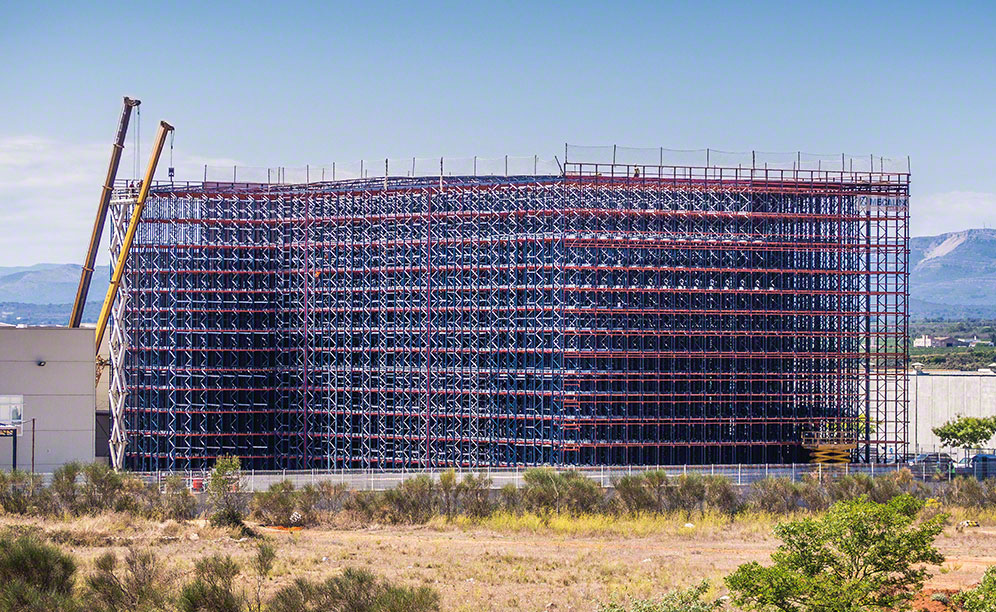
Laboratorios Maverick automates its Deliplus product warehouse
The warehouse, set up next to the production centre the company has in Tarragona, is fitted with cutting-edge technology and runs the Mecalux Easy WMS.
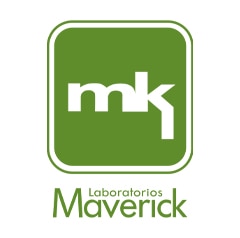
By being fully-automated operations-wise, Laboratorios Maverick’s clad-rack warehouse was able to cut order prep and delivery times by half, optimising each lorry’s load volume. The warehouse, set up next to the production centre the company has in Tarragona, is fitted with cutting-edge technology and runs the Mecalux Easy WMS.
Laboratorios Maverick (Ubesol Group)
Laboratorios Maverick, founded in 1991, is a specialist in the development and manufacture of hygiene and personal care products.
Since 1995, it has worked as an exclusive Mercadona supplier and makes a huge variety of eco-friendly, socially responsible products, including: bath gels, deodorants, hand soaps, hair-removal and shaving products, intimate hygiene, other hygiene and hair care products, as well as baby care products. The company has two large manufacturing centres, one in San Fernando de Henares (Madrid) and another in Ulldecona (Tarragona).
Combined solutions
Although the highlight of Laboratorios Maverick’s facility is the massive automated clad-rack warehouse, other storage solutions were also installed that are just as essential for the whole logistics process to run smoothly:
- Automated clad-rack warehouse for finished products.
- Pallet racks for raw materials and highly-flammable products.
- Live pallet racking run by a stacker crane allocated to prepared orders.
- Sequencing buffer for pallets that must be restacked automatically to optimise the volumetric capacity of transport vehicles.
In tandem, handling equipment was supplied (stacker cranes, pallet lifts, transfer cars, etc.) and the Easy WMS of Mecalux rolled out. “The logistics centre is equipped with a computer system that runs 24-hours a day, all year round,” explains Hugo Marante, departmental operations coordinator of Laboratorios Maverick. “Data transmission flows through a sophisticated high-speed fibre-optics network and includes infrastructures that minimise downtimes,” he adds.
Hugo Marante Departmental Operations Coordinator at Laboratorios Maverick “Through this new warehouse, we automated our storage tasks and reduced the time we normally needed to prepare and distribute each order, all of which translates into better, more efficient logistics for our company.”Automated clad-rack warehouse
Finished product is stored here. As a clad-rack construction, the warehouse yields high capacity without losing access or speed while goods flow in and out. The company went with a compact storage system because its customer Mercadona works with very few SKUs, but an usually high number of each of these SKUs.
Palletised goods include bottled gels, shampoos and creams that are stored as per the ABC rotation criteria.
The warehouse fills a 3,878 m2 area which adds to Laboratorios Maverick’s already 33,000 m2 large manufacturing centre. It is comprised of racks that stand 26.5 m high, with 14 different load levels for storage.
Inside the warehouse, three 70 m long aisles were enabled for a twin-mast MT3 stacker crane to run along. Each stacker crane, capable of 24 simultaneous combined-cycles each hour, is supplemented by a shuttle that transports pallets up to the open position in the aisle, as indicated by the Easy WMS warehouse management software.
