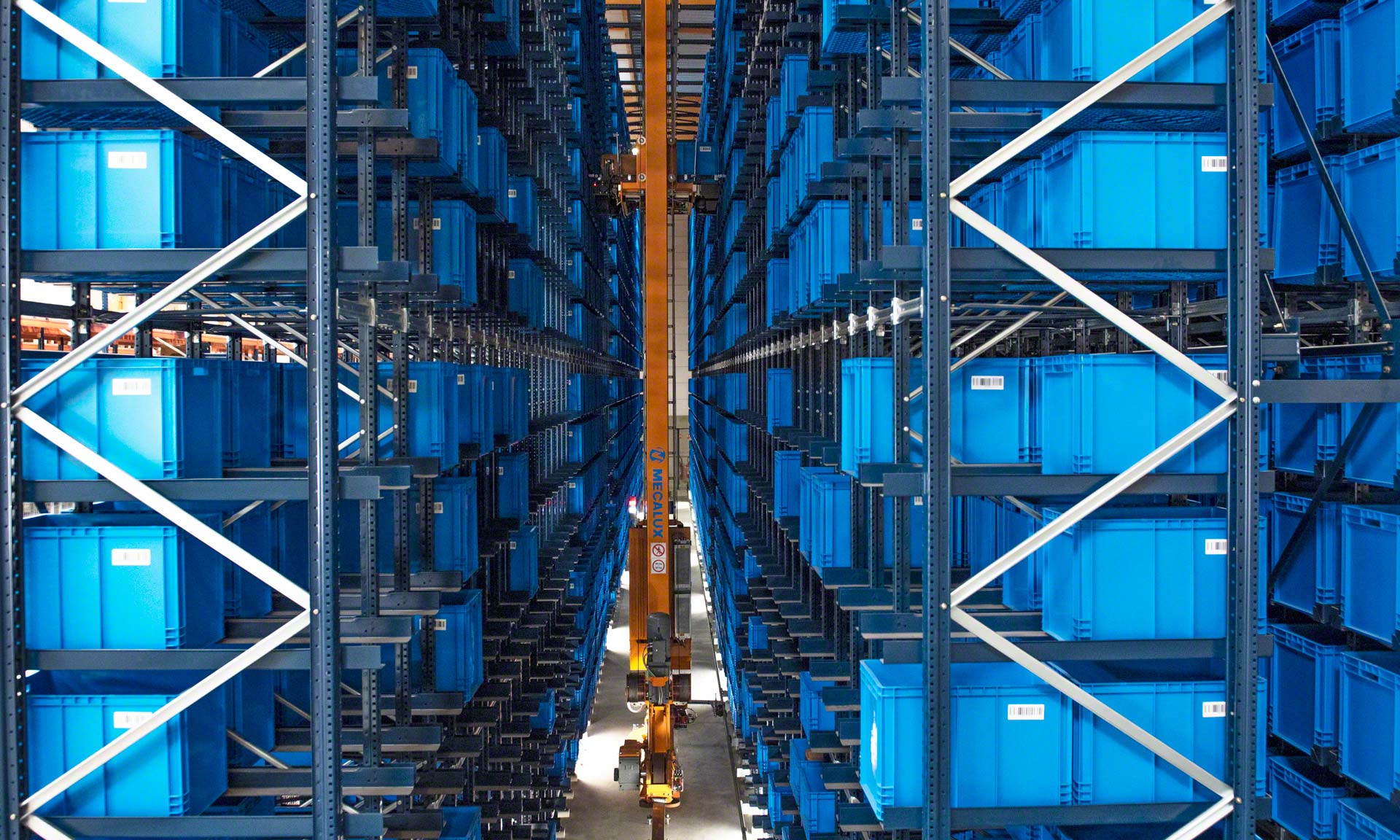
FIC: 60% of SKUs stored in 5% of floor space
Easy WMS has improved inventory management and the quality of FIC’s service to end customers in just a few months
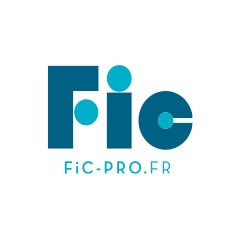
Concentrating a large portion of SKUs in a small space streamlines flows and reduces warehousing costs. FIC, a French company specialising in products for construction professionals, has centralised its logistics operations in a new facility near Nîmes (southern France) equipped with three storage systems to manage 12,000 SKUs. Mecalux has installed an automated storage and retrieval system (AS/RS) for boxes in addition to pallet and cantilever racks that can adapt to any type of good. Automation, overseen by Mecalux’s Easy WMS warehouse management system, has boosted picking and improved both inventory management and the quality of FIC’s service to end customers in just a few months.
