College of DuPage: a solution that’s just the right size
College of DuPage has optimised its warehouse space with the help of push-back racks
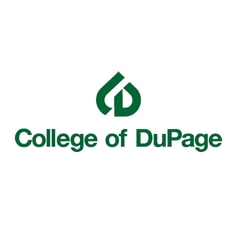
College of DuPage’s warehouse in Glen Ellyn, Illinois, is not a typical installation. As opposed to managing raw material or finished products, it stores goods for very specific end customers: the college’s students, faculty and staff. With over 28,000 students, College of DuPage is the second-largest provider of undergraduate education in the State of Illinois. The 110-hectare campus of Glen Ellyn has 11 buildings and a warehouse where it stores a large amount of paper and supplies.
Needs of the client
College of DuPage used to store its products on pallet racks, which had become overloaded in the face of so much material. In addition, they were so tall that they almost reached the ceiling; “whenever we put anything up there, we had to be really careful that we wouldn’t hit lighting or sprinkler heads,” says Angelo Conti, supervisor of warehouse services at College of DuPage.
The height issue also made it impossible to deposit full pallets on the upper level, so operators had to break them down. All of this was time-consuming for operators and, therefore, increased labour costs for College of DuPage.
Interlake Mecalux’s proposed solution
After consulting various storage systems manufacturers, College of DuPage hired Interlake Mecalux to design and instal push-back racking to solve the problem posed by the old racking units. “Interlake Mecalux was able to identify the specific product that would help us and our requirements,” affirms Conti.
College of DuPage has optimised the space in its warehouse by installing push-back racks. These systems minimise the number of aisles needed to access products, creating a high-density, high-efficiency solution. The pallets are deposited on top of a set of trolleys that are pushed along slightly sloped rolling rails. The trolleys can be from one to five pallets deep, depending on the application and available space.
When the operator, aided by a forklift, removes the first pallet, gravity pulls the remaining pallets forward towards the working aisle, ensuring that the front position is always full. With this system, pallet extraction is simple and agile, as well as safe for operators. This was an essential requirement for College of DuPage, even more so considering the problem caused by the former racking. “Sometimes we just need one case of paper, and with our old system, you’d have to reach in the rack to grab that case of paper. So, for us, not having to put a person in the rack underneath thousands and thousands of kilos was a big plus. It’s just the fact that you’re eliminating the potential for injury. You can’t really put a price tag on that,” emphasises the warehouse services supervisor.
The installation of push-back racks has also solved College of DuPage’s warehouse height issue. In comparison with the standard racking that had been used in the warehouse, the push-back racks have one storage level less because the top level was no longer practical. “We are now able to store full pallets of paper without breaking them down. Now, they can just be taken off the truck and put on the racks,” explains Conti.
All these benefits have resulted in considerably reduced logistics costs for the institution. The push-back racking solution saves the college from having to purchase specific handling equipment to move pallets. Instead, operators can now use a smaller forklift to access the products from the working aisle. They no longer need to reach inside the storage lanes, which decreases the risk of structure damage to the racks, increases safety in the installation and reduces maintenance to a minimum.
Another aspect to bear in mind is that the racks had to support the full weight of the pallets laden with paper. Each trolley in the rack can withstand up to 1,500 kg, which is ideal for companies that work with heavy loads.
One of the aspects that most impressed Conti when starting up the warehouse renovation project was Interlake Mecalux’s responsiveness to the university’s needs. College of DuPage has very strict requirements and conditions for selecting its suppliers, and Interlake Mecalux was able to provide the university with the information it required to make the wisest choice.
Angelo Conti - Supervisor of Warehouse Services at College of DuPage
“Personally, what I liked is the customer service that I received and how Interlake Mecalux was able to work with our unique situation. Interlake Mecalux worked with me and understood our requirements and was able to provide the information I requested.”
Advantages for College of DuPage
- Optimisation of space: push-back racks leverage space without sacrificing efficiency in goods management.
- Warehouse safety: the storage system installed ensures safe pallet extraction, doing away with the need to reach into the racks and minimising any risk of accidents.
- Cost savings: operators no longer have to break down full pallets, saving time and personnel costs for the College of DuPage.
- Resistant racking: the push-back racks can support the heavy paper-laden pallets, each holding up to 1,500 kg.
College of DuPage’s warehouse | |
---|---|
Storage capacity: | 96 pallets |
Pallet sizes: | 1,000 x 1,200 mm |
Max. pallet weight: | 1,500 kg |
Rack height: | 3.5 m |
No. of storage levels: | 3 |
Gallery
Ask an expert