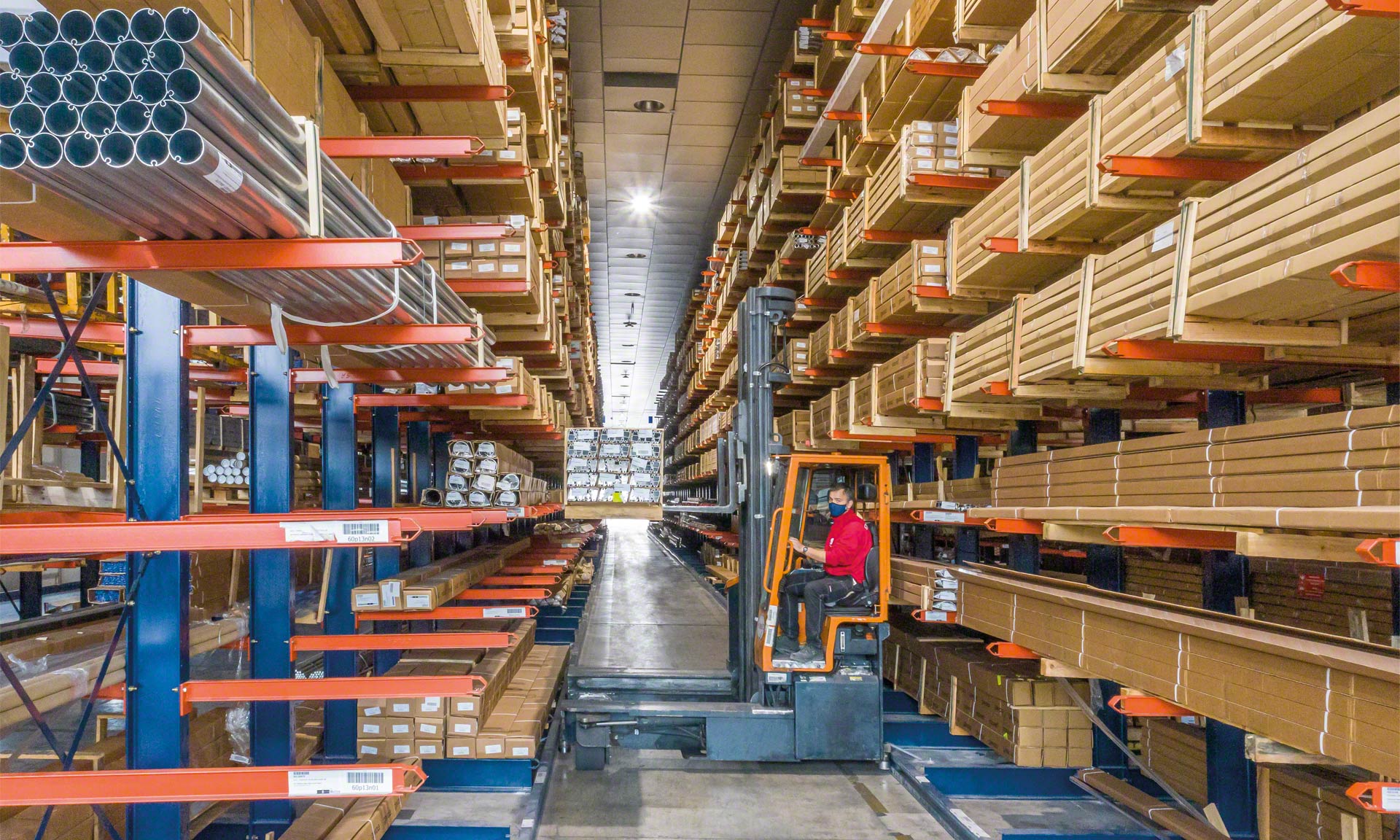
The perfect solution for storing extra-long profiles
Gaviota equips its warehouse with cantilever, pallet and drive-in racks
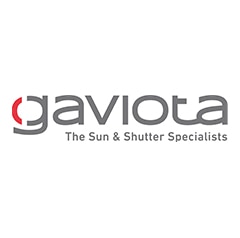
Multinational Gaviota is noted for its continuous development and clear commitment to modernisation, which have enabled it to grow by leaps and bounds over the years. Following this line, this leading manufacturer of smart blinds and awnings has decided to transform its warehouse in the town of Villena in Alicante, Spain, from top to bottom. Its objective is to optimise its logistics systems and prepare 450 orders a day with the aim of delivering them to its customers all over the world in the shortest time possible. To do this, Mecalux has equipped the centre with three different yet compatible storage systems: cantilever, pallet and drive-in racks. In total, the installation houses 4,600 SKUs of finished products and 12,800 SKUs of components used to make awnings, blinds and glass curtains.