Ever-expanding
Founded in France in 1965, FIC is a company specialising in products for professionals in the construction sector such as air conditioning and ventilation equipment, plumbing and water treatment materials, personal protective equipment, hardware and electrical materials.
Thanks to its extensive network of sales outlets throughout France (in cities such as Avignon, Montpellier and Nîmes, among others), industrial workers can find more than 40,000 SKUs of all the products they need to do their jobs.
This family-run business has experienced continuous growth, thanks to the work and dedication of its 310 people on staff. From the start, FIC has constantly adjusted to technology changes in the market, maintaining excellence and prioritising quick responses to customers. This is illustrated by the fact that, in 2019, its turnover exceeded €80 million (£68 million).
Logistics under one roof
After the rise in sales in the past few years, the company came to the conclusion that it had to bring all its logistics operations together to continue growing. “Before, our supply chain was decentralised, with all the goods spread out among different warehouses, which really complicated management,” says Yannick Taton, Logistics and Transport Manager at FIC.
The firm decided to relocate to a 3-hectare site in the south of Nîmes. There, it has built an 8,332 m² modern logistics centre where it stores all its goods (around 12,000 SKUs). “Our products run the gamut when it comes to size: from bulky products on pallets to small items in boxes. We needed a logistics solution that would help us to organise them in the best possible way and facilitate storage and picking tasks,” says Taton.
With these requirements in mind, FIC contacted Mecalux because, according to Taton, “we’d already outfitted other warehouses with its racks, and it offers good value for money. More than a supplier, Mecalux is a partner with whom we can discuss our issues and our desire to improve. We’re pleased with the different storage solutions from Mecalux because they meet our needs.”
After analysing FIC’s requirements, Mecalux proposed a highly personalised, comprehensive logistics solution in which traditional systems with bulky products would coexist with an AS/RS for boxes housing smaller SKUs. Taton says: “We visited several warehouses of other companies, and we realised that we’d obtain very good results with automation. We also thought it would be positive for our business because it would speed up the preparation of orders made up of small items.”
The automated warehouse needed to be managed by a WMS that would control all operations, reduce errors and provide maximum traceability of the goods. Taton says: “Our logistics centre is equipped with latest-generation technology that helps us to provide the level of service we want our customers to receive. Our priority is to deliver them the perfect product at the right time and at the best price.”
Characteristics of the AS/RS for boxes
Mecalux has installed a 10-metre-tall miniload system with two aisles spanning 38-metres-long and with double-deep racking on both sides. The 19 storage levels in the racks have been personalised to accommodate boxes of two different heights: 240 and 420 mm.
One of the particular features of this solution is that it leverages the space to maximise storage capacity: in just over 330 m², FIC houses 10,679 boxes. “We manage 60% of all our SKUs in the AS/RS for boxes, taking up only 5% of the logistics centre's surface area,” says Taton.
To store and remove boxes from the racks, Mecalux has installed two twin-mast stacker cranes for boxes that incorporate telescopic forks to work efficiently in double-deep racking. Following instructions from the Mecalux Group’s Easy WMS warehouse management system, all the goods arriving at the facility must go through a checkpoint to verify that their weight and size meet the established requirements.
“Easy WMS is a warehouse management system outfitted with all the functionalities you need to organise the receipt, storage, preparation and shipment of goods. Plus, the software has been seamlessly integrated with our Evolubat ERP system,” says Taton.
Picking twice as fast
“Another reason we’re so thrilled with the AS/RS for boxes is that, compared to manual warehousing systems, it’s doubled our throughput in order prep and storage tasks. It’s enabled us to reduce our labour costs and improve the quality of our customer service,” says Taton.
Two pick stations have been set up at the front of the facility. There, orders are prepared according to the goods-to-person method. This working method has resulted in considerable savings in picking times, as, previously, FIC operators had to go through the warehouse to locate the SKUs that make up the orders. Now, stacker cranes and conveyors bring the products to the pick stations automatically.
At each pick station, equipped with RF scanners, six orders are prepared simultaneously. To avoid mistakes, Easy WMS tells the operators which goods they need to remove from the boxes and sort into orders. Specifically, the workers deposit them on picking shelves outfitted with put-to-light devices. Located on the front of the shelves, they display the number of SKUs to be placed in each box. Once the operator has deposited the product, he/she presses the confirmation button to inform the WMS that the task has been completed and to receive more orders.
