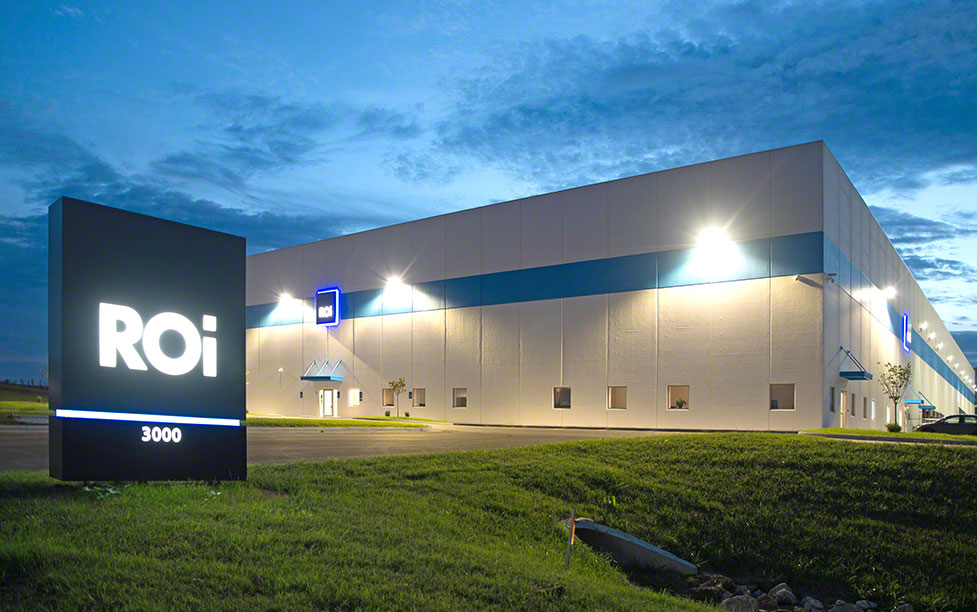
A warehouse to manage a healthcare product supply chain
The new Roi warehouse in Missouri: an efficient supply chain to handle healthcare products
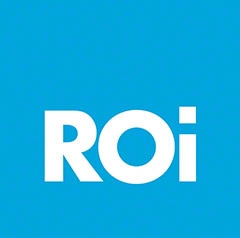
ROi has opened a brand-new logistics centre in Missouri (USA) specifically to prepare kits needed by healthcare professionals to perform medical procedures. Equipped with a three-level high-rise picking tower, said modules comprises pallet racks and push-back racks by Interlake Mecalux. The company has tripled the number of kits that were prepared in its prior distribution centre by using all of these solutions.
About ROi
The Mercy Healthcare System, one of the largest non-profit healthcare organisations in the USA, knew it needed to update its supply chain to provision hospitals with the required materials and instruments faster. Resource Optimization and Innovation (ROi) is a cost-management supply solutions organisation started by Mercy Healthcare in 2002.
ROi administrates all operations of Mercy Healthcare System’s supply chain. Its objective is to supply medical personnel with the instruments they use to perform procedures.
Needs of ROi
ROi’s Custom Pack Solutions (CPS) is the kit prep division of ROi for custom packs that hold supplies needed by doctors. Initially, they were assembled in its 9,100 m2 logistics centre in Springfield, Missouri. It has experienced exponential growth every year since its inception. Today, the program averages more than 630,000 kits produced each year.
A new 30,480 m2 centre was opened in Republic, Missouri to deal with this work volume. The centre is set aside for the storage and distribution of medical and pharmaceutical materials, as well as for the assembly of medical and surgical kits. ROi worked with Interlake Mecalux and material handling solutions provider LD Systems to equip the new facility with the material handling systems needed to reinvent ROi’s custom procedure tray (CPT) manufacturing process.
Different storage systems
High-rise picking blocks
A three-storey, 8.5 m high pick module stands right in the middle of the warehouse. A conveyor circuit runs through each level.
One side of the high-rise picking bays is made of pallet racks, which offer a 152-pallet storing capacity. On the other side, live pallet racking was installed where up to 234 pallets are housed.