According to Hugo Marante, “to optimise the automated warehouses’ operations, management systems were integrated into all processes (manufacturing, quality, storage and dispatch) in a single platform.”Pallet racks: raw materials and flammable products
Raw material to make products is stored next to the automated warehouse in some pallet racks, as well as packaging and auxiliary materials.
Another zone inside the manufacturing plant houses pallets filled with highly-flammable products, like aerosols used in deodorants and hair sprays. Laboratorios Maverick complies with the specific standards that certify that its work area, as well as the operation of the handling equipment, have been devised, utilised and maintained with respect to all safety criteria dealing with flammable products.
Overall, 45 blocks of pallet racks were installed, featuring fourteen 8 m high storage levels.
Sequencing buffer for the full-pallet stacker
The sequencing buffer, connected to the automated warehouse, is set between the standard pallet racks and some live pallet racks allocated to finished orders. It comprises a conveyor circuit and functions as storage for pallets that must be stacked.
The sequencing buffer also receives pallets from the CPS (Chemical Product Storage), so these pallets can be stacked during order preparation.
Live pallet racking run by a stacker crane for finished orders
Here, the company houses finished orders waiting and ready to be shipped out. With three levels of storage, the live pallet racks can absorb up to 88 incoming pallets per hour flowing either from the sequencing buffer (conveyor circuit full pallet stacker), or the automated warehouse.
The high-performance single-mast stacker crane with an onboard roller conveyor inserts pallets into the live pallet channels (on a 4% incline), which facilitates the pallets’ gravity displacement from the higher to the lower part.
Live pallet racks offer precise product rotations thanks to the FIFO system (the first pallet inserted into the channel is the first to be extracted).
The side in which pallet inputs and outputs are done in the live pallet racks coincides with the dispatch area. With this setup, lorries can be loaded directly from the racks without any need for pre-loading manoeuvres.
The Easy WMS combines pallets coming directly out of the automated warehouse with pallets in the sequencing buffer to make up orders and, by doing so, optimises lorry volumes. Grouping and sequencing goods for shipments according to their route, lorry, customer, delivery order and other variables reduces dispatch times.
Hugo Marante - Departmental Operations Coordinator at Laboratorios Maverick
“Through this new warehouse, we automated our storage tasks and reduced the time we normally needed to prepare and distribute each order, all of which translates into better, more efficient logistics for our company.”
ADVANTAGES FOR LABORATORIOS MAVERICK
- More capacity in less space: the automated warehouse offers the highest storage capacity possible in only 3,800 m2.
- 30 minute orders: the automation of logistics processes means Laboratorios Maverick can prepare an order in just a half an hour, cutting task times by more than half.
- Efficient management: the Easy WMS manages and organises all operations being carried out inside the warehouse, reducing logistics costs, minimising errors and raising the bar on efficiency and order preparation productivity. These benefits have led to the load volume optimisation of each transport vehicle.
Automated warehouse of Laboratorios Maverick | |
---|---|
Pallet size: | 800 x 1,200 mm |
Max. pallet weight: | 1,000 kg |
Racking height: | 26.5 m |
Aisle length: | 70 m |
Storage levels: | 14 |
No. of stacker cranes: | 3 |
Gallery
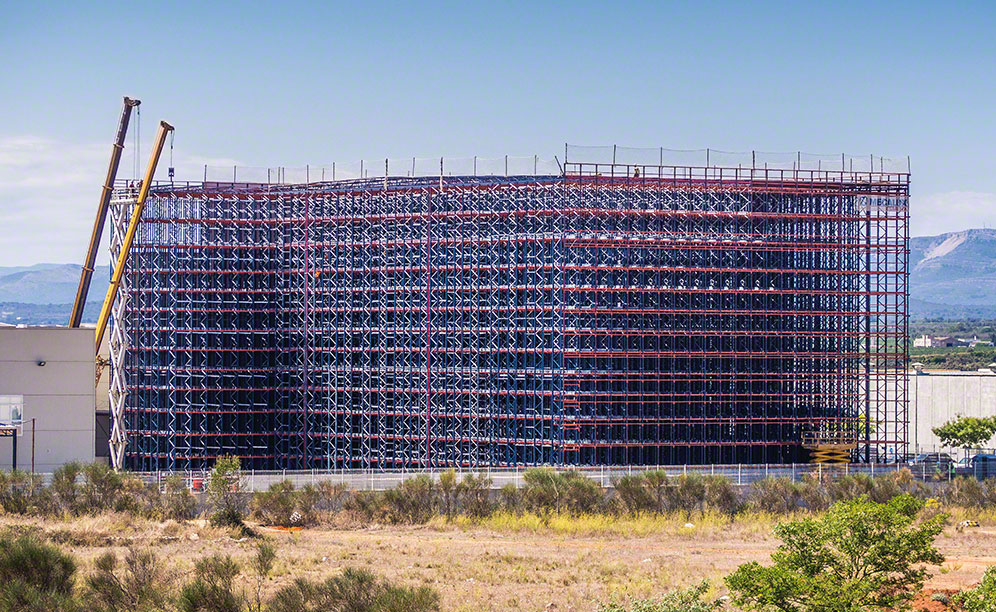
Automated clad-rack warehouse of Laboratorios Maverick
Ask an expert