High quality and design
Founded in 1968, Gaviota is a leading producer and marketer of accessories for blinds and awnings. The firm has continuously evolved over the years to become the benchmark manufacturer of sun protection systems for the construction industry. The business has eight production plants worldwide and is present in over 75 countries. With a staff of over 500, its strongest markets today are Spain, Italy, the US, France, Algeria, Brazil, Lebanon, Morocco, Mexico, Portugal, the Dominican Republic, Romania and Uruguay.
Gaviota is constantly growing. Roberto Urra, its Logistics Manager, explains, “The company’s drive makes it possible to undertake projects in new business lines that diversify and complement our extensive portfolio. This calls for the continuous adaptation of our installations and processes, as well as more complex warehouse management.”
Against this backdrop, the firm needed a supply chain that was flexible and robust enough to cope with the rise in both demand and SKUs. Therefore, it decided to reorganise its warehouse in Villena (Spain) to accommodate the increasing number of SKUs of different sizes, types and turnovers.
To bring this project to fruition, “We contacted Mecalux, and we did so for several reasons: the price-quality ratio of its products, the attention paid to us by the sales rep, the fast turnaround times and its good reputation in the market,” indicates Roberto Urra.
In terms of logistics, the business is noted for managing a wide variety of items of different sizes: up to 4,600 SKUs of finished products, 12,800 SKUs of components in pallets and boxes, and profiles measuring four, five, six and seven metres long. With this in mind, Mecalux proposed equipping the installation with a combination of storage systems: cantilever, pallet and drive-in racking. This personalised solution enables Gaviota to organise all its products based on their demand level and particular characteristics.
Warehouse organisation
Order is one of the most effective means of achieving an efficient logistics system, and this, of course, was a priority for Gaviota. Thanks to the proper distribution of its products, the warehouse operators can locate the SKUs they need more quickly and, thus, prepare and dispatch orders in less time.
Gaviota’s warehouse is divided into two installations within the same space. In the words of the Logistics Manager, “One of them is for profiles, where we have the cantilever racks; the other is for pallets, stored on adjustable racks and high-density drive-in racks.”
Each building is independent, with its corresponding loading and unloading areas. There, operators receive goods sent from production or by suppliers, and, simultaneously, orders are dispatched. Each installation also carries out its own storage and order prep operations.
The goods in both warehouses are organised based on different criteria. According to Roberto Urra, “In the installation for profiles, these are classified by length, and those with the same length are grouped by weight. The warehouse for pallets meanwhile, is divided into two areas: on the one hand, we have the awnings line, and, on the other, accessories for blinds. Meanwhile, in each of these two areas, we’ve installed drive-in racks, where we store high-turnover items, and pallet racks, where we do picking and sort products by weight.”
Cantilever racking: ideal for extra-long and heavy loads
- Very long unit loads. They are specifically designed for storing bulky loads of varying lengths, such as the profiles managed by Gaviota.
- Simple structure. The racks are formed by columns to which a series of arms (that hold the loads) are attached.
- Versatility. The cantilevered arms fit together simply, so their position can be modified based on the dimensions of the goods.
- Direct Access. Operators can easily handle the profiles and visually monitor each of them.
Varied operations
Gaviota’s warehouse stands out for its incessant work pace. In addition to managing so many SKUs, operators must deal with the daily arrival of a large number of goods: 550-700 pallets and 125-200 profile packages, depending on the season. Most items come from Gaviota’s production plants in Spain and Lebanon, while several others are sent by external suppliers, mainly in Spain.
At the same time, 600 pallets and 150 profile packs are dispatched every day. Roberto Urra notes, “In total, 40% of these orders are dispatched to Spanish customers. The other 60% are shipped to customers in the rest of the world, especially in Algeria, the US, France and Italy.”