Finished orders are placed on a pallet, which is then sent to the consolidation area located in front of the loading docks. In addition, some of these orders are finished with items from the pallet racks.
Every day, 125 orders are prepared, each made up of about 17 lines. In total, the warehouse dispatches between 150 and 180 pallets.
Bulky goods
FIC’s facility is also equipped with pallet racks with capacity for 4,832 pallets. With four storage levels, the racks measure 10 m tall and the aisle 54 m long. “The pallet racks from Mecalux can be customised according to the product characteristics. Thanks to Mecalux’s after-sales service, we’ve also made changes and enhancements to the structure of the racks as our business evolved,” says Taton.
In this vein, Mecalux placed mesh panels on most of the lower levels of the racks to be able to accommodate the boxes. Picking is done along the lower levels, while the upper levels house reserve products to ensure that the warehouse always has the required goods on hand.
Mecalux also installed 10-metre-tall cantilever racking, specially designed to store heavy, extra-long unit loads such as bars, profiles, pipes and timber. This solution guarantees direct access to the goods and also stands out for its versatility in being able to adapt to large products.
Logistics with a present and a future
Taton explains, “The investments made in logistics and transport will allow us to continue growing both geographically and structurally, conquer new markets and develop new business.”
The centralisation of FIC’s logistics operations has been completed successfully: the company now has an efficient, sustainable logistics centre that will enable it to provide quality service as well as bolster its growth plans. “The various storage solutions from Mecalux have been adapted to the different types of products we manage. They’ve also helped to optimise the work of the operators and ensure full traceability and safety in all processes.”
We’re pleased with the different storage solutions from Mecalux because they meet our needs. The miniload warehouse is like a Formula 1 car: it just needs to be set up and adjusted to reach peak performance. The first few months of use are key for achieving smooth operations. We now have a logistics centre equipped with latest-generation technology that helps us to provide the level of service we want our customers to receive.
Advantages for FIC
- Floor space optimisation: in just 5% of the warehouse’s surface area (330 m2), FIC is equipped with a completely automated solution for 10,679 boxes, i.e., for 60% of the total number of small SKUs.
- Cost savings: the centralisation of the logistics processes has cut FIC’s costs while improving the management of its entire supply chain.
- Storage of extremely varied goods: the company has a single warehouse that houses 12,000 SKUs of different sizes (including boxes, extra-long pipes and profiles, and palletised merchandise).
Cantilever racks | |
---|---|
Max. racking height: | 10 m |
Gallery
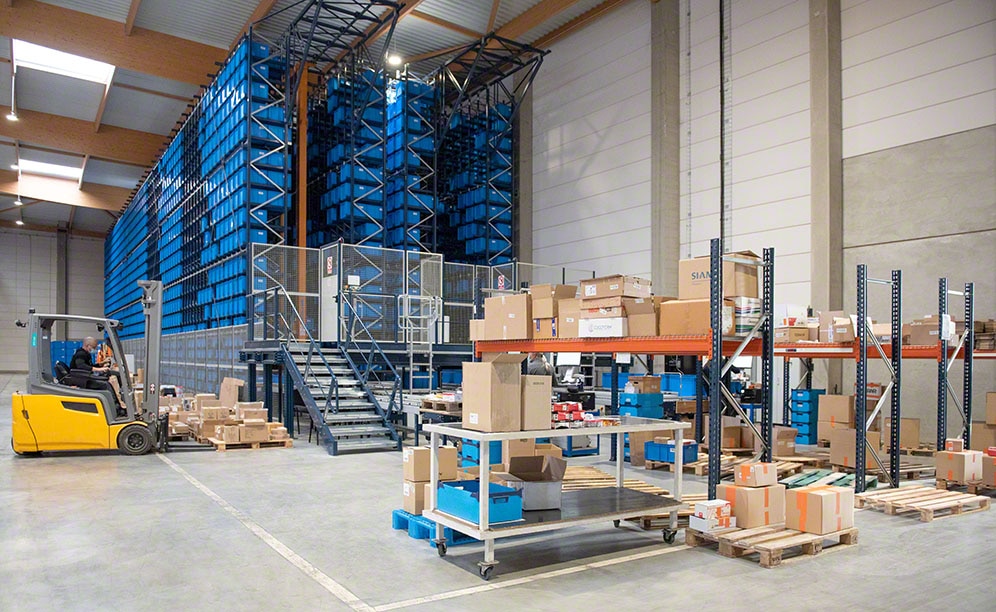
FIC warehouse with products for professionals in the construction sector
Ask an expert