Operators walk the aisles picking the products directly from the pallets for each order and set them on the conveyors. Once the orders are prepared, they are moved to a consolidation area to, later on, be sent to the production lines which have requested these items.
Pallet racks
The warehouse also includes six, 3.5 m wide aisles with single-depth pallet racks on each side. The 7 m high racks can hold 2,800 pallets that are 1,000 x 1,200 mm in size on four storage levels. Each pallet unit can weight up to 900 kg.
This direct-access pallet solution streamlines stock management and speeds up material handling during storage and picking labours.
The racks are adaptable to any product volume, weight or size and provide versatility for facilities like ROi’s, which has wide varieties of product types and 2,200 different SKUs. Moreover, racks include accessories to adjust the shelves to each load’s dimensions.
Push-back racks
This section of racking has four levels and three aisles that are 3.5 m wide on either side. Standing 7 m tall, overall, they house up to 1,200 pallets.
Push-back racks are available in two-, three-, four-, and fivedeep pallet designs. Sets of lanes are arranged on a slight incline (the front is somewhat lower, meaning gravity moves the pallets forward to the aisle).
Forklifts do not enter the storage lanes, since both pallet loading and unloading is done from the same side of the work aisle. Thus, forklift traffic is kept to a minimum, and there is a dramatic acceleration of the material handling times.
Rick Parrish - Director of Manufacturing at ROi
“We are very satisfied with our multi-solution storage in the kit centre because it allows us to pick more materials with less staff and be much more scalable as we grow kit volumes.”
Advantages for ROi
- Increased productivity: the new kit-friendly warehouse will enable ROi to triple its production compared to its previous centre.
- Streamline all operations: the direct access provided by the storage system facilitates and boosts order picking and pallet inflows and outflows.
- Space is king: the warehouse’s surface is equipped with various solutions that yield top capacity storage.
Pallet racking | |
---|---|
Storage capacity: | 2,800 pallets |
Racking height: | 7 m |
Gallery
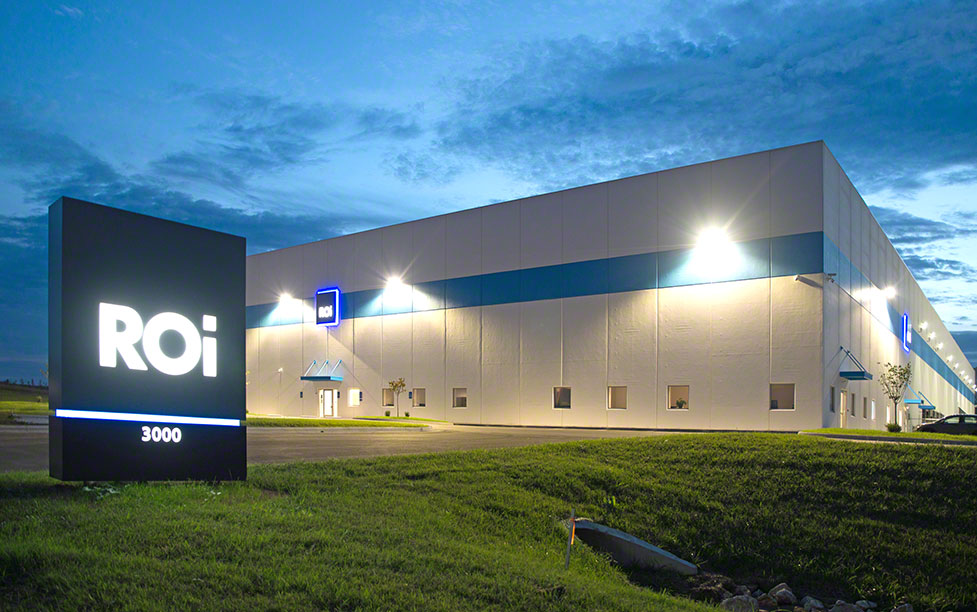
Pallet racking, push-back racking and high-rise pick bays in the ROi warehouse
Ask an expert