Nevertheless, the most demanding operation is order preparation. Every day, operators strive to put together and dispatch around 450 orders in only two working shifts (three during summer months).
Roberto Urra points out that three types of orders are prepared: “those with single profiles, boxes or full pallets.” In the profile warehouse, operators pick the profiles they need directly from the three lower levels of the racking. The upper locations are used to store profile packs that serve as reserve goods or can be shipped in full.
In the building for pallets, meanwhile, workers can pick full pallets to be dispatched or boxes. In the case of the latter, the operators walk around the warehouse, locating the SKUs they need and directly removing the boxes from the pallets on the lower rack levels. Additionally, orders made up of single units are prepared in an area set up for this purpose. Gaviota’s Logistics Manager affirms, “The direct access provided by the pallet racks is critical for operators to be able to prepare orders quickly.”
Order and competitiveness
Gaviota’s warehouse in Villena stands out for its orderliness and optimal goods organisation. As a result, all operations are much more flexible, and its 17,400 SKUs are kept under strict control.
“Believe it or not, with the pandemic, our workload has increased, even surpassing other years,” remarks Roberto Urra. The cantilever, pallet and drive-in racks have helped the company to achieve a logistics system that is much more streamlined and committed to its clientele. The firm is now able to supply the 450 orders placed by its customers as expeditiously as possible.
Roberto Urra - Logistics Manager at Gaviota
“At our warehouse, all products are organised based on various criteria such as characteristics, weight, profile length and turnover. Plus, the cantilever racks are the only ones that can store our 4-to-7-metre-long profiles”.
Advantages for Gaviota
- Expanded storage capacity: the cantilever, pallet and drive-in racks take up nearly the entire warehouse surface area, providing the maximum possible storage capacity.
- Goods organisation: the products are distributed based on size and demand. For example, the profiles are grouped according to length and weight.
- Optimal picking: operators prepare 450 orders a day made up of single profiles, boxes and full pallets. The direct access to the racks facilitates goods handling and, thus, ramps up the throughput of this operation.
Cantilever racking | |
---|---|
Storage capacity: | 3,480 loads |
Load size: | 4,000 / 7,000 x 600 mm |
Max. load weight: | 600 kg |
Racking height: | 8 m |
Gallery
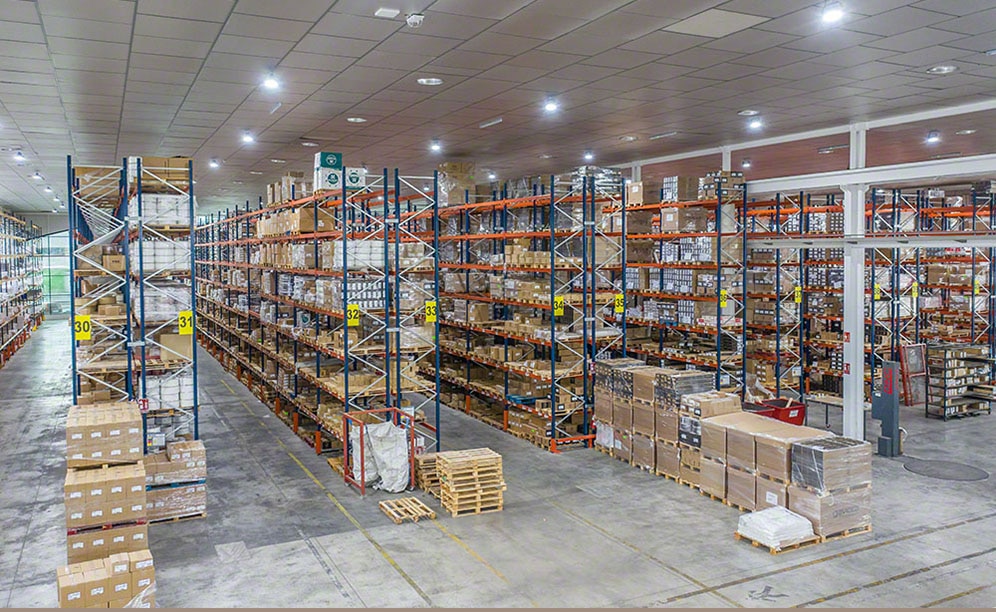
Gaviota's three storage systems at its warehouse in Villena (Spain)
Ask an expert