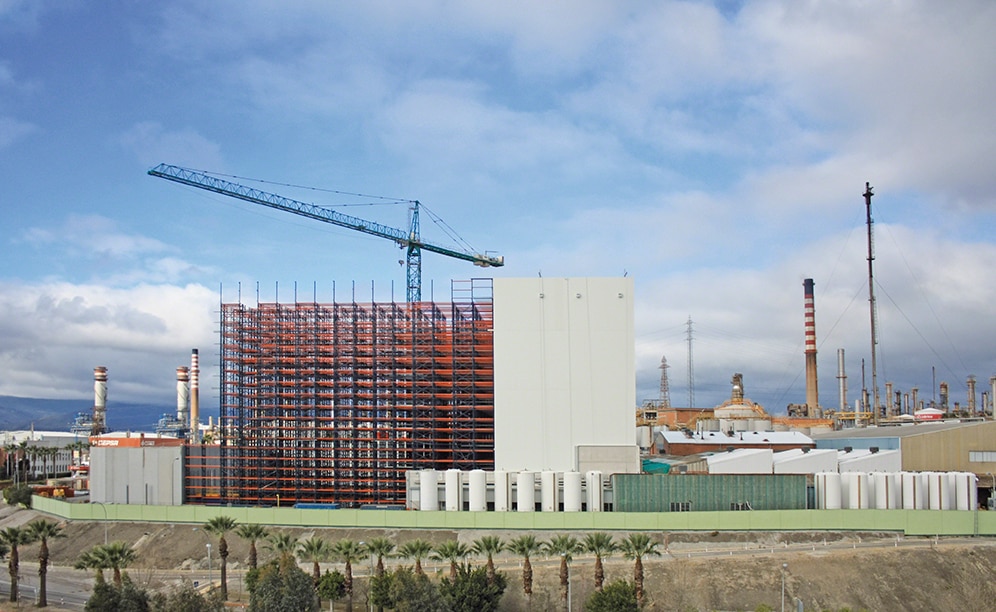
Next-generation automated clad-rack warehouse: a sure bet to streamline of logistics processes at Cepsa
Cepsa: a success story about the integration the lubricants logistics
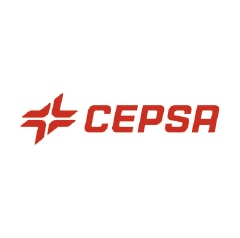
The energy company Cepsa entrusted Mecalux with the construction of a 37 m tall automated, turnkey warehouse in its lubricants production facility in the town of San Roque (Cádiz). The Mecalux Easy WMS warehouse management system has also been included in the set up, and is responsible for managing all the activities of the centre.
About Cepsa
Cepsa is an energy group, 100% IPIC, which employs more than 10,000 professionals to carry out their activity in all stages of the hydrocarbon value chain: oil and gas exploration and production, refining, transportation and sale of petroleum products and natural gas, biofuels, cogeneration and commercialisation of electric energy.
The company has developed an important petrochemical niche, which is highly integrated with oil refining. The company focuses on the manufacture and sale of raw materials for the elaboration of high added value products. These are used mainly for the production of new generation plastics and biodegradable detergents. They enjoy a notable presence in Spain and, through progressive internationalisation, do business on several continents, marketing their products worldwide.
Needs of Cepsa
The company had high logistics costs because, unlike the raw material warehouse, its finished products warehouse was a distance from the production plant.
To address this situation, Cepsa contacted Mecalux with the aim of building a new automated warehouse with the largest possible capacity in the area occupied by their conventional warehouse and maintenance workshops. In addition, it was essential to have picking stations that would enable them to expedite order preparation.
Automation should start at the end of each production line, so that operators only perform operations that demand manual intervention.
It was necessary to consider the different models and pallet sizes, as well as how to store Euro-pallets directly on the racks, in these sizes: 800 x 1,200 mm, 1,000 x 1,200 mm, 1,150 x 1,200 mm and 1,200 x 1,200 mm.
At the same time, they took into account the arrival and subsequent storage, mainly from abroad, of different sized pallets than those specified. A portion of these pallets contain products essential for production, so the warehouse also had to provide its delivery to this area.
Another Cepsa requirement was that all phases of warehouse development and construction, including the supply of the software necessary to properly manage all the internal operations, be carried out by a single company. In short, the turnkey project needed to be built from start to finish without stopping product manufacturing.
Characteristics of a turnkey warehouse
The Cepsa turnkey warehouse included the following prerequisites:
- Development, implementation and legalisation of the project, considering all the parts that make up the warehouse, and taking into account the different applicable regulations.
- Demolition of the existing installations where the warehouse would be located, as well as its subsequent conditioning.
- Preparation of the terrain and the construction of the concrete slab and the perimeter walls. All of this with the resilience and planimetry ideal for this type of warehouses.
- Supply and installation of the racks, as well as the structures necessary for the construction of the clad-rack warehouse.
- Supply, assembly and commissioning of handling equipment: stacker cranes, conveyors, checkpoints, devices to facilitate picking and all ancillary elements needed.
- Supply and assembly of the warehouse enclosure panels, both the facade and roofing.
- Construction of an annex building, where the reception areas for outside goods, warehouse outputs, P&D stations are located.
- Supply and installation of the fire protection system inside the warehouse and annexed areas, taking into account existing regulations. In this case, Cepsa already had both the water tank and the pumping equipment required in the facility.
- Install fire doors to act as a barrier between the warehouse and the annex buildings that operate automatically in the event of a fire.
- Electrical installation.
- Warehouse Management System (WMS). This system must be connected to the ERP or Cepsa’s main computer system to exchange commands and information.
A clad-rack warehouse as a solution
From the beginning, Mecalux collaborated closely with those responsible for the different structural engineering areas and the logistics management of Cepsa to determine which solution would best suit the needs of the company.
After a detailed analysis of all the specifications provided, Mecalux proposed building a 37 m tall, automated clad-rack warehouse with capacity for more than 28,000 pallets in a surface area of only 4,150 m².
Having limited space, they proposed to perform inflows that go directly to the warehouse from the end of the production lines, and dispatches on the opposite side. Separating input and output areas is not a widespread practice, but in Cepsa’s case, it turned out to be the best solution.
In a clad-rack warehouse, the racking is a fundamental part of the building’s structure, where cladding is placed. In addition to its own weight, it must withstand the pallets stored, the force of the wind, the handling elements, earthquakes on the basis of the coefficient indicated in the construction site and the corresponding weight of snow as per regulations.
The pipes of the fire system are installed and attached to the racks themselves. Thereby, they are protected from occasional blows and provide correct spraying of the pallets.
So that all operations function correctly, the Mecalux WMS Mecalux warehouse management system was installed, responsible for managing and controlling all the centre’s logistics operations.
Inside the warehouse
There are seven aisles, with double-depth racks placed on both sides. An almost 34 m tall, twin-mast stacker crane — with double-depth telescopic forks — circulates in each aisle.
It is 19 racking bays long and 18 load levels high and can hold, depending on the model and size, two or three pallets each.
An extra location was set up on each level starting on the third and up to level 18 that coincides with the conveyor input and extraction points, placed at the ends of each lane.
Production conveyor
Inputs of finished products are made on this side, although there are also outputs for complementary product required for production.
Once the goods are palletised, the system installed by Mecalux takes charge of the pallets. It deposits them in the warehouse and performs their subsequent delivery to the P&D stations from the production line exits.
If the layout of this page is analysed in detail, it is clear that, in addition to the production area which coincides directly with the back of the warehouse, there is a space reserved for the packaging of IBC containers (specific to the storage and transport of liquids). This area is also connected to the warehouse via a second transfer car and the production conveyor itself.
Dispatch conveyor area
Direct output conveyors are set up facing the loading docks (five using chains and three with rollers), allowing the pallet to be positioned on the most appropriate side.
The inflow of goods from the exterior is performed on this side. To do this, the conveyor system and other necessary elements were installed; including the possibility of elevating unsuitable quality and sized pallets on top others in good condition.
In addition, there are picking stations in this area with the appropriate handling equipment and an open space to install two more stations if needed.
A transfer car also serves as a liaison between the different positions.
Picking area
It is installed between the main conveyors and the group of elements that comprise the inflow station from the docks. There are two picking stations and each one of them has:
- A "U" shaped circuit attached to the main conveyor system and with triple pallet capacity sourcing (two of them on standby).
- A work platform with access to all four sides of the pallet that is in the central position. This is where the picking operation itself is performed.
- Three allocated pallet positions for preparing orders, three at a time. Its location is on the opposite side of the work platform.
- A vacuum lifter for boxes hung from the upper structure, capable of moving in all three directions. This avoids manual handling of mainly the heavier boxes.
- A computer terminal and two printers.
This is an open area scheduled for duplicate picking stations.
Pallets with prepared orders are introduced, using the transfer car, into the inflow station for pallets coming from the exterior. These pallets are strapped during an automatic process before going to standby positions inside the warehouse, or directly to the assigned output channel. In both cases, they move via the main conveyor system.
Easy WMS management system: the nerve centre of the installation
The Easy WMS controls all processes to do with inflows, warehouse locations, stock, slotting rules, storage and extraction, the pallets that should go to picking stations, the picking itself, warehouse returns, etc.
Galileo, the control software by Mecalux, orders the movements of the different devices and machines. In addition, it controls the status of the elements that make up the whole conveyor circuit, the stacker cranes themselves, their internal and external safe usage and the other elements that interact with them.
As a highlighted aspect, it has developed a high level of integration between the IT systems of the new warehouse and that of Cepsa. The latter includes the ERP (SAP) and MES (SEP-PAP) applications that completely manage the purchase of raw materials, manufacturing, inventory control and business processes. Easy WMS automatically receives, through specific interfaces, the information on the products that are being manufactured, the needs for raw materials for manufacture, the reception of orders from suppliers or customers' orders. This high degree of integration minimises errors and ensures that operations are performed automatically.
Finally, a bar code reading system allows verification during dispatch so that the products being loaded are those ordered by the customer.
Advantages for Cepsa
This new warehouse built by Mecalux for Cepsa provides the following advantages:
- High storage capacity in a small space: the clad-rack warehouse enables the placement of 28,630 pallets in a 4,150 m² surface.
- Cost savings: the automation of the clad-rack warehouse and a direct connection to the production lines has allowed Cepsa to boost efficiency while reducing personnel and logistics costs.
- Complete control: thanks to the Mecalux Easy WMS, Cepsa controls all the processes and operations that occur inside the warehouse.
Automated turnkey warehouse in Cádiz, Spain | |
---|---|
Storage capacity:: | 28,630 pallets |
Maximum pallet weight:: | 1,000 kg |
Warehouse height:: | 37 m |
No. of stacker cranes:: | 7 |
Stacker crane type:: | twin-mast |
Fork type:: | double-depth |
No. of transfer cars:: | 3 |
Constructive system:: | Self-supporting |
Gallery
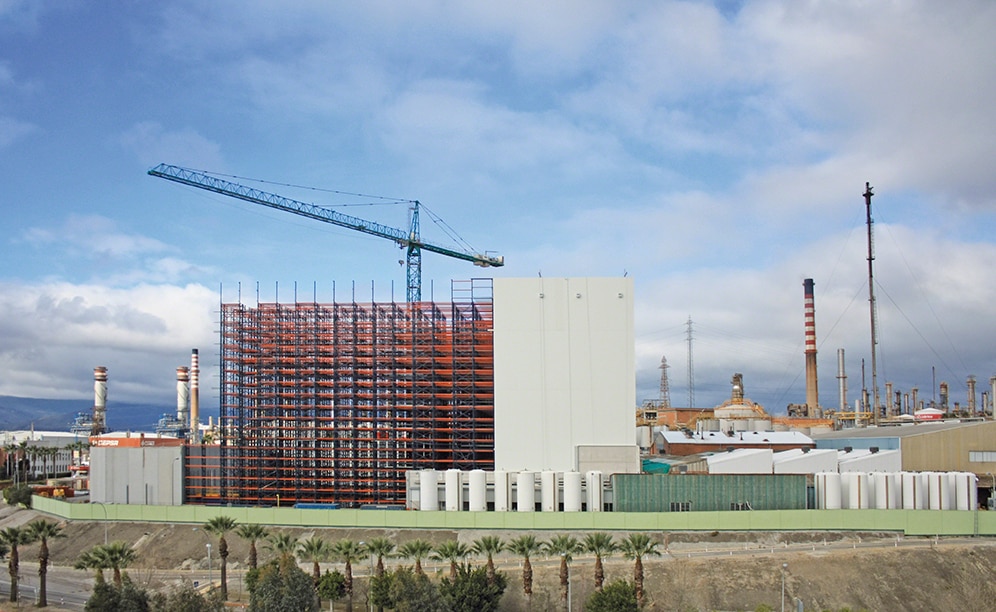
Mecalux builds Cepsa a 37-metre tall automated warehouse with capacity for more than 28,000 pallets
Ask